Flowserve Durco Mark 3 ISO Frame Mounted User Manual
Page 16
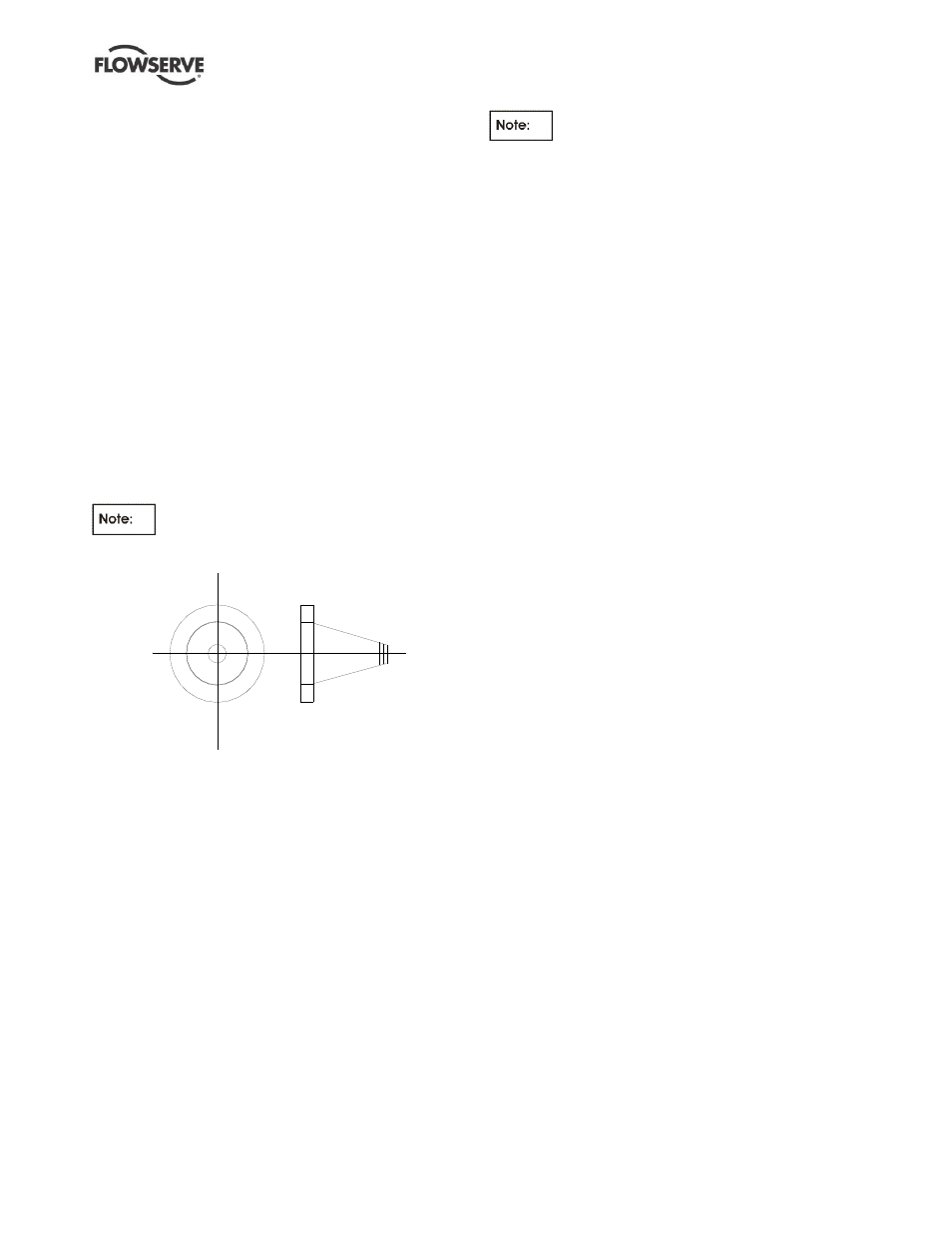
DURCO MARK 3 ISO FRAME MOUNTED ENGLISH 85392719 12-14
Page 16 of 52
flowserve.com
c) Take into account the available NPSH, which must
be higher than the required NPSH of the pump.
d)
Allow a minimum of two pipe diameters of straight
section between the elbow and inlet flange.
e) Fitting an isolation valve will allow easier
maintenance.
f)
Never throttle pump on suction side and never
place a valve directly on the pump inlet nozzle.
Suction strainer
4.6.2.3
In a new installation, great care should be taken to
prevent dirt, scale, welding beads and other items
from entering the pump, as it is particularly important
to protect the numerous close running fits from
abrasive matter present in new piping.
The suction system should be thoroughly flushed
before installing the suction strainer and making up
suction piping to the pump.
The suction strainer should be installed between 5 to 20
pipe diameters upstream from the pump suction flange.
The open area of the strainer should
have a minimum of a 3 to 1 ratio to the area of the
pump suction.
Cone type strainer
The Flowserve recommendation for suction strainers
consists of a conical shaped steel plate. The plate
has 1.6 mm (
1
/
16
in.) perforations and is of sufficient
size and thickness for the required flow. (See figure
above.)
Other type of strainers may be used as long as they
conform to the requirements stated above.
Pressure gauges should be installed on both sides of
the screen so that the pressure drop across the
screen can be measured.
When the unit is being started, the gauges on each
side of the screen should be carefully watched. An
increase in the differential pressure between the two
gauges indicates that the screen is becoming clogged
with dirt and scale. At this point, the pump should be
shut down, and the screen cleaned and or replaced.
A spool piece should be installed in
suction line so that the suction strainer may be
installed and removed with a pressure gauge
between the strainer and pump.
4.6.3
Discharge piping
Non self-primer casing discharge piping
4.6.3.1
a)
A non-return valve should be located in the
discharge pipework to protect the pump from
excessive back pressure and hence reverse
rotation when the unit is stopped.
b)
Fitting an isolation valve will allow easier
maintenance.
Self-priming casing discharge piping
4.6.3.2
a) In order to minimize friction losses and hydraulic
noise in the pipework it is good practice to choose
pipework that is one or two sizes larger than the
pump discharge. Typically main pipework velocities
should not exceed 3 m/s (9 ft/sec) on the discharge.
Pipework expanders should have a maximum angle
of divergence of 9 degrees.
b)
If a non-return valve is located in the discharge
pipework then a vent/bleed pipe should be fitted
from the discharge pipe back to the sump or
source tank.
c)
A regulating valve should be fitted in the discharge
pipework unless pump flow is controlled by the
delivery system design.
4.6.4
Allowable nozzle loads
The pump complies with ISO 5199 shaft deflection
limits for the following flange loads. The values are
presented in the ISO 5199/ISO 13709 (API 610)
format. Please note that the values permitted may be
higher or lower than those in ISO 5199; see those
specified for the actual pump size.
The values permitted (50 mm and above) meet ISO
13709 (API610 11
th
edition) Table 5 values with
grouted metallic baseplates. Individual forces and
moments up to twice ISO 13709 (API610) Table 5
values may be permitted but only when applied in
accordance with the conditions in ISO 13709
(API610) Annex F.
Values are presented in compliance with the ISO
1503 sign convention.
All individual values which are greater than the
following values must be referred to Flowserve for
approval.