Flowserve Mark 3 User Manual
Page 29
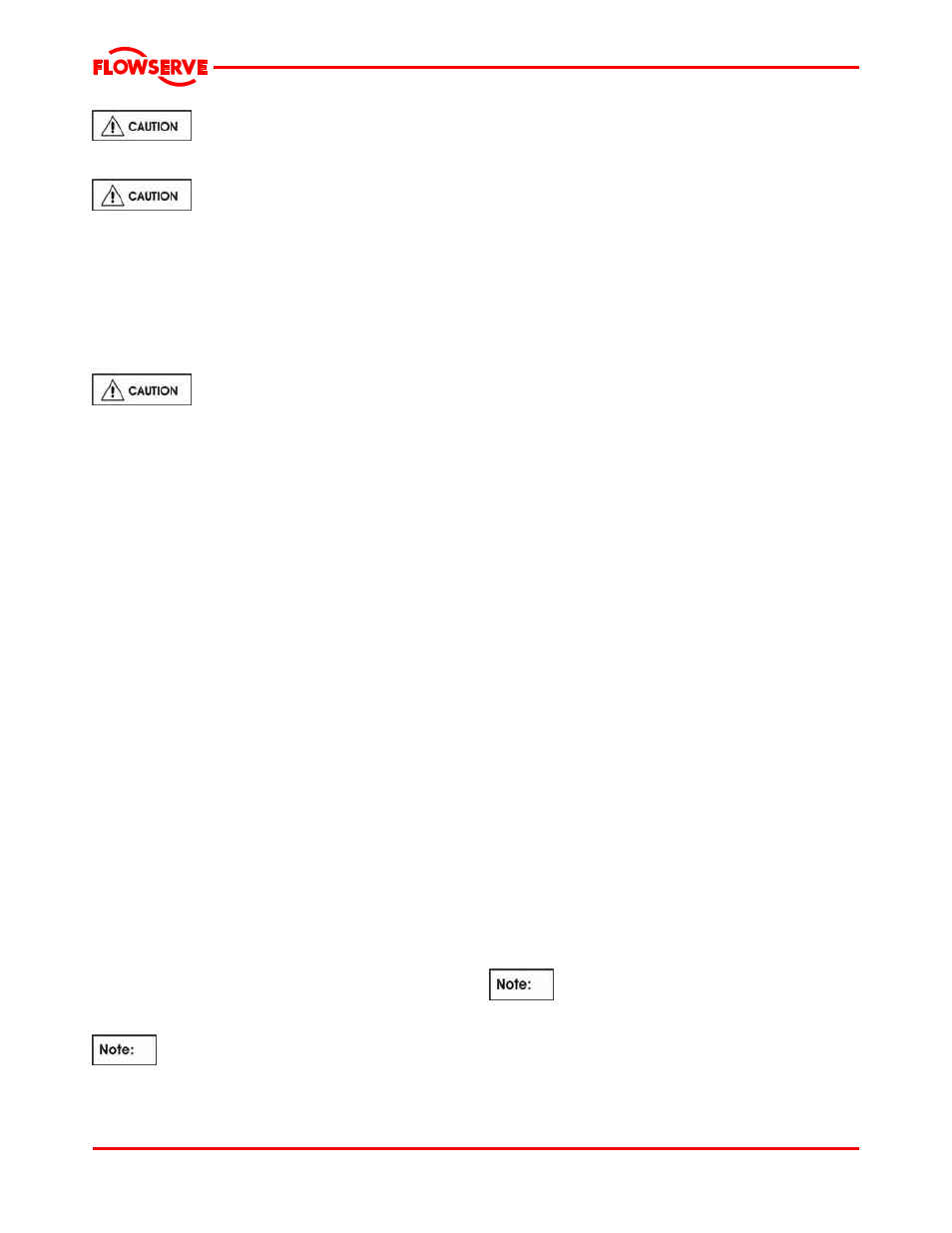
USER INSTRUCTIONS MARK 3 High Silicon Iron ENGLISH 71569249 09-04
The impeller could have sharp edges,
which could cause an injury. It is very important to
wear heavy gloves.
Care should be taken in the handling
of high chrome iron impellers.
Tighten the impeller with the impeller wrench from the
Flowserve Mark 3 tool kit. To do this, grasp the
impeller in both hands and, with the impeller wrench
handle to the left (viewed from the impeller end of the
shaft - figure 6-3), spin the impeller forcefully in a
clockwise direction to impact the impeller wrench
handle on the work surface to the right (figure 6-4).
Do not attempt to tighten the impeller
on the shaft by hitting the impeller with a hammer or
any other object or by inserting a pry bar between the
impeller vanes. Serious damage to the impeller may
result from such actions.
Like all front vane open style impellers, the Flowserve
open impeller clearance must be set off the front.
The suction cover must be installed to accurately set
the impeller clearance.
Attach the suction cover plate to the casing. Now set
the impeller clearance by loosening the set screws
[6570.3] and rotating the bearing carrier [3240] to obtain
the proper clearance. Turn the bearing carrier
clockwise until the impeller comes into light rubbing
contact with the suction cover. Rotating the shaft at the
same time will accurately determine this zero setting.
Now, rotate the bearing carrier counter-clockwise to get
the proper clearance. Refer to figure 5-10 for the proper
impeller clearance.
Rotating the bearing carrier the width of one of the
indicator patterns cast into the bearing carrier moves the
impeller axially 0.1 mm (0.004 in.). (See figure 6-5.)
Determine how far to rotate the bearing carrier by
dividing the desired impeller clearance by 0.1 mm
(0.004 in.) (one indicator pattern). Tightening the set
screws [6570.3] will cause the impeller to move 0.05
mm (0.002 in.) away from the suction cover because of
the internal looseness in the bearing carrier threads.
This must be considered when setting the impeller
clearance. Rotate the bearing carrier counter-clockwise
the required amount to get the desired clearance to the
casing.
Lastly, uniformly tighten the set screws
[6570.3] in incremental steps up to the final torque
value to lock the bearing carrier in place.
See section 5.3 for impeller clearance settings.
Example: If a pump was to be placed in a service
with an operating temperature of 150 °C (302 °F) the
impeller setting would be 0.69 mm (0.027 in.) off the
suction cover. Since it is necessary to subtract 0.05
mm (0.002 in.) for the movement caused by
tightening the set screws an adjustment of 0.64 mm
(0.025 in.) is needed. First, turn the bearing carrier
clockwise until the impeller comes into light rubbing
contact with the suction cover. To determine the
number of indicator patterns that you will need to
rotate the carrier, divide 0.10 into the desired setting;
0.64 / 0.10 = 6.4 (.025 / 0.004 = 6.3). Rotate the
bearing carrier counter-clockwise 6.5 indicator
patterns which will give a clearance of 0.65 mm
(0.026 in.). Flowserve suggests that a felt tip pen be
used to mark an initial reference point on the bearing
housing and the bearing carrier as shown in figure 6-6.
Then make a second mark on the bearing carrier
indicator patterns clockwise from the initial reference
point. Rotate the bearing carrier counter-clockwise until
the second mark on the bearing carrier lines up with the
initial reference point mark on the bearing housing.
Lastly, uniformly tighten the set screws [6570.3] in
incremental steps up to the final torque value to lock
the bearing carrier in place. The impeller is now set for
an impeller setting of 0.7 mm (0.028 in.) off the
casing.
The above procedure is fairly straightforward when
doing the final setting of the impeller. However it can
be quite laborious when doing the preliminary setting
in order to establish the location of the mechanical
seal. For this reason, the following practice is
recommended. Before the pump is taken out of
service, adjust the impeller until it touches the suction
cover and then rotate the bearing carrier until the
desired impeller clearance is obtained. Identify this
location on the bearing carrier and then rotate the
bearing carrier until the impeller contacts the casing.
Record the distance from the desired impeller
clearance setting to when the impeller contacts the
casing. The pump is now removed and taken to the
shop for maintenance. When it is time to set the seal,
the impeller is simply set off the casing by the same
distance recorded earlier.
The above technique is only applicable if all
of the original pump components are reinstalled. If
the casing, suction cover, impeller or shaft is replaced
this method must not be used.
Page 29 of 48