Flowserve 132000 Series User Manual
Page 11
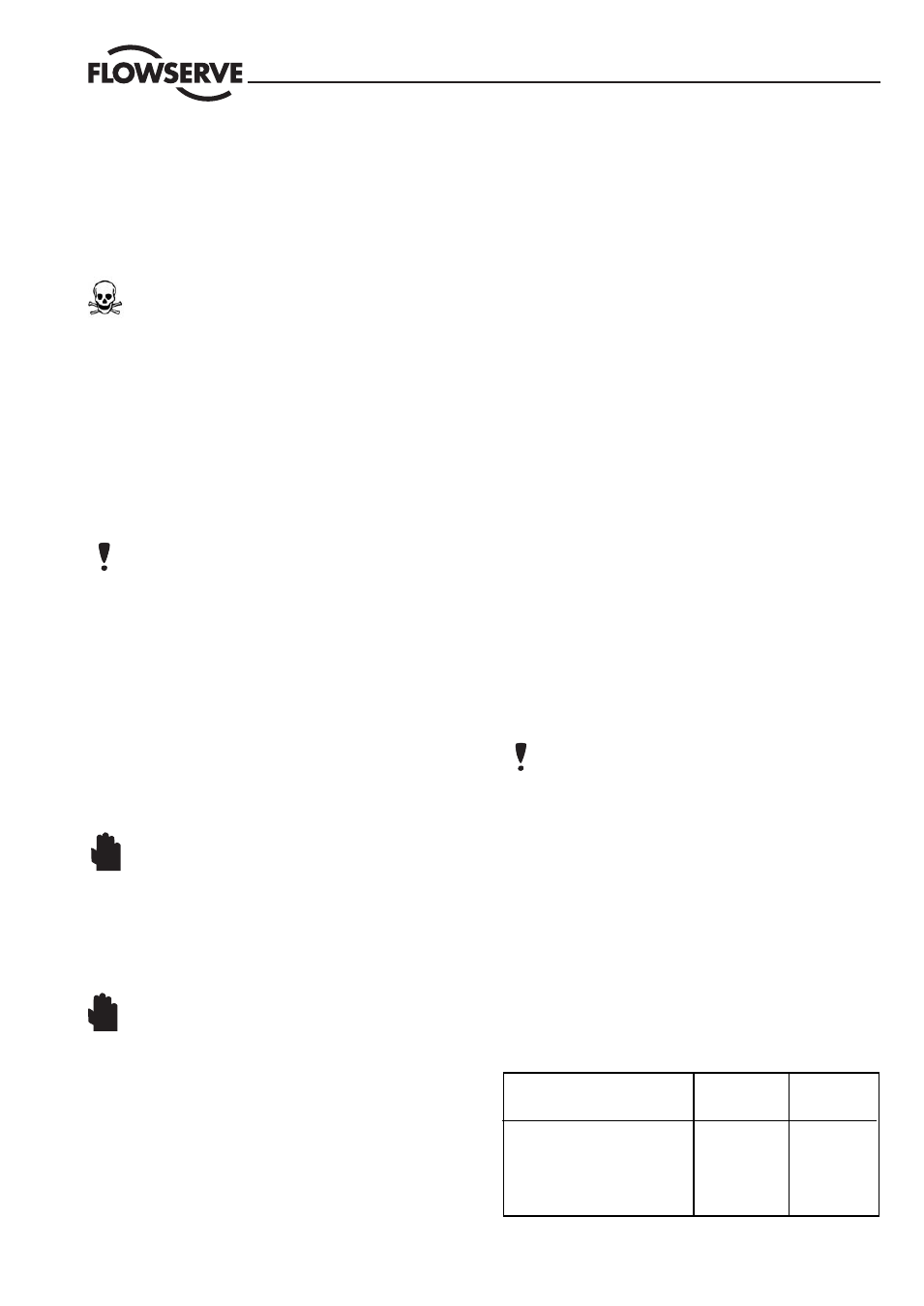
11
Flow Control Division
Kammer Control Valves
DISASSEMBLE AND ASSEMBLE VALVE
20
DISASSEMBLE VALVE
(see Fig. 2)
DANGER:
Since toxic or hazardous substances could be
present, release all pressure in the system and drain all
process substances. If necessary, decontaminate
valve. Keep hands, hair and clothing away from moving
parts. Wear face and eye protection. Failure to observe
can lead to severe injuries.
20.1
Carefully loosen test connection and check whether
medium has collected in bellows cap (bellows
defective).
20.2
Remove bolts/nuts from bonnet and remove bonnet.
Note:
Due to packing friction the bellows/plug is usually
pulled out when the bonnet is removed. In such cases,
hold the bellows/plug so that it cannot fall and be
damaged.
20.3
If the bellows remains in the housing, it can be pried out
carefully with two screwdrivers.
20.4
Without stretching the bellows, remove the plug/
bellows assembly from the bonnet. Press guides,
packing and spacer out of packing chamber from below
with a punch (the punch diameter should be slightly
larger than the plug stem).
20.5
If required, pull out thread lock insert with a pair of
pliers and unscrew plug from bellows.
WARNING:
..When the plug is loosened, medium
residues can be released which have leaked through the
thread.
20.7
Unscrew seat ring with seat ring wrench.
20.8
Check sealing edges on seat ring and plug for damage.
The sealing surfaces must be clean and free of damage.
WARNING:
..To avoid damage to the seat, plug or plug
stem, observe the preceding instructions exactly.
21
ASSEMBLE VALVE
(see Fig. 2)
21.1
Replace all worn or damaged parts. Use only genuine
FLOWSERVE parts. Parts to be reused must be clean.
Always replace parts subject to wear such as gaskets,
packings and O-rings.
21.2
Insert seat ring and tighten (see Table 6 for torque).
21.3
Screw plug onto bellows hand-tight and insert a new
thread lock insert. Cut off thread lock insert so that
approx. 3 mm extends from the hole.
21.4
Carefully insert plug stem with bellows into bonnet.
21.5
Position new O-ring on inclined surface on top of
housing.
21.6
Position bonnet slowly and absolutely upright on body,
to avoid damage to seat/plug.
21.7
Insert bonnet mounting bolts and tighten hand-tight in
crisscross pattern.
21.10 Tighten all bolts to specified torques in crisscross
pattern with torque wrench (see Table 7).
21.11 Replace packing by inserting packing rings one at a time
tapping each one down with a suitable bushing.
NOTE:
ensure that the gaps in the packing rings are dis-
tributed evenly around the circumference in the packing
box (gaps not in line).
Different packings and fitting sequencess are shown in
the spare parts list.
21.12 Insert packing follower and tighten packing nut (see
Table 8).
21.13 During the subsequent pressure test, ensure that the
pressure does not exceed the maximum permissible
pressure for the bellows (PN16). After checking the test
connection for leakage – if present – plug with a plug or
appropriate pressure gauge.
Table 8: Tightening totque for packing nut (Nm)
Thread
PTFE
Grafoil
Packing
Packing
M20 x 1,5
1
3
M30 x 1,5
6
15
M38 x 1,5
15
35
M45 x 1,5
17
40
STOP!
STOP!