Electronic circuit board basics, Worcester controls – Flowserve 90 Series Controller User Manual
Page 3
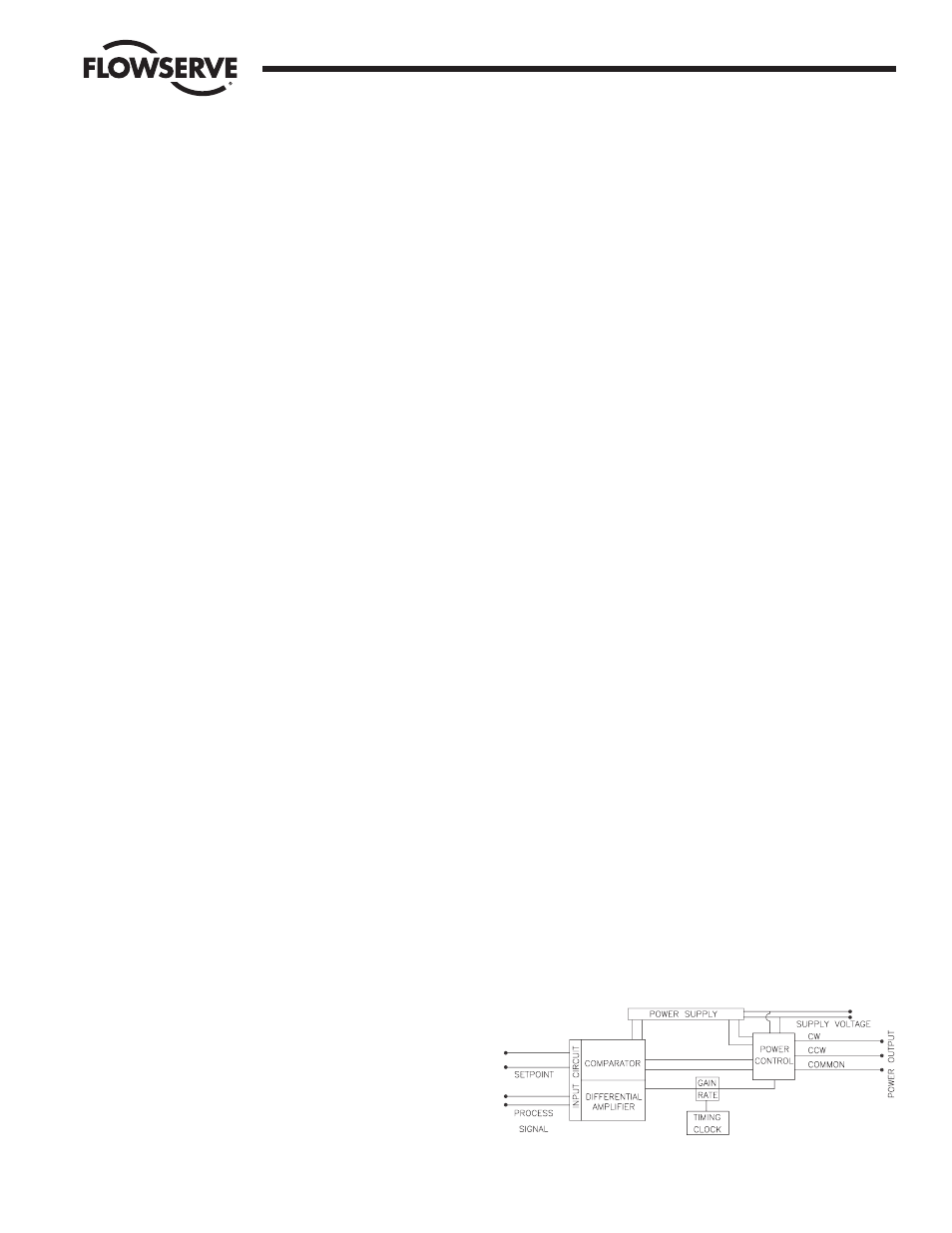
The shields should never be used in place of one of the input
wires, and the shields normally should be grounded to
equipment housings at one end of the wiring run only. Grounding
both ends of shielding can eliminate the shielding benefits
because of ground loops. If two or more shielded cables come to
the positioner from different locations, they must be grounded at
the positioner.
3. ELECTRONIC CIRCUIT
BOARD BASICS
a. Circuit Board Configurations
There are two basic circuit board configurations. Both versions
contain the same basic input, logic and solenoid control
circuitry. The difference is in the type of control function
desired. The positioner version is used to position a
valve/actuator combination proportional to a position input
signal provided by the customer. The controller version is a
single closed-loop controller that compares a process signal to
a user-provided setpoint signal and positions a valve/actuator
combination accordingly.
b. Controls
Each version of the M.A.S. board has a complete set of
adjustment potentiometers to allow tailoring the circuit board’s
response to individual process requirements.
c. Power Control
The M.A.S. circuit board is 100% solid state and utilizes opto-
couplers for input/output circuit isolation. The 120 VAC version of
the M.A.S. board uses sensitive gate triacs to control power to the
solenoid valve(s). The DC M.A.S. board uses transistors to
control the DC power to the solenoid valve(s). The DC M.A.S.
board will work with either 12 or 24 volts DC with no change
required to the board. However, solenoids of the correct voltage
rating must be used.
4. M.A.S. POSITIONER/CONTROLLER
CIRCUIT BOARD DESCRIPTION
OF OPERATION
a. General
The M.A.S. positioner/controller controls on a basis similar to a
computer or microprocessor-driven controller. It first compares
the input signal to the feedback or setpoint signal, and if there is a
relatively small difference, generates a short pulse to move the
valve in the direction necessary to reduce the difference.
At the end of the pulse, the circuit enters a waiting period to see if
the previous valve movement was sufficient to correct the
difference between the feedback or setpoint signal and the input
signal. If the difference has been eliminated by the end of the
waiting period, no additional pulse will be generated. If a
difference still exists, additional pulses will be generated until the
difference has been eliminated.
If there is a large difference between the feedback or setpoint
signal and the input signal, the circuit generates a continuous
signal to move the valve quickly in the direction to reduce the
difference. When the difference becomes small, the controller will
enter the pulsing mode as described above.
Note: The AC M.A.S. positioner/controller input circuit is
protected by a
Z\zn amp fuse, F1, located on the circuit board. This
fuse helps to protect the signal input circuit from excessive
voltage (usually 120 VAC) applied in error. A spare fuse is also
provided on the circuit board. (Also see Section 1, paragraph a).
b. Circuit Description and Block Diagram
The input signal, whether from a process transmitter or a
4-20 mA current source, is fed to the input circuits along with the
feedback/set-point signal. The two signals’ values are compared
by a comparator and action is determined by a differential
amplifier. The comparator circuit evaluates if the valve should
move and in what direction. The differential amplifier circuit
determines the speed of valve movement and the amount of
position change required for the valve to correctly reposition. A
final stage of amplification generates a control signal proportional
to a deviation from the desired position. The amount of this
control voltage signal is adjustable in this final stage of
amplification by the “Gate” adjustment trimpot.
The voltage from the final stage of amplification is also fed into a
timing circuit. This circuit controls the speed with which the
actuator will respond to a given deviation. The timing circuit
senses the control voltage and allows the actuator to turn on for a
time period proportional to the control voltage. As this voltage
decreases, the time on of the actuator (i.e. actuator speed) will
decrease as the process variable returns to the set point. The pulse
duration adjustment “On” and the wait period duration adjustment
“Off” allows a wide adjustment range of speed change. Therefore
the correction signal can be adjusted so the final control element
matches the process variable’s time constant.
0nce the control senses a match between the feedback/set-point
signal and the input signal, the comparator inhibits further actuator
motion, and the power pulse(s) to the solenoid(s) stop(s).
Three Light Emitting Diodes (LEDs) give functional indication:
The top LED indicates when the “Open” solenoid is energized.
The bottom LED indicates when the “Close” solenoid is de-
energized.
The middle LED indicates when there is a match condition.
The LEDs are located in the upper right corner next to the
mounting post when facing component side of board.
WCAIM2045
Positioner/Controller for Series 90 Modular Accessory System
3
Flow Control Division
Worcester Controls
Circuit Block Diagram