Boyertown Cox Heating Products Commercial Furnace User Manual
Page 7
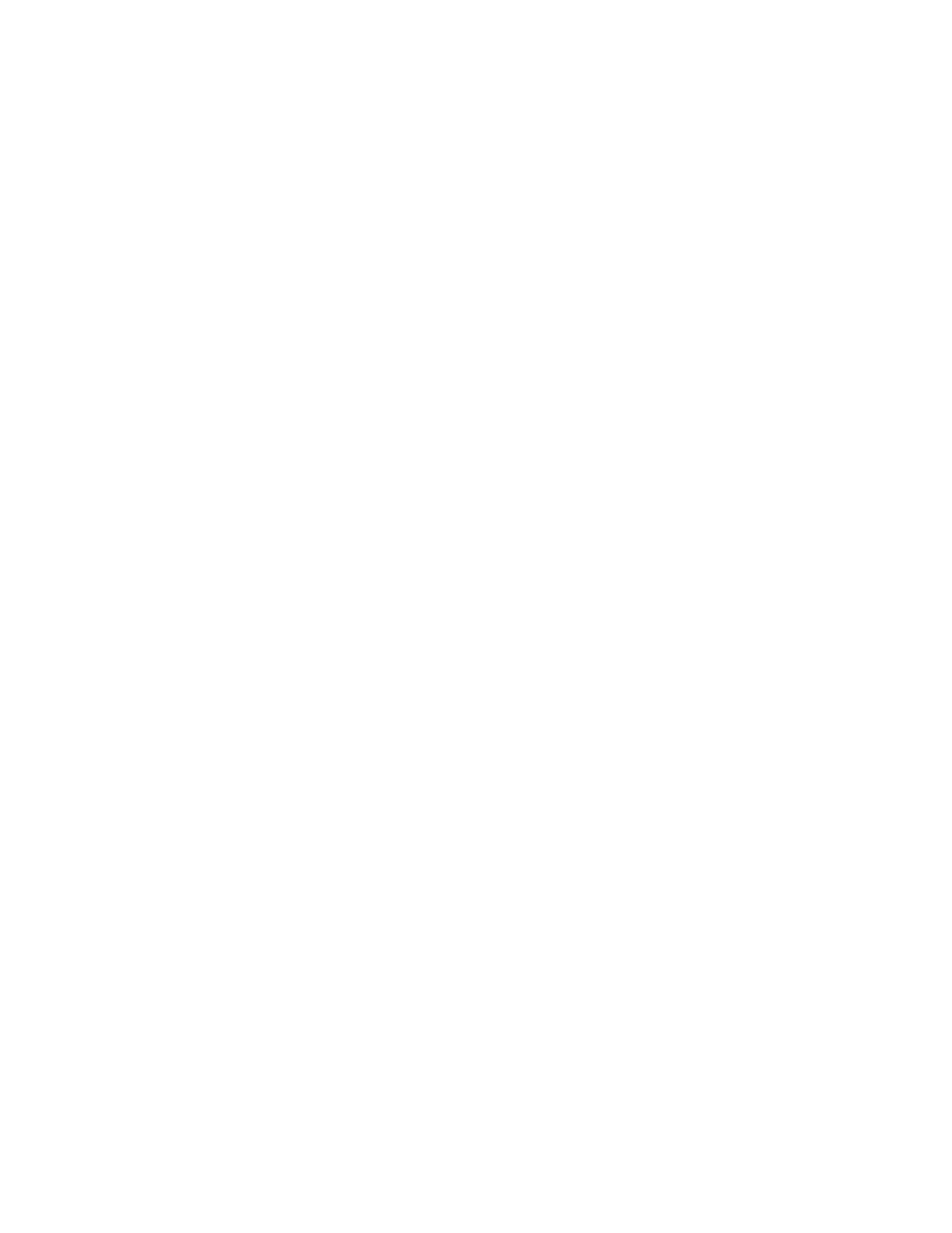
7
flue-
flue
the
e of
ore
the
the
the
s
f
t
l
opening may be used for
ocedure – The test procedure is as follows:
1
e burner shall be operated and the fuel rate
2
3
er operation.
Combustion – There must be openings into
Size – The burner shall be of adequate size for the
heating load as
rner certificate by the
ded by
e installer on the oil burner certificate to be placed
1) CO2 – The CO2 in the flue gas by analysis
ed when the stack
temperature is measured.
nk is buried underground, all pipe
nnections should be arranged so they will not be
oken if the tank should settle. Always use a good
e.
E. Burner Installation
OIL
Equipment – The following equipment shall be
available on each oil burner installation before the
tests are started:
1) Where the oil rate is not indicated on the
nozzle tip, a suitable device for determining
the rate in terms of gallons per hour fed to the
burner shall be used. This may be in the form
of a graduated glass vessel.
2) A suitable flue gas analyzer for determining
the percentage of CO2 in the flue gases.
3) A suitable draft gauge graduated in
hundredths of an inch of water.
4) A suitable thermometer to indicate the
gas temperatures.
5) Provision for inserting a thermometer in
pipe as follows: Not more than 12” from
furnace outlet, measured on the center lin
the flue pipe, there shall be a hole not m
than ½” diameter, located at the side of
pipe on the center line so that
thermometer may be inserted horizontally.
The thermometer is to be placed so that
ensitive element is one fourth of the pipe diameter
rom the far side of the flue pipe. The opening around
he thermometer shall be sealed to prevent air
eakage. This same
checking draft and sampling flue gases.
Test Pr
) Th
adjusted to that required for the particular
installation.
) The draft then shall be adjusted to meet the
burner manufacturer’s specifications, both over
the fire and at the breeching. Refer to
“Installation Instructions” Section, B.
) Combustion air adjustments are to be made to
give the highest CO2 without visible smoke
(unburned carbon) at the chimney. If the
minimum required percentage of CO2 cannot be
obtained in the breeching, it will be permissible
to take CO2 over the fire, which will be
acceptable. In this event, both CO2 readings
shall be recorded after 10 minutes of operation.
Readings – During the period of operation to permit
flue gas temperature to reach maximum, periodic
readings of draft CO2 and oil rate shall be taken and
the average recorded on the certificate.
All controls and limiting devices shall be checked
for prop
Air for
the furnace room to admit free air to maintain
combustion, minimum opening of not less than twice
the area of flue outlet of furnace.
furnace and the connected
mended on the oil bu
recom
installer. Models and Firing Rate : See “Furnace
Specification” Section.
Certificate – Following installation of the burner,
certain test data shall be obtained and recor
th
with each oil burner installation. The test shall cover
the following points: CO2 in the flue gas by
analysis, draft, stack temperature, firing rate, and
smoke.
Requirements – The standard requirements as
approved by the industry as follows:
shall not be less than 8%.
2) Draft - The draft shall be in accordance with
specifications in the manufacturer’s
installation manual. An automatic draft
regulator or its equivalent is required.
3) Stack Temperature – The stack temperature
shall be measured on the furnace side of
automatic draft regulator and not more than
12 inches from the smoke connection. The
stack temperature shall be measured at the
certified firing rate. If an automatic draft
regulator is built into the furnace, such
regulator shall be clos
4) Firing rate – The firing rate shall be based on
the burner manufacturer’s recommendation
for the existing total connected load. Burner
shall be fired at that rate.
5) Smoke – During the above test, there shall be
no visible smoke at the chimney.
6) Installation Manual – The burner shall be
installed in accordance with manufacturer’s
installation manual.
Fuel Tank Connections – Pipe connections between
fuel tank and the oil burner should be made with 3/8”
copper tubing and brass fittings, however, galvanized
pipe is quite satisfactory. All joints should be sealed
with key paste or other good oil resisting compound,
and pulled up tight. Where fuel tank is installed in a
basement, a one-pipe system to the burner will be
found entirely satisfactory.
When fuel ta
co
br
leak-proof check valve in the suction lin