C. installation of dc af-17, Worcester actuation systems – Flowserve DC AF-17 Electronic Positioner User Manual
Page 2
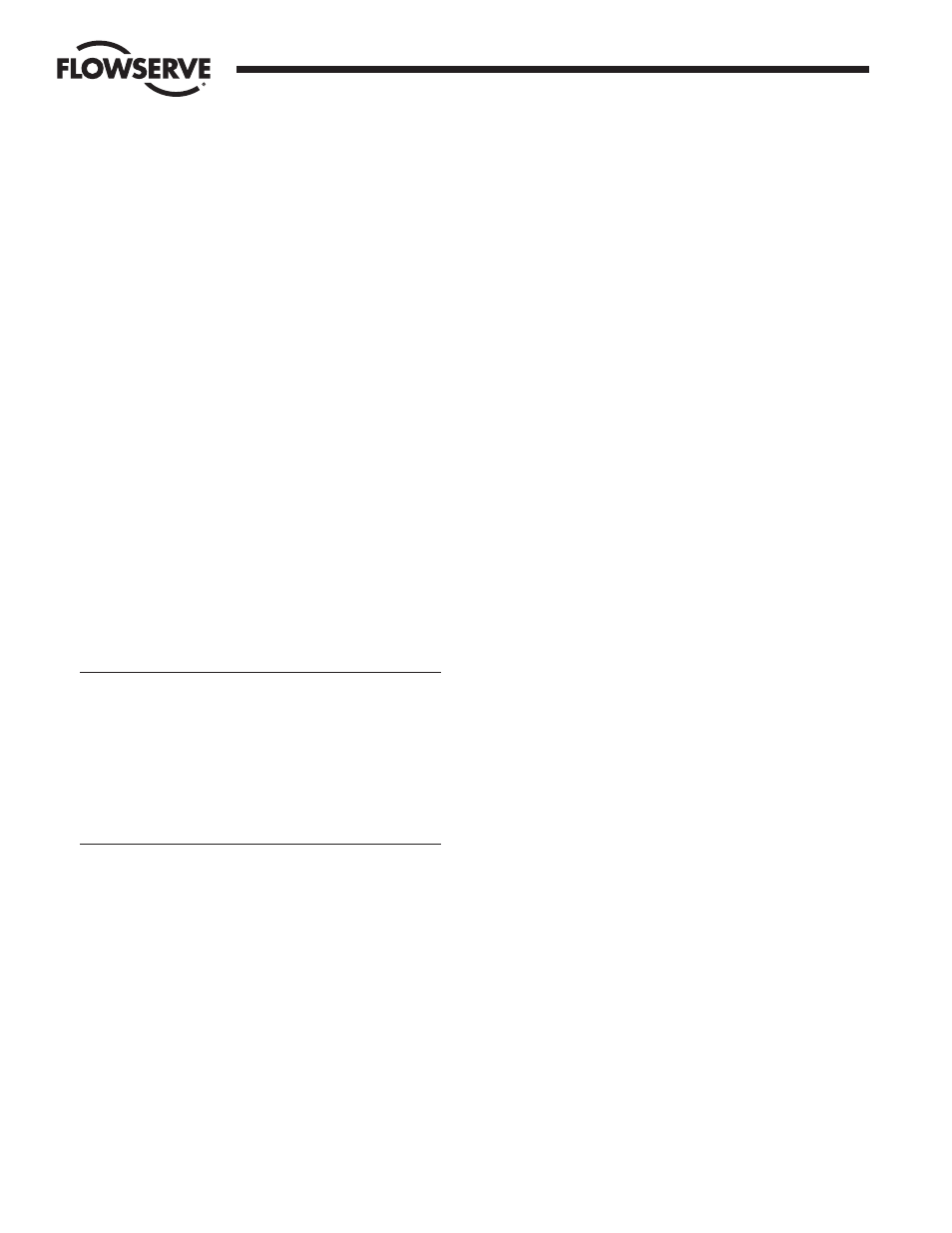
protection fuse. This is most likely to happen when you initially
turn on your current source, i.e., before it starts regulating its
output current. For example, let's say you measure an open
circuit voltage from your current source of 24 volts. Apply the
following formula to determine the value of the resistor to be
added in series with the current loop:
R = [ 24 volts - ( .05
×
220 ohms )] /.05
This calculation may yield a resistor value that is not a common
standard value. Select a resistor of the next higher standard
value (i.e., if your calculation result is a value of 260 ohms, as in
the above example, then pick the next higher standard resistor
value which in this case would be 270 ohms). This will ensure
that enough voltage will get dropped across the added resistor
at 50 mA, to prevent the zener diode from turning on and
causing the fuse to blow. If there are other devices in the current
loop such as a chart recorder or digital readout, then their input
resistances must be added to the input resistance of the AF-17
board (in the above formula, 220 ohms would be replaced by the
total loop resistance). If the calculation results in a zero or a
negative resistance value, then no additional series resistor is
needed. The fuse (F2) used in the input circuit is a Littlefuse
PICO II very fast acting fuse rated at 62 mA. There is a spare
fuse located near the top edge of the circuit board between the
two connectors.
All DC versions of the AF-17 board use a standard 1
¹ ₄" 250 volt,
3 amp fuse (F1) to protect the circuit board and the power
source in case of a fault in the H-bridge circuit on the circuit
board. The H-bridge circuit is the DC polarity and power
switching circuit for the DC motor(s).
CAUTION: It is important that the DC voltage power source be
connected properly to the actuator's terminal strip. Terminal
one (1) of this strip is to have the negative wire connected to
it. Terminal two (2) is to have the positive wire connected to it
(See Figure 3 on page 4.). As stated above, earlier versions of
the board have a diode and a fuse installed to prevent
damage, as in the case of reverse voltage polarity, but if the
diode happens to be defective, damage could be done before
the fuse blows.
NOTE: All wiring to terminal strip should be inserted only to mid-
point of terminal strip.
3. Floating Input Signal
The AF-17 board has been designed to receive a floating current
input signal as standard from the factory. This allows several
pieces of equipment to be operated from the same current loop
while at the same time remaining electrically independent of
each other. A floating input signal means that the current input
signal should not be referenced to the circuit board ground. This
is especially important with DC powered circuit boards. The
board power source must have a ground independent from that
of the signal source.
4. Quadrants of Operation (Refer also to Page 4 of AC AF-17 IOM)
The AF-17 board can be set up in several ways for normal
operation. The board is designed to control in 90° quadrants
only. The number of quadrants over which the board will control
is determined by the number of teeth on the feedback
potentiometer pinion gear. The adjustment trimpots on the board
were not set up to reduce actuator travel for a 4 - 20 mA input
span. For example, trying to adjust the board such that 4 mA is
closed and 20 mA is only 60% open is just not possible with the
standard setup.
The standard setups are:
1) 4 mA for full clockwise rotation – i.e., 0° and 20 mA for full
counterclockwise rotation – i.e., 90° or 180°.
2) Split range where 4 mA would be full clockwise and 12 mA
would be full counterclockwise or 12 mA would be full
clockwise and 20 mA would be full counterclockwise.
3) Each of the above standard setups can also be made reverse
acting.
4. Feedback Potentiometer Calibration
Quite often when we receive an actuator for repair at Flowserve
we find that the only thing wrong with the unit is that the
feedback potentiometer is out of calibration. It is very important
that the feedback potentiometer be properly calibrated for
correct operation of the positioner board. It is also very
important that the actuator shaft not be rotated out of the
quadrant for which the feedback potentiometer has been
calibrated. Whenever you have a problem with positioner
calibration, always check the feedback potentiometer calibration
first. This must be done with no power applied to the circuit
board. If the actuator is in the full clockwise position, check the
resistance between the purple and white/black potentiometer
leads. The reading should be 80-90 ohms. If it is not, rotate the
face gear until the proper reading is achieved. NOTE: It is not
necessary to loosen or remove face gear snap ring to rotate
gear, it is a friction fit. If for any reason the snap ring(s) are to
be removed, do not over stretch them; use minimum opening to
allow them to slip over the gear. If the actuator happens to be in
the full counterclockwise position then check the resistance
between the green and white/black potentiometer leads. If
necessary, adjust the face gear for an 80-90 ohm reading.
C. INSTALLATION OF DC AF-17
1. General
If the actuator was purchased with the DC AF-17 positioner
board factory installed, proceed to section 4.0.
2
DC AF-17 Electronic Positioner
WCAIM2050
Flow Control Division
Worcester Actuation Systems