Worcester controls – Flowserve 10-40 39 Access M Worcester Controls User Manual
Page 3
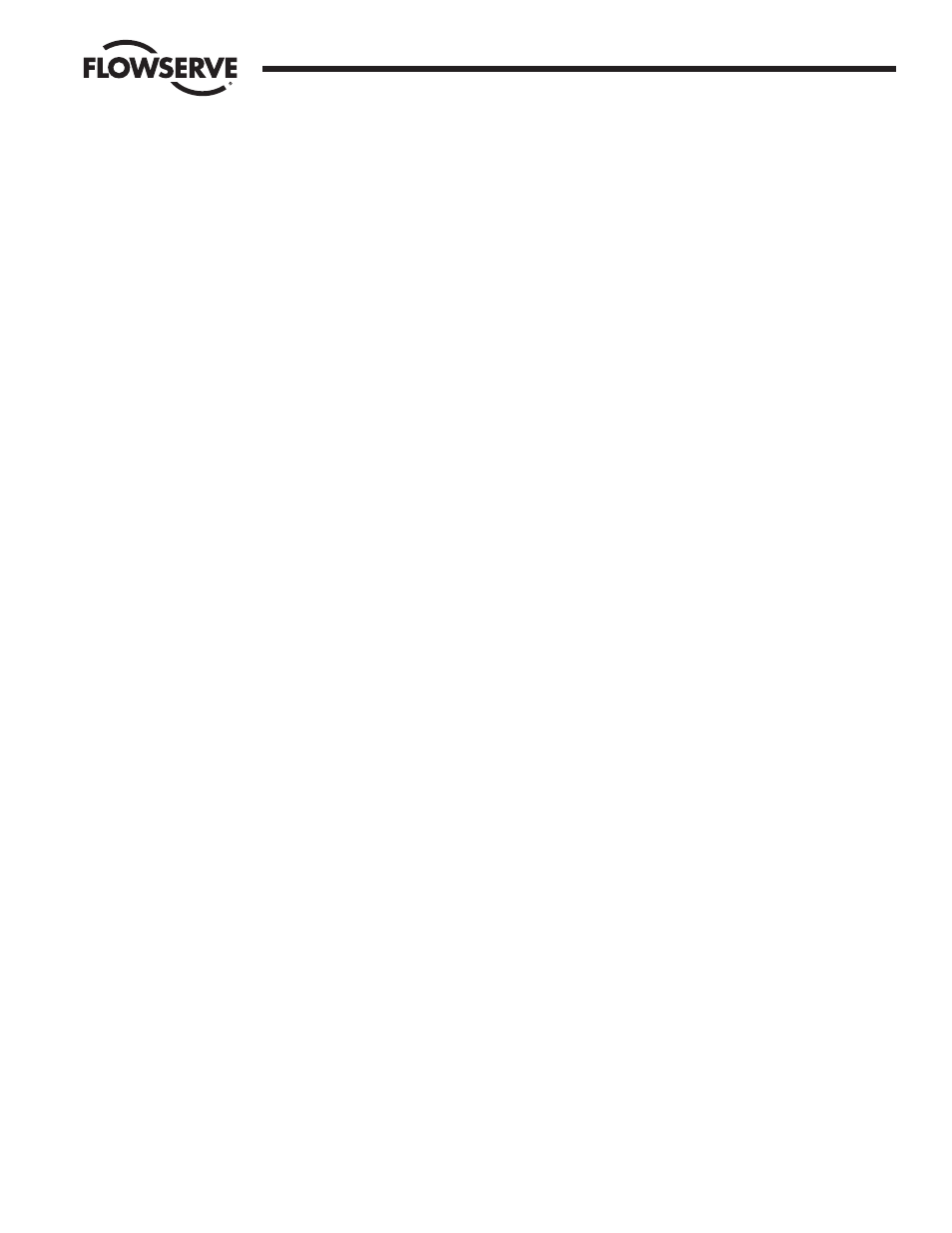
WCAIM2034
10-40 39 Access M Mounted Limit Switch (Proximity Sensor) and Solenoid
3
indicating power to the coil and coil continuity, respectively (if
applicable). Adjust the closed position switch, SW-1 in the
same manner as the open position switch until the red LED
turns on. Then for SPDT switch, tighten adjustment screw
one additional turn. For DPDT switch, tighten adjustment
screw additional
1
/
4
turn only. When the solenoid is de-
energized or the air supply is off, the actuator will return to its
full-open position. The red LED will turn off indicating
solenoid de-energized (if applicable) and actuator no longer in
full-closed position and the green LED will turn on indicating
the actuator is in the full-open position.
NOTE: For DPDT switches, customer must wire directly to the outside
set of terminals of each switch. The wires on the circuit board will be
wired to the switches by the factory using the inside set of terminals
of each switch.
If actuator is mounted in any other than “standard” configuration,
consult Step 1 of Installation Instructions to insure proper orientation
of probes and switches (sensors)
C. Limit Switches Not Using PC Board and/or Not Using LEDs:
With actuator mounted in “standard” fail-closed mounting
configuration (see Step 1) and wired per appropriate wiring
diagram, set actuator in full-closed position, CW limit of
rotation, with adjustment screw near its loose limit. Adjust
closed position switch SW-2 (see wiring diagram) by
tightening the adjustment screw until switch contacts click.
Then for SPDT switch, tighten adjustment screw one
additional turn. For DPDT switch, tighten adjustment screw
1
/
4
turn only. Change actuator to its full-open position, CCW limit
of rotation, and adjust open position switch SW-1 in the same
manner.
For fail-open mounting configuration, wire actuator per
appropriate wiring diagram, set actuator in full-open position,
CW limit of rotation, with adjustment screw near its loose
limit. Adjust open position switch SW-2 (see wiring diagram)
by tightening the adjustment screw until switch contacts click.
Then for SPDT switch, tighten adjustment screw one
additional turn. For DPDT switch, tighten adjustment screw
1
/
4
turn only. Change actuator to its full-closed position, CCW
limit of rotation, and adjust closed position switch SW-1 in
same manner.
NOTE: For DPDT switches, customer must wire directly to the outside
set of terminals of each switch. Inside set of terminals will be wired
by the factory to the terminal strip.
If actuator is mounted in any other than “standard” configuration,
consult Step 1 of Installation Instructions to insure proper orientation
of probes and switches.
D. Proximity Sensors (PC Board not used):
Sensors have to be wired (and powered) per appropriate
wiring diagrams in Section 8. With actuator mounted in
“standard” fail-closed mounting configuration (see Step 1)
and the adjustment screw near its loose limit, set actuator in
full-closed position, CW limit of rotation, and adjust closed
position sensor SW-2 (see Wiring Diagram) by tightening the
adjustment screw until sensor energizes its load. Then tighten
the adjustment screw one additional turn. Supply power to
solenoid (if applicable) and change actuator to full-open
position, CCW limit of rotation. Adjust the open position
sensor SW-1 in the same manner as the closed position
sensor. When solenoid is de-energized (if applicable) the
actuator will return to the full-closed position. The closed
position sensor SW-2, will energize its load indicating the
actuator is in the full-closed position. NOTE: Whenever
actuator is in either the closed or open position, the LED on
SW-2 or SW-1 respectively, will turn on.
For fail-open mounting configuration, wire actuator per
appropriate wiring diagram, set actuator in full-open position,
CW limit of rotation, with adjustment screw at its loose limit.
Adjust open position sensor SW-2, by tightening the
adjustment screw until sensor energizes its load. Then tighten
the adjustment screw one additional turn. Supply power to
solenoid (if applicable) and change actuator to its full-closed
position, CCW limit of rotation. Adjust the closed position
sensor SW-1, in the same manner as the open position
sensor. When solenoid is de-energized (if applicable) the
actuator will return to its full-open position. The open position
sensor, SW-2, will energize its load indicating the actuator is
in the full-open position. NOTE: Whenever actuator is in either
the open or closed position, the LED on SW-2 or SW-1
respectively, will turn on.
7. Customer Wiring to Circuit Board Terminal Strip:
NOTE: Wiring diagrams for units with a PC board as found in this
instruction sheet are for the new PC board. The solenoid (power) and
the limit switch circuits of the new PC board are now separate. The
new board is rated for 10 amps maximum and can be identified by
the board part number label. See table on page 7 for identification of
color-coded part number label.
The old circuit board in the original unit was designed for a single
voltage and current for the solenoid (power) and limit switches,
and was rated for 6 amps maximum. If used on a dual voltage
installation, damage will occur in the control device.
Refer to wiring diagram on inside of cover or appropriate wiring
diagram on the following pages.
Note that for “Standard” fail-closed position, TB4 Terminals #7
and #8 on PC board may be used to connect AC Hot or DC
positive to the customer’s position indication input circuits.
Terminal #8 will be Hot (or positive) relative to terminal #1 when
the actuator is full CCW. Terminal #7 will be Hot (or positive)
relative to terminal #1 when the actuator is full CW. For fail-open
position, Terminal #8 will be Hot (or positive) relative to terminal
#1 when the actuator is full CW. Terminal #7 will be Hot (or
positive) relative to terminal #1 when the actuator is full CCW.
8. Wiring instructions for limit switches and proximity sensors.
Refer to Step 1 for any actuator mounting configuration other
than “standard.”
Flow Control
Worcester Controls