Flowserve Valtek FlowTop General Service Control Valve User Manual
Page 2
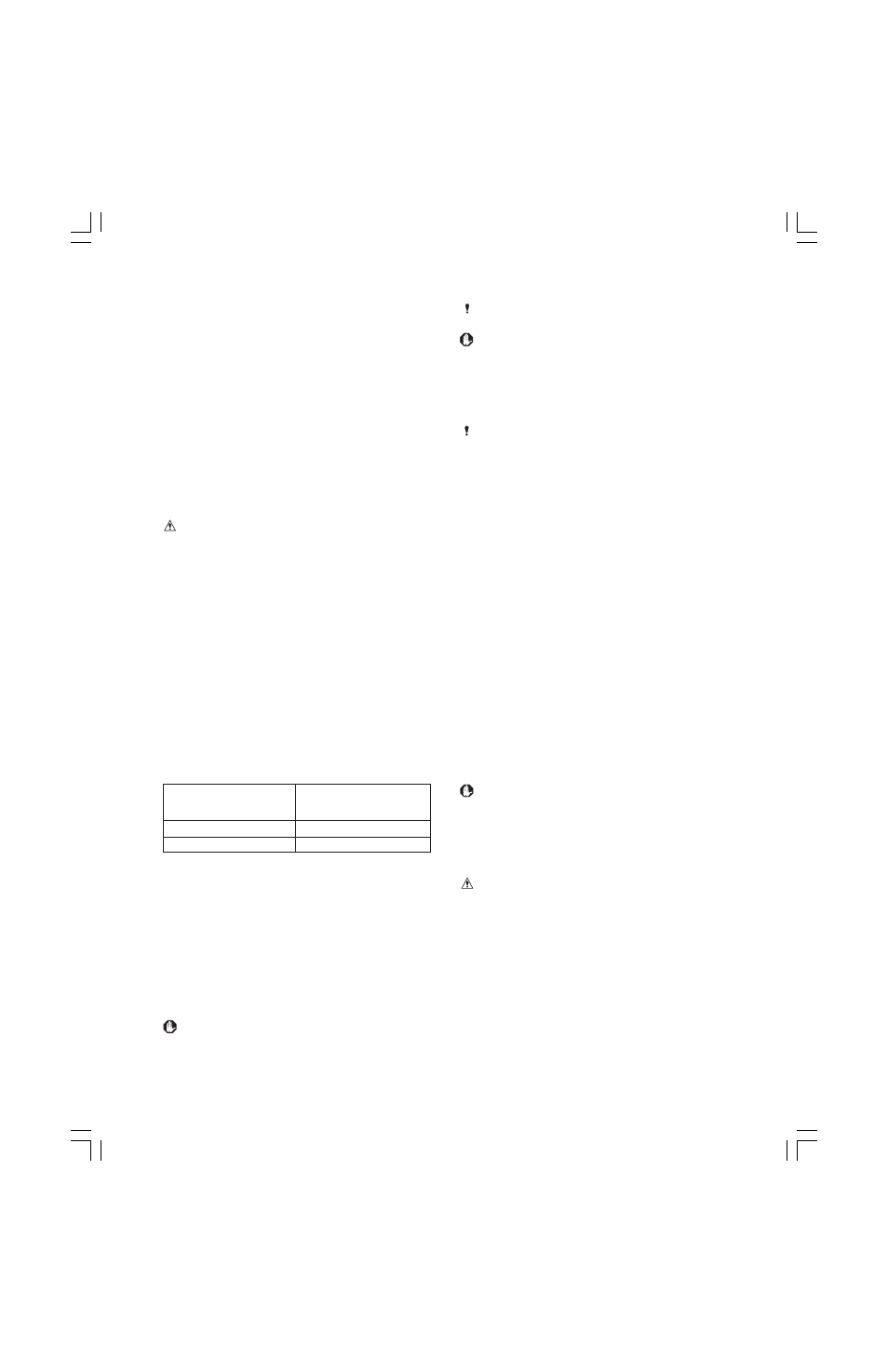
60-2
Flowserve Corporation, Valtek Control Products, Tel. USA 801 489 8611
NOTE: The air supply should conform to ISA 7.0.01.
See specific positioner IOM for details.
WARNING: On valves equipped with air filters,
the air filter bowl must point down – otherwise,
the air filter will not perform properly.
7. Excessive piping stresses, if transmitted to the valve
body, may cause plug friction, seat leakage or other
operating faults.
NOTE: Every effort should be made to minimize
external stresses on the valve during installation.
PREVENTIVE VALVE MAINTENANCE
At least once every six months, check for proper op-
eration by following the preventative maintenance steps
outlined below. These steps can be performed while
the valve is in-line and, in some cases, without inter-
rupting service. If an internal problem is suspected, re-
fer to the
Overhauling section.
1. Look for signs of gasket leakage through the end
flanges and bonnet. Tighten flange and bonnet
bolting (if required). (See Table II.)
2. Ensure the air supply is within the specified range
indicated on the nameplate. Insufficient or
excessive air supply can affect valve operation.
3. Examine the valve for damage caused by corrosive
fumes or process drippings.
4. Clean valve and repaint areas of severe oxidation.
5. Check packing box bolting for proper tightness.
Packing nuts should be slightly over finger-tight;
however, tighten only as necessary to prevent stem
leakage.
WARNING: Do not overtighten packing. This can
cause excessive packing wear and high stem
friction that may impede stem movement.
6. If possible, stroke the valve and check for smooth,
full-stroke operation. Unsteady stem movement
could indicate an internal valve problem.
CAUTION: Keep hands, hair, clothing, etc. away
from all moving parts when operating the valve.
Failure to do so can cause serious injury.
7. Ensure all accessories, brackets and bolting are
fastened securely.
8. If possible, remove air supply and observe actuator
for correct fail-safe action.
9. Check the actuator stem seal assembly (257) for
wear or leakage. Apply an acceptable lubricant
(such as Dow 55) to the actuator stem then retract
and extend the stem to work the lubricant into
the seal.
Unpacking
1. While unpacking the valve, check the packing list
against materials received. Lists describing the
valve and accessories are included in each shipping
container.
2. When lifting the valve from the shipping container,
position lifting straps to avoid damage to external
tubing and mounted accessories.
3. Contact your shipper immediately if shipping
damage has occurred.
4. Should any problem arise, contact your Flowserve
representative.
Installation
CAUTION: Before installation and disassembly,
ensure the actuator is secured with a suitable
method (crane or support) and cannot topple
over.
1. This valve can be installed in alternate service
conditions. Check data on name plate and verify
sizing with local Flowserve office.
2. Before installing the valve, clean the line of dirt,
welding chips, scale or other foreign material.
3. Whenever possible, the valve should be installed
in an upright position; vertical installation permits
easier valve maintenance. (See Figure 1.)
4. Be sure to provide proper overhead clearance for
the actuator to allow for disassembly of the plug
from the valve body. Refer to Table I for the
clearance needed for valve disassembly.
Table I: Overhead Clearance Requirement
Valve Size
Clearance
(inches)
(inches / mm)
1, 1.5, 2, 3, 4
5.6 / 142
3, 4
9.0 / 229
5. Double-check flow direction to ensure the valve
is installed with the flow under the plug. Flow
direction is shown by the arrow on the body.
6. Connect the air supply and instrument signal lines.
Throttling control valves may be equipped with a
valve positioner. In most cases, both the actuator
and positioner are suitable for a maximum of 90 psi
(6 bar) air supply. However, with tandem actuators,
the air supply to the actuator assembly must be
limited to 50 psi (3.5 bar). Check the nameplate to
determine the correct air supply requirements.
WARNING: Tandem actuators require a maxi-
mum of 50 psi (3.5 bar) air supply. Check
nameplate to determine correct air supply
requirements.
IM049 FlowTop IOM.p65
2/10/03, 12:34 PM
2