Worcester controls – Flowserve CPT Series Metal Characterized Seat Control Valves User Manual
Page 4
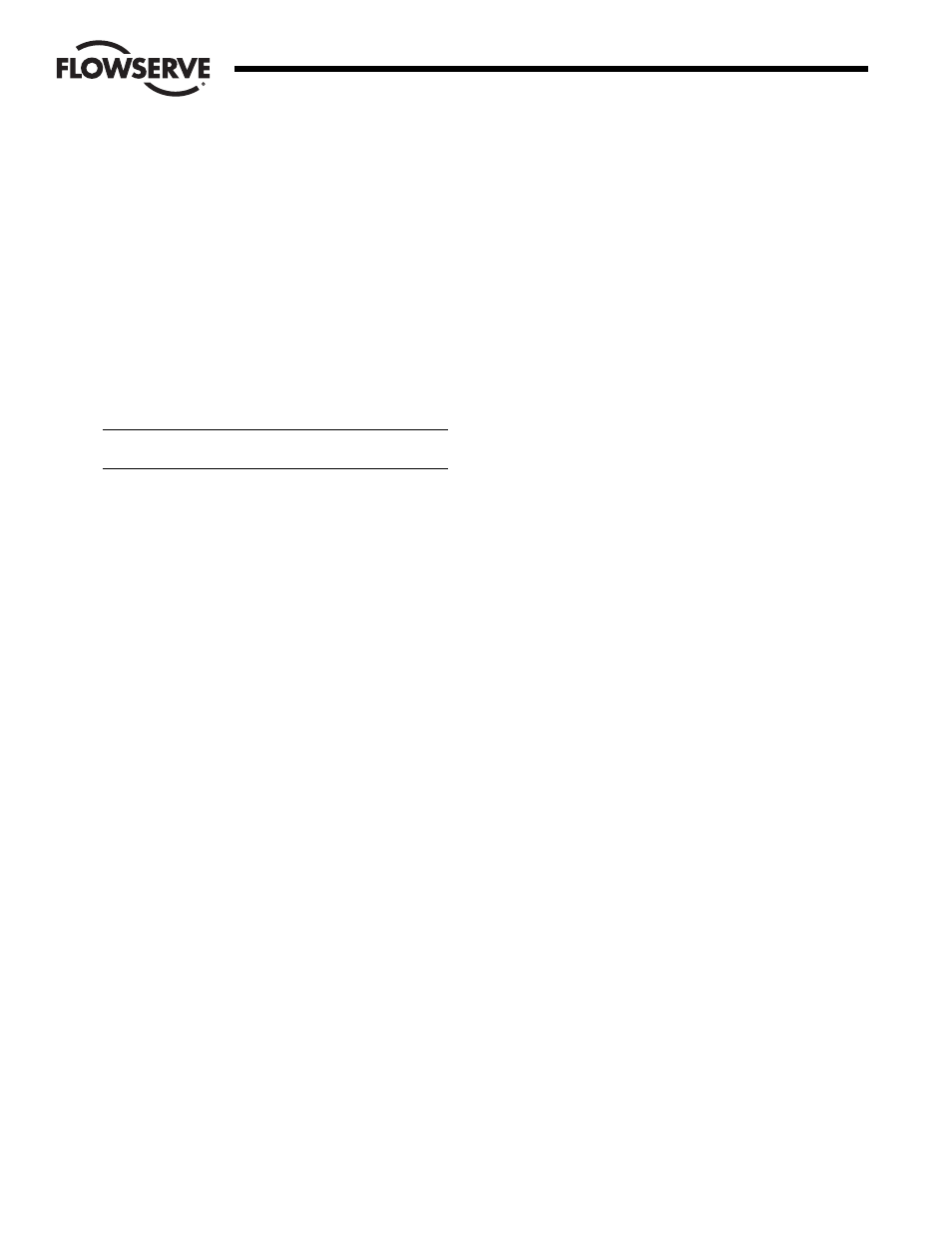
4
Metal Characterized Seated Control Valves Installation, Operation and Maintenance Instructions
09015-G
TO DISASSEMBLE 3"-4" FLANGED ONE-PIECE VALVES:
10. Place valve in closed position. Remove actuator from valve
and remove valve from line.
11. Remove end plug retaining screws. Remove end plug. If
necessary, drive end plug from valve, using wooden drift
applied to face of ball. Be certain the ball is fully closed.
12. Remove body seal, ball, seats, seat back seal(s), and seat
insert (if used).
13. Remove the gland bolts, Belleville washers, gland plate and
follower from the top of the valve.
14. Push the stem down into the body cavity and remove.
15. Remove the thrust bearing and stem packing from the body.
CAUTION: Use care to avoid scratching the surface of the
stem and packing chamber.
C. VISUAL
INSPECTION:
1. The ball and surfaces against which the seats and seals are
installed should be undamaged, clean, and free of pit marks
and scratches. Light marring from the action of the ball
against the seats is normal and will not affect the operation of
the valve.
Flaws that can be seen, but barely detected with fingertips,
are acceptable.
2. The stem and body surfaces that the stem seals and thrust
bearing contact should be clean, undamaged and free of pit
marks and scratches.
D. REASSEMBLY:
Clean all sealing surfaces of the valve including the ball.
For all valves, lightly lubricate the ball, seats, seat back seal(s),
body seal(s), split thrust bearing and split ring or one-piece thrust
bearing, and stem seals with a lubricant compatible with the
media being handled as the parts are used. White petroleum jelly
is a good general purpose lubricant. Filled metal seats will be
lubricated at the factory. If they are not, they should be lubricated
as previously stated. The seat back seals will be pre-assembled to
the seat backs. Do not operate a newly rebuilt valve with filled
metal seats without lubricant.
If graphite parts are used, they should be handled on the flat
surfaces rather than the O.D. These parts can be damaged by
squeezing the O.D. and will not work if they are cracked or
broken. Light flaking of the material is acceptable.
TO REASSEMBLE
1
/
2
"-2" THREE-PIECE VALVES:
1. Insert the stem down through the bonnet and into the body.
2. Place the split thrust bearing in the recessed diameter above
the stem tang. Place the split ring in the same recessed
diameter, under the split thrust bearing (refer to exploded
view).
3. Pull the valve up so that the split thrust bearing and split ring
are drawn into the stem hole recess in the ball cavity. See
instructions 22 through 27 for stem packing and gland plate
assembly.
4. With the valve in the closed position (stem flats going across
pipeline), replace the ball, seats and seat back seal(s) (used
with “A” or “G” filled metal seats only). The characterized seat
has a “V” or “slot” cut in it for improved flow control. It must
be properly oriented to function and the seat can only fit in
the pipe end with an oversized port hole. A locating pin is
provided in the body, and a groove in the seat, to assure that
proper alignment is accomplished. This valve seat can only be
assembled one way and must fit properly, not jam on the pin.
The opposite seat has a standard round port in it.
5. Open the valve and add the body seals. For “S” gaskets, see
cautions I.D.1 - I.D.5. When seat back seals are used, be
certain that they are correctly located on the seat back face
before putting the center section between the pipe ends.
Damage may occur and leaks or high operating torque may
result if the seat back seals are not located correctly.
6. Place center section between pipe ends by separating the pipe
ends from the body by at least
1
/
8
" to allow locating diameter
on the back of the metal characterized seat (for insertion into
oversized pipe end bore) to clear pipe end flange. Replace
actuator, the four body bolts and nuts. Tighten finger tight.
TO REASSEMBLE
1
/
2
"-2" FLANGED ONE-PIECE VALVES:
7. On all sizes except the
1
/
2
", insert the far (characterized) seat
and seat back seal in the body cavity. The seat has a “V” or
“slot” cut in it for improved flow control. It must be properly
oriented to function. A locating pin is provided in the body,
and a groove in the seat, to assure that proper alignment is
accomplished. This valve seat can only be assembled one way
and must fit properly, not jam on the pin. When seat back
seals are used, be certain that they are correctly located on
the seat back face before installing the ball and end plug.
Damage may occur and leaks or high operating torque may
result if the seat back seals are not located correctly.
8. Insert the stem down through the bonnet and into the body.
9. Place the split thrust bearing in the recessed diameter above
the stem tang. Place the split ring in the same recessed
diameter, under the split thrust bearing (refer to exploded
view).
10. Pull the stem up so that the split thrust bearing and split ring
are drawn into the stem hole recess in the ball cavity. See
instructions 22 through 27 for stem packing and gland plate
assembly.
11. Insert the far (characterized) seat and seat back seal into
1
/
2
"
valves per paragraph 7. With the valve in closed position
(stem flats going across pipeline), insert the ball into the body
so that the stem slot engages the tang on the stem.
12. Install the body seal. Be certain that the body seal rests
squarely on the sealing surface in the body. For “S” gaskets,
see Cautions I.D.1 - I.D.5.
Flow Control Division
Worcester Controls