Open impeller clearance, Direction of rotation – Flowserve IDP CPXV User Manual
Page 19
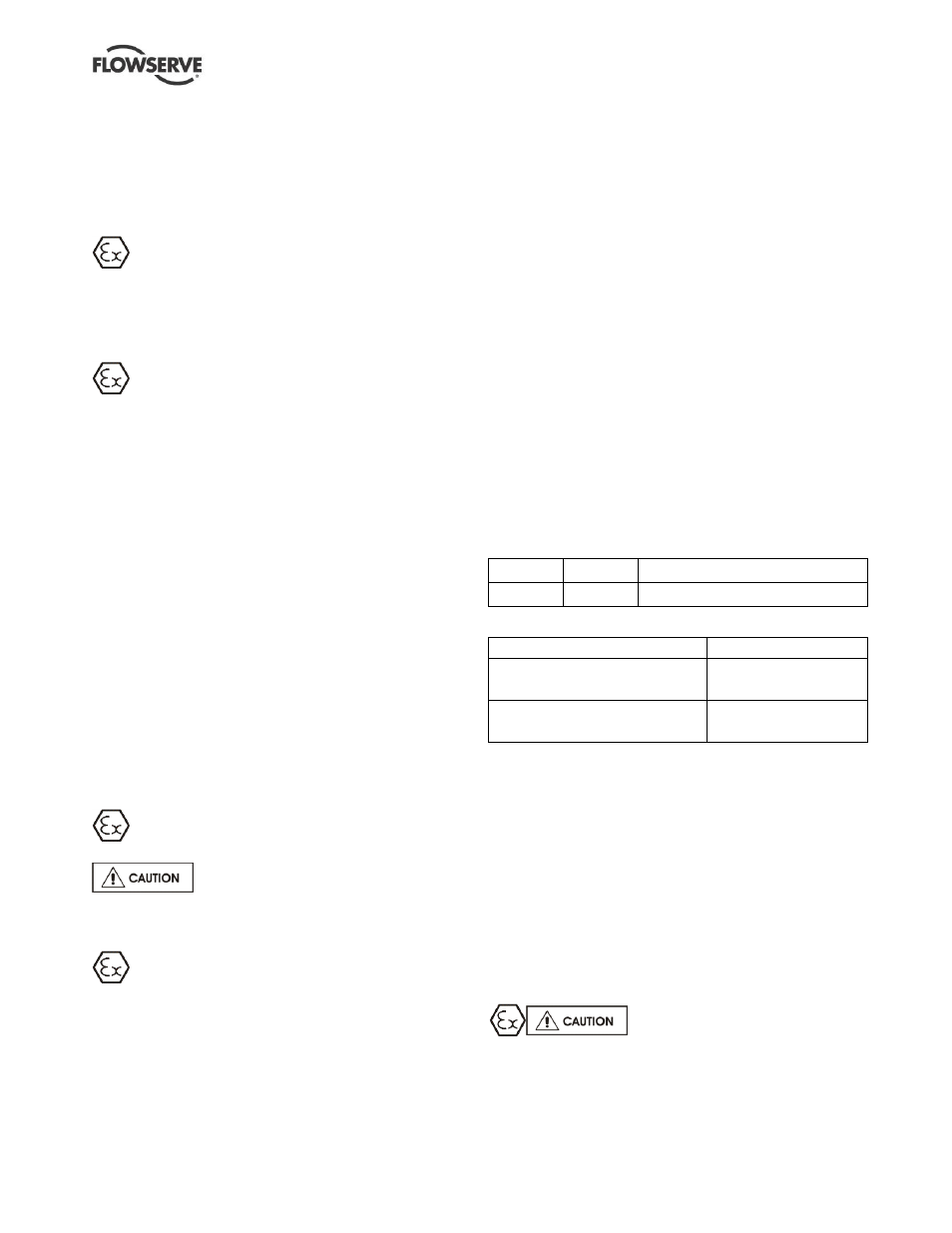
CPXV and CPXRV USER INSTRUCTIONS ENGLISH 71569193 09-14
Page 19 of 48
flowserve.com
used if checks show that the rubber oil seals will not be
adversely affected.
The bearing temperature may be allowed to rise to
50 ºC (90 ºF) above ambient, but should not exceed
82 ºC (180 ºF) (API 610 limit). A continuously rising
temperature, or an abrupt rise, indicates a fault.
T5 and T6 temperature classes have more
restrictive temperature control limits, see 5.8.3.
Pumps that handle high temperature liquids may
require their bearings to be cooled to prevent bearing
temperatures exceeding their limits.
T5 and T6 temperature classes have more
restrictive temperature control limits, see 5.8.3.
5.2.5.2 Grease lubricated Rolling element
bearings
When grease nipples are fitted, one charge between
grease changes is advisable for most operating
conditions; ie 2 000 hours interval. Normal intervals
between grease changes are 4 000 hours or at least
every 6 months
. For food grade grease the grease
change and relubrication intervals are half that of the
conventional greases.
The characteristics of the installation and severity of
service will determine the frequency of lubrication.
Lubricant and bearing temperature analysis can be
useful in optimizing lubricant change intervals.
The bearing temperature may be allowed to rise to
55 ºC (99 ºF) above ambient, but should not exceed
95 ºC (204 ºF). For most operating conditions, a
quality grease having a lithium soap base and NLGI
consistency of No 2 or No 3 is recommended. The
drop point should exceed 175 ºC (350 ºF).
T5 and T6 temperature classes have more
restrictive temperature control limits, see 5.8.3.
Never mix greases containing different
bases, thickeners or additives.
5.2.5.3 Grease lubricated plain line bearings
This option must not be used with ATEX pumps.
Pumps furnished with grease-lubricated shaft
bearings [3300] will leave the factory with lubrication
pipes [3840] shown in Section 8.5.1, and bearings
[3300] already packed with grease. The grease used
will be of a water-resistant nature. Each line bearing
120 ml (4 oz.) minimum automatic lubricator [3800]
should be started prior to the pump start-up through
their fittings located above the pump sole plate
[6140].
Grease must be insoluble in the liquid being pumped
to be effective. The recommended grease procured
with the automatic lubricators must also be
compatible to that being provided in the lubrication
lines. The normal standard default for an automatic
lubricator is Mobil Mobilith SCH100 NLGI 2 grade
grease or an equivalent in which case the bearing
lubrication lines are filled with that grease type before
the pump leaves the factory. Check the automatic
lubricators manufacturer’s instructions provided with
the order. Consult local lubricant suppliers for the
type of grease most compatible with the liquid being
pumped.
Grease lubricated line bearings require frequent
lubrication. Grease lubricating systems may be
utilized. Follow the automatic lubricators
manufacturer’s instruction for proper use. General
lubrication intervals and amounts are shown in the
tables below.
Service
Clean
Contains abrasives
Interval
8 hours
4-6 hours
* Interval depends upon process conditions
Location
Amount
Bottom Bearing (3300.1)
11 grams (0.375 oz.)
47 cm
³
(2.9
in
.
³)
Intermediate Bearing (3300.2)
18 grams (0.625 oz.)
21 cm
³
(1.3
in
.
³
)
Flowserve offers one system for the CPXV consisting
individual 120 ml (4 oz.) minimum automatic
lubricators per line shaft. Consult your Flowserve
representative for additional information.
5.3 Open impeller clearance
The impeller clearance is set in the factory. This may
require adjustment because of increase in liquid
temperature. If piping attachment cause the impeller
clearance to change, correct piping. For setting
instructions see section 6.7, setting impeller clearance.
5.4 Direction of rotation
Serious damage can result if the
pump is started or run in the wrong direction of rotation.
The pump is shipped with the coupling element
removed. Ensure the direction of rotation of the motor is