Calibration and commissioning – Flowserve CEA Series Limitorque Automax User Manual
Page 12
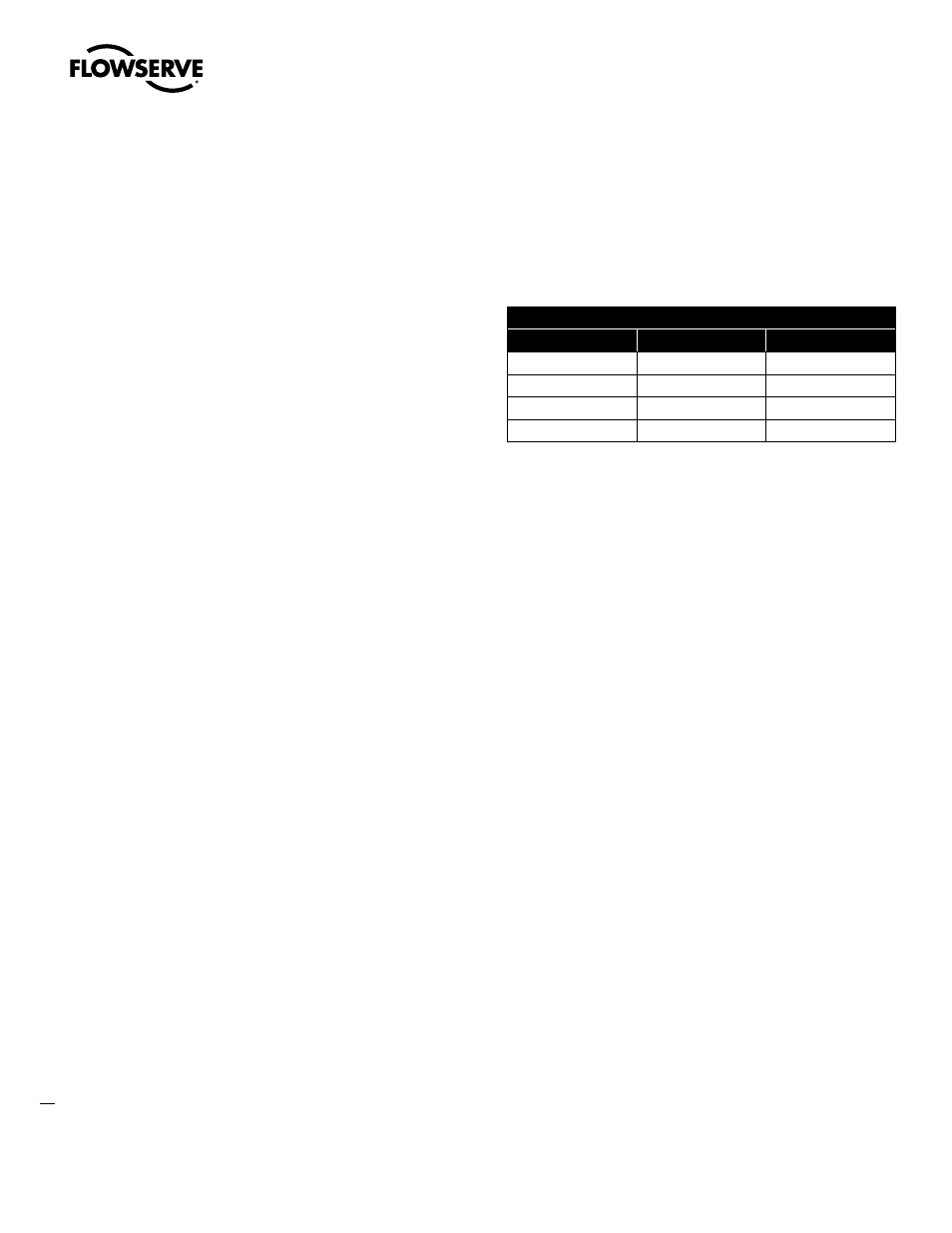
Limitorque Worcester Controls CEA Series FCD WCENIM2080-00-AQ 12/14
12
with two Belleville washers (except 8”, 10” 82/83 and 10” 51/52) and
replace retaining nut.
NOTE: Belleville washers are installed with larger diameters so
they are touching each other. Using a wrench to prevent stem
from turning, tighten retaining nut until the stem packing is fully
compressed or until Bellevilles (if used) are fully flattened. Then,
back off nut 1/6 turn. Excessive tightening causes higher torque
and shorter seal life.
NOTE: 3” size and larger valves with V51 high cycle stem
packing (no handle assembly) are ready to automate without
modification.
For 1/2”–2” 94 valves, remove handle (if any). For 3”–6” 94 and 2”–8”
E818/E828 valves, remove handle assembly, stop, and spacer (if any).
Do NOT remove gland plate or gland bolts.
For 2”–8” 818/828 valves, remove handle assembly, locking plates
and hardware, and stop screw (if any). Do not remove stop plate
(2”–6” sizes) or spacer (8” size).
1. Center coupling on valve stem.
2. Lower mounting bracket/actuator assembly over coupling and
onto valve, making sure that male actuator shaft engages slot in
coupling.
3. Secure bracket to valve using cap screws and lockwashers, or
bolts and nuts provided in mounting kit. Tighten securely. For
small size top mount style valves, bracket nameplate will be to
side of valve.
4. Install set screws (if any) in the coupling and tighten securely.
3.2 Electrical Installation and Adjustment
NOTE: The CEA actuator has 3 threaded covers on the actuator
housing: Controls cover, Terminal Block cover and Motor cover.
Cover(s) use an O-Ring to provide environmental sealing and
proper installation/assembly is required to prevent moisture
ingress.
ATEX hazardous area installation
Each cover incorporates a locking bracket attached by a screw that
must be loosened prior to cover(s) being removed.
Each cover is designed with 4 raised tabs and mechanical assistance
is required to remove the cover. A common “tool belt” screwdriver, 10
inches or longer, is recommended for mechanical assistance. Place
the tool between 2 adjacent tabs and rotate counter clockwise (CCW)
to remove the cover. Once O-Ring compression is relaxed the cover
will rotate freely by hand.
A. To gain access to terminal block, it is necessary to remove the
terminal block cover
B. Make conduit connection(s) to NPT/Metric fitting taps on actua-
tor housing. Connect power supply to actuator terminal strip as
shown on electrical schematic diagram(s) located inside terminal
block cover and also in this manual.
The actuator should be electrically grounded in accordance with
standard procedures.
See table below for minimum fuse rating when overcurrent protection
is used in motor power circuit.
Minimum Fuse Rating for Overcurrent Protection
Actuator Size
Voltage
Fuse Rating (A)
15/60/150
120 VAC
2A
15/60/150
240 VAC
1A
15/60
24 VDC
3A
150
24VDC
5A
NOTE: The table shows the minimum rating to prevent in-rush
current from blowing the fuse.
4. Calibration and Commissioning
The CEA actuator ships from the factory calibrated for 0-90 degree
rotation.
4.1 Travel Stop Adjustment
a
CAUTION: do not rotate travel stops counter clockwise (CCW)
beyond the inward/second “position orientation” groove as this
will result in oil leakage. If accidentally rotated beyond this posi-
tion and leakage is observed, adjust clockwise (CW) to reposition
to the sealing zone between the two position grooves.
a
CAUTION: it is not recommended to use the travel stops to
control normal rotation. Rotation limits should be electronically
set using the HMI menu Calibrate/Rotation with travel stops set
1-2 degrees outside calibrated rotation
Mechanical travel stops are provided on 90 degree rotation units to
provide over-travel protection. They are adjustable to provide +/- 6
degrees of adjustment. They are factory set 1-2 degrees outside the cal-
ibrated rotation. Adjust CW to reduce travel and CCW to extend travel.
One 360 degree rotation provides 3.2 degree position output change.
Each travel stop bolt has 2 position orientation grooves to identify the
min and max rotation position. Adjustment must be maintained within
these 2 grooves. CCW rotation beyond the inward groove will result in
potential oil leakage.
To calibrate the unit after a travel stop adjustment, simply navigate
using the arrow down key to the CALIBRATE menu and then to AUTO
CALIBRATE and select OK. This will recalibrate the actuator to the new
travel stop endpoints.
Please note that if any adjustments are made to the travel stops due to
mount issues or special valve requirements then the unit will require a
field AUTO CALIBRATION before it is placed IN SERVICE.