Flowserve 1000 Series Digitial Positioner User Manual
Automax logix series 1000 digital positioner, General information, Logix 1200 positioner overview
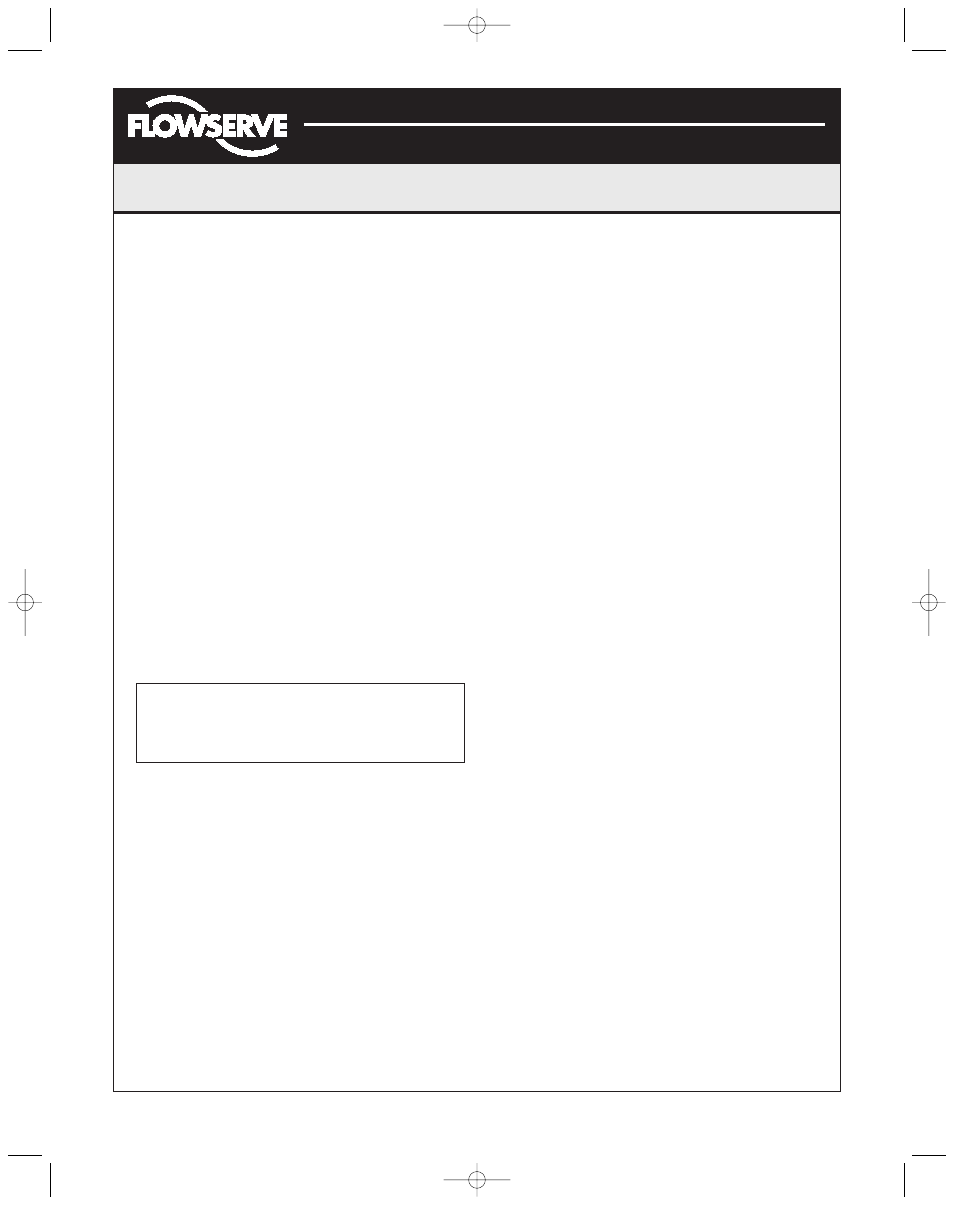
Logix Series 1000 Digital Positioner
Installation, Operation and Maintenance Instructions
Flowserve Corporation
1350 N. Mountain Springs Parkway
1978 Foreman Dr.
Flow Control Division
Springville, Utah 84663-3004
Cookville, TN 38501
www.flowserve.com
Phone: 801 489 2233
Phone: 931 432 4021
© TriCom, Inc., 2004, All Rights Reserved.
Automax Logix Series 1000 Digital Positioner
GENERAL INFORMATION
The following instructions are designed to assist in
unpacking, installing and performing maintenance as
required on Logix™ Series 1000 Digital Positioners.
Series 1000 is the term used for all the positioners
contained herein; however, specific numbers indicate
features specific to a model (i.e., Logix 1200 indicates
that the positioner uses HART
®
protocol). Product users
and maintenance personnel should thoroughly review
this bulletin prior to installing, operating, or performing
any maintenance on the positioner. For quick calibration
instructions, see page 11.
To avoid possible injury to personnel or damage to
valve parts, users must strictly adhere to WARNING
and CAUTION notes. Modifying this product,
substituting non-factory or inferior parts, or using
maintenance procedures other than outlined could
drastically affect performance and be hazardous to
personnel and equipment, and may void existing
warranties.
WARNING: Standard industry safety practices must be
adhered to when working on this or any other process
control product. Specifically, personal protective and
lifting devices must be used as warranted.
Logix 1200 Positioner Overview
The Logix 1200 positioner is a two-wire, 4-20 mA input,
digital valve positioner which utilizes the HART protocol
to allow two-way remote communications with the
positioner. The positioner can control both double and
single-acting actuators and operates with a signal as
low as 3.2 mA. Below 3.2 mA, the operation and
communication are suspended (3.2 mA is required
to restart the positioner).
Since the positioner is insensitive to supply pressure
changes and can handle supply pressures from 35 to
150 psig, a supply regulator is usually not required;
however, an air filter is required due to the close
clearances in the spool assembly.
NOTE: The air supply should conform to ISA Standard S7.3
(a dew point at least 18 degrees Fahrenheit (7° C) below
ambient temperature, particle size below five microns, and
oil content not to exceed one part per million).
Positioner Operation
The Logix 1000 positioner is an electric feedback
instrument. Positioning is based on a balance of two
signals: one proportional to the command input signal
and the other proportional to the valve stem position.
The supply pressure for the positioner pressure
modulator is tapped off the main supply and is filtered
as it passes through a field-replaceable, coalescing filter
element in the module. Next it passes through an internal
pressure regulator that regulates it to approximately
22 psig. The air then passes through an orifice that
restricts the flow and air consumption.
The pressure modulator further controls the air to
6-12 psig, using a spring-diaphragm flapper that is
attracted by an electromagnet to a nozzle. A temperature
compensated hall effect sensor mounted on a circuit
board senses the spool valve position. The hall effect
sensor and circuitry create an inner feedback loop,
which determines how much current to send to the
electromagnet for a desired spool valve position. The
electromagnet in the feedback loop varies the nozzle-
flapper spacing, which regulates the output pressure to
6-12 psig, proportional to the digital position algorithm.
When the command and stem position signals are equal,
the system will be in equilibrium and the valve stem will
be in the position called for by the command signal.
If these opposing signals are not equal, the spool valve
will move up (or down) and, by means of the pressure
modulator, change the output pressures and flow rate.
This causes the actuator pistons to move until the signal
of the position sensor equalizes with the command signal.
FCD AXAIM0064-00 (AUTO-64) 08/04
Page: 1 of 16
© 2004, Flowserve Corporation, Printed in U.S.A.
(AXAIM0096-00) Logix 1000 IOM 8/6/04 3:34 PM Page 1