Flowserve 955 Chemiepac User Manual
Page 6
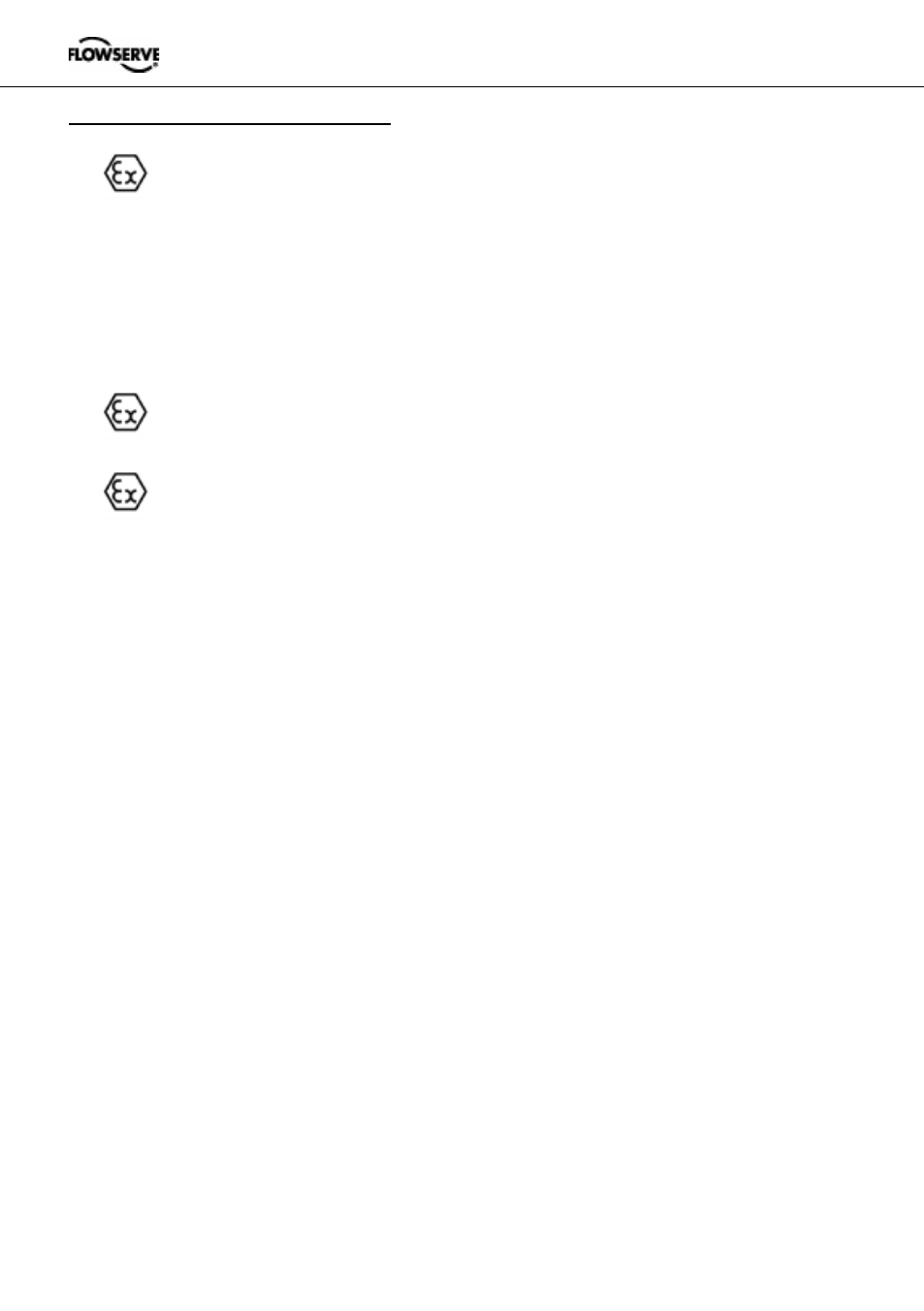
!
!
!
-6-
5.0 PREPARING FOR INSTALLATION
5.1
The MS may be installed when there are no visible signs of damage to the MS.
This applies in particular to the seats, centrings, and the static sealing ele-
ments.
Before installing, consult the specifications on the accompanying documents
to verify that the correct MS has been installed correctly and is suitable for the
specified application. Do not exceed the design data.
Requisite for all assembly work are the installation drawing and parts list and
the tools and aids required for the assembly.
Vibrations must be prevented from transferring to the installed MS during
operation, e.g. through structural measures implemented on the machine.
5.2
The installation chamber for the MS must be checked against the correspon-
ding drawing and table of dimensions. It must be ensured that all dimensions,
surface qualities, and tolerances (e.g. concentricity, run-out, fits) are observed.
The specifications under e.g. ISO 21049 or API 682, DIN 28 161, FLOWSERVE
publication FSD 101, FLOWSERVE publication 127 must be observed.
5.3 Ensure the highest degree of cleanness. Force must not be used to install the CHEMIE-
PAC. Use only suitable tools and aids.
5.4 The seal faces of the MS are important functional sites and may not be damaged.
5.5 All functional and assembly areas for the secondary seals (e.g. O-rings) must be
dimensionally accurate, free of striae and burrs, chamfered, and radiused.
5.6 The locating surfaces of the MS and installation chamber must be undamaged and the
feed pipes and ring channels dry.
5.7 A thin coat of product-compatible grease (e.g. DOW Chemical 111) is to be applied to
the sealing elements (e.g. O-rings). Excess grease is to be avoided.
5.8 Depending on the installation direction, a lubricant, e.g. Molykote M55 or PTFE spray
without solvent, must be applied to the shaft or shaft sleeve.
The areas for the clamp connections must remain free of grease, otherwise the
holding force will become inadequate for correct functioning.
Inserting the installation plates.
Place the spring-loaded unit (1–3, 6–[14]15) on a clean surface. Compress the
bellows by applying light, uniform pressure to the drive. The installation plates
must not be inserted until just before the actual installation otherwise there will
be a very high downtime leakage for the first 45 minutes. The setting dimension
is obtained when the installation plates are inserted.
!