Worcester controls – Flowserve 10 ACCESS I 39 Actuator with AS Interface User Manual
Page 9
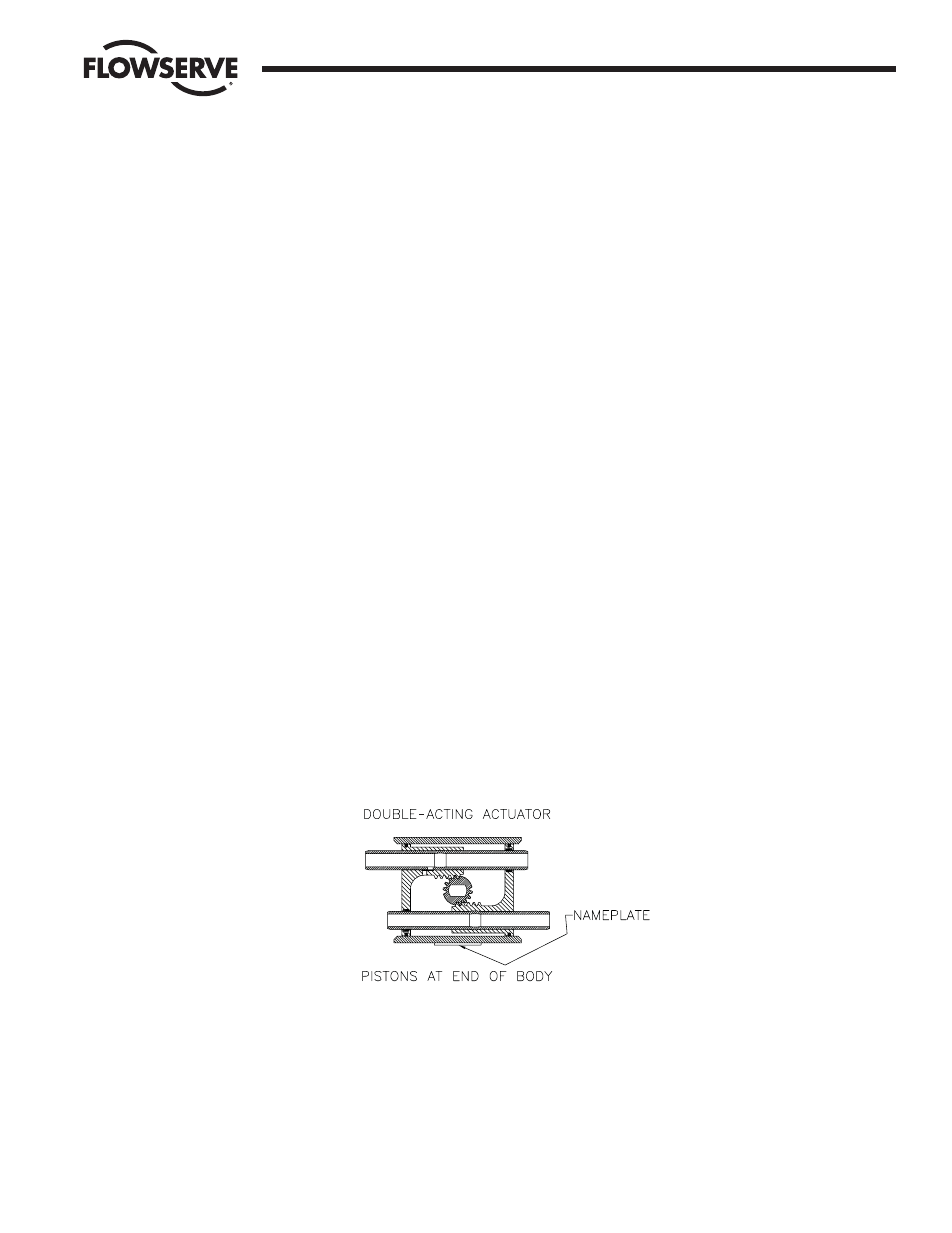
WCAIM2041
10, 15, 20 Access I 39 Acutators with AS Interface
9
IMPORTANT: One piston guide rod assembly has a through hole
drilled in it. It can be easily located by looking down the ends of
both guide rods. This piston assembly must be reassembled, with
its respective guide rod, opposite the nameplate on the body, as it
was removed.
6. Align the shaft so that the teeth on the shaft will “pick-up” the
piston assembly’s rack teeth when turning the top extension of
the shaft clockwise (CW). See Figure 5.
IMPORTANT: Proper 90° rotation can only be ensured if the shaft
teeth begin to mesh with the piston assembly’s teeth at the
“proper tooth” between these meshing gear pairs. See Figure 5.
7. To ensure proper meshing of teeth, move the shaft 15 to 20
degrees counter-clockwise (CCW) from its normal position when
the piston assemblies are located at the body ends. NOTE: The
“normal position” of the shaft is when the top flats are parallel to
the main axis of the actuator body.
8. With the piston assemblies in the body, gently push each piston
into the body. Turn the top shaft extension clockwise (CW). Do
not allow the pistons to “cock”.
At the proper point of engagement between the shaft and piston
assemblies, both piston assemblies will move toward the center
of the body when turning the top shaft extension of the actuator
clockwise (CW).
9. Once the shaft and pistons are properly engaged, ensure that
smooth movement and full closed operation can occur without
moving the pistons out of the actuator body. This is important!
10. Install O-Ring (15A) into and replace the actuator end caps, (5A
and 5B), noting that the “foolproof” pin between the body and end
cap mates properly. For spring-return actuators, see spring
installation section below before installing end caps.
NOTE: When installing the end cap O-Rings, use a small amount
of a general purpose lubricant, such as petroleum jelly, to hold
them in place for ease of assembly and to avoid having them fall
and get pinched.
11. Replace the S.S. washer over the top shaft extension.
12. VERY IMPORTANT:
Install the NEW shaft clip (15F) into its mating groove on the top
shaft extension. (The removed shaft clip is not to be reused.)
Place the numbered side up on the shaft clip and be certain the
clip is fully seated in its groove. See Note in paragraph 7 of
Actuator Disassembly on page 8 for installation of spiral-ring type
shaft clip (which newer rebuilding kits will contain).
13. If control block (7A) was removed:
Properly insert appropriate gasket (9A or 9B) between control
block or air connection block and end cap (see actuator exploded
view), and attach block securely to end cap. Do not apply any
grease to gasket, it must be installed dry.
14. Replace position indicator (17) (if any). See Section D.8. in
Installation Section for proper installation and to determine
position indication.
15. Mark Rebuild/Accessory Addition Label, if included in repair kit,
and apply to actuator.
Flow Control
Worcester Controls
IMPORTANT: Note the relative location of the shaft teeth and the
piston assembly’s rack teeth. The above figure is viewed when
looking at the top of the actuator.
Figure 5