Adept white paper – Adept PLC User Manual
Page 2
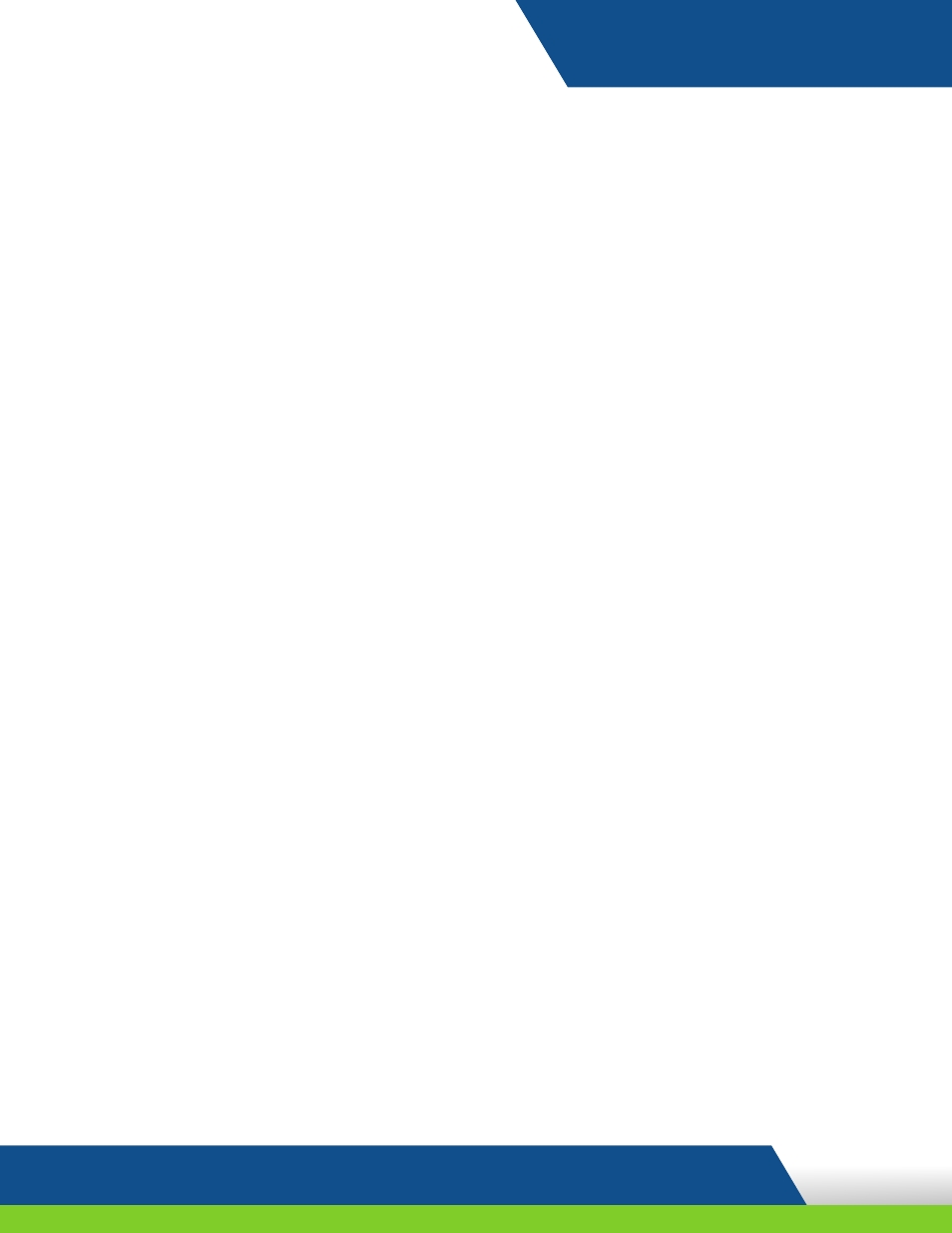
Historically the users of robots have relied on the robot manufacturer, an integrator, or third party consultant
to set-up and train the workers. This support may not be local to the end-user and more importantly can be
challenging to orchestrate, delaying installation and adding extra costs. Once set-up and training is scheduled,
even a single robot installation & subsequent employee training sessions can take days.
PLC Robot Programming
Robot manufacturers studying their customer’s needs and understanding what knowledge support personnel
already possess have developed new methods to more easily deploy and program robots. Specifically, new solutions
utilizing the end-user’s existing knowledge of Programmable Logic Controller (PLC) software have been met with
increased adoption. Originally developed for the automotive industry, PLCs have been used by many industries
for a wide variety of machines for nearly 30 years and are therefore familiar control interfaces in most production
and manufacturing settings.
“With the ePLC, the robot becomes another peripheral device rather than the basis of the machine that
everything else has to be built around. We, and many of our customer’s maintenance staff, already know how
to program PLC ladder logic,” said Scott Gerold, senior software specialist of NACS, Inc a leading automation
integrator. “Leveraging that knowledge to program a robot just makes sense. We save both time and money with
regards to training internal engineers. We are able to keep the machine interface and user experience consistent
which also saves time on the technical documentation and customer training as well.”
Robot manufacturers and integrators have developed several options to use the PLC to automate robotic cells
including offering emulation solutions, robot & new PLC hardware & software, and robot software that works
directly with the end-user’s existing equipment.
Robot plus new PLC Solution
One solution has evolved from partnerships between robotic manufacturers and PLC manufacturers. Working
together, these manufacturers offer packages whereby the end-user purchasing a robot from the robot
manufacturer then purchases their desired PLC from a PLC manufacturer. These two components work together
to program the robot using familiar PLC Ladder Logic software. Additional components may also be required
such as servo amplifiers and potentially some additional software education depending on how custom the PLC
is to the robot. While this solution does leverage the end-user’s knowledge, it does require separate purchases and
potentially additional training.
Emulation Solution
Another solution from robotic manufacturers has been the development of software that emulates PLC Ladder
Logic software. While emulating PLC software attempts to shorten the learning curve associated with robot
software, it still requires the end-user to install and learn new software in order to program the robot. This
solution usually requires end-users to purchase multiple licenses from multiple vendors.
Leveraging Existing Equipment
Another solution introduced over 5 years ago is a unique solution that allows end-users and integrators to take
ownership quickly by utilizing the end-user’s existing PLC when deploying a robot. Although the original
deployment of Adept Technology’s ePLC Connect software was designed to be centric to Allen Bradley’s PLC,
which makes up 70-80 percent of the US market, it has since been shown to integrate with Schneider Electric
(formerly Modicon) and Siemens’ PLC’s.
ADEPT WHITE PAPER
PLC Robot Programming: Familiar Programming, Reduced Costs of Implementation and 21 CFR Part 11 Compliance
2