Flowserve 1888 Parallel Slide Gate Valve User Manual
Page 5
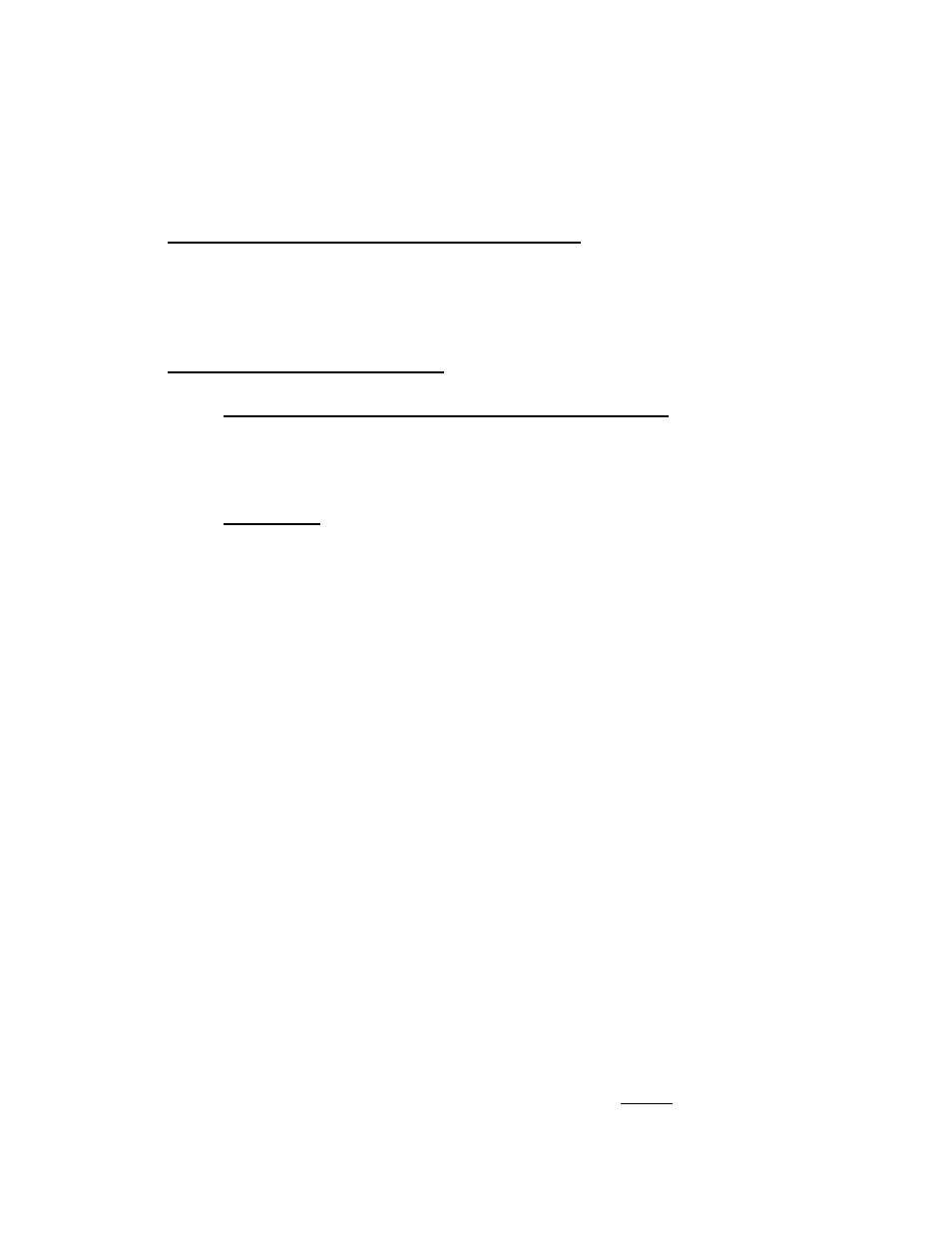
4.1.3 A backseat leakage test at 110% of the 100
°
F pressure rating.
4.1.4 A packing test at 110% of the 100
°
F pressure rating.
5.0
OPERATING PRECAUTIONS AND LIMITATIONS
5.1
Maximum hydrostatic test pressure shall not exceed the values imposed by
the ASME Code, Section III.
6.0
INSTALLATION INSTRUCTIONS
6.1
Lifting and Handling Requirements and Limitations
6.1.1 Good judgement should be exercised in selecting a lifting device that
will safely support the unit's weight.
6.2
Installation
6.2.1 Although the valves have been shipped in a clean condition, prior to
installing the valves, examine the lines and the valve ports for foreign
matter and clean them thoroughly if they have been exposed to the
elements; (BEFORE CLEANING IN THIS FASHION, CHECK AT
THE SITE TO SEE IF A SPECIFIC CLEANING PROCEDURE
SHOULD BE FOLLOWED.) Open the valves fully and flush them
out with water if possible; otherwise blow them out with air or steam.
In performing this cleaning procedure, the ports should be vertical
and the stem horizontal to assure complete removal of all matter that
might have accumulated during storage.
6.2.2 Ensure that there is no line sag at the point of installation. Eliminate
any pipeline deviation by the proper use of pipeline hangers or
similar devices.
6.2.3 Where possible, install the valves with the stem vertical. When other
orientations are used, take care when disassembling the valve so
that the internals do not become damaged.
6.2.4 Remove the end protectors and clean the socket weld ends with a
solvent such as Acetone in preparation for welding the valve into the
line. The valves should then be blocked or slung into position with
an apparatus that is sufficient to hold the valve assembly weight
while the valve is being welded into the line. WELDING SHALL
TAKE PLACE WITH THE DISCS IN THE OPEN POSITION.