Maintenance, Spare parts, Troubleshooting – Flowserve 10 ACCESS I 39 Actuators User Manual
Page 10: Worcester controls
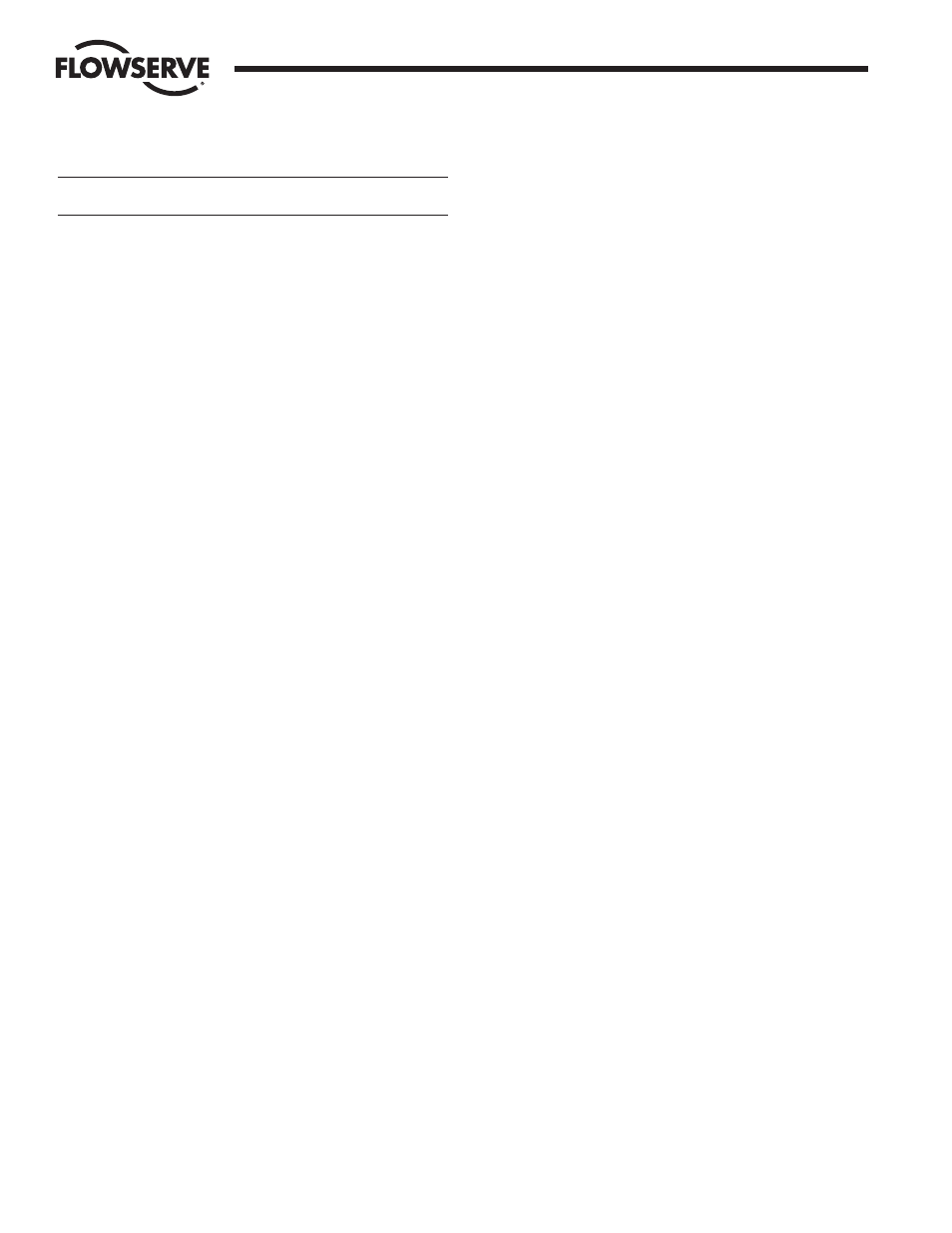
10
10, 15, 20 ACCESS I 39 Actuators
WCAIM2027
MAINTENANCE
CAUTION: The actuator must be isolated both pneumatically and
electrically before any maintenance activity is begun.
Periodic checks should be performed to make certain that all
fasteners remain tight. Care should be taken when tightening the end
cap retaining bolts since these fasteners are METRIC. All other
fasteners are UNIFIED IMPERIAL.
All actuators are supplied with sufficient lubrication for their normal
working life. If required, recommended lubrication for all standard
actuators is a #1 grease.
Depending upon the conditions under which the actuator must work,
such as extended duty, non-compatible operating media or abnormal
operating conditions, periodic replacement of internal seals is
recommended. Repair kits containing all necessary seals can be
obtained through any authorized Worcester/McCANNA distributor.
On spring-return actuators, the springs may need replacement after
extended duty since springs may fatigue and break. SPRINGS
SHOULD ALWAYS BE REPLACED IN COMPLETE SETS. Spring kits are
available through any authorized Worcester/McCANNA distributor.
SPARE PARTS
The following are recommended spare parts that should be kept on
hand for Series 39 pneumatic actuators:
Repair Kit(s) – Kits contain all necessary seals, bearings and
instructions.
Spring Kit(s) – For spring-return actuators.
TROUBLESHOOTING
Before disassembling actuator for any reason, consult rebuilding
instructions contained in following section.
A. If actuator does not function, check to ascertain:
1. That valve is free to rotate. This can be done as described
above in Manual Operation.
2. That actuator is the correct size.
3. That speed control screws or exhaust ports are not blocked.
4. That correct voltage is supplied to solenoid.
5. That sufficient air supply is available at inlet to control block.
Inlet pressure to control block should be at least 40 psig for
double-acting, 80 psig for spring-return (unless a reduced
spring complement is installed (fewer springs)). When
checking supply pressure, place gage in line at control block
inlet and monitor gage for unexpected pressure drops.
6. If the ACCESS unit is equipped with a 120 VAC circuit board,
check for a blown fuse (F1). Using an ohmmeter, the fuse
should read about 6 ohms if it is good. Remove the fuse from
the circuit board in order to check it. If it is good, reinstall the
fuse. If the fuse is bad, replace it with a Littlefuse PICO II very
fast-acting fuse rated at 62 mA (Newark part number 94F2146)
or the spare fuse, which may be found on some circuit boards
and located below capacitor C1. Try to determine what caused
the fuse to blow before turning power back on. The most likely
cause is a bad solenoid coil.
B. If proper voltage and air pressure have been verified and valve is
free, proceed as follows:
1. Turn on signal voltage. Check solenoid for clicking sound.
2. If no sound is detected, remove air pressure and turn off
signal voltage.
a. Carefully unscrew solenoid and solenoid stem from
end cap.
b. Reapply signal voltage and observe solenoid plunger. If it
does not retract, replace solenoid.
3. Manually override control block. If correct operation is not
obtained, replace the control block.
4. If control block and solenoid are operating correctly, proceed
to Section C.
C. If the actuator functions but exhibits leakage, or power loss
accompanied by leakage, proceed as follows:
1. Check voltage. Voltage must be within 10% of the specified
voltage. Low voltage will cause leakage out of the back of the
solenoid and burn out of the coil.
2. Check air supply. Be certain that no sharp air pressure drops
occur as unit is cycled. Loss of air pressure can cause
incomplete shifting of the spool valves, which results in
bypass leakage and substantial actuator torque losses.
3. If air supply and voltage are adequate, proceed as follows:
a. If leak is at solenoid exhaust port, replace the solenoid.
b. If leak occurs at exhaust ports in the block itself, the
trouble will be in either the spool valve in the block, or at
one of the piston seals of the actuator. A leaking piston
seal will usually leak on either cycle.
If the block is replaced and leakage continues from the
exhaust port, remove the actuator from the valve,
disassemble (per Rebuilding Instructions) and check the
following:
1. Make sure that all internal porting is free and clear of
any obstructions. End caps, guide rods and the piston
with hole are air-transporting components.
NOTE: The most common problem encountered on 39
actuators is the improper replacement of the piston
with hole relative to seals in end caps. See Step 5 on
page 11.
2. Make certain that the actuator has lubrication, and
that there is no solidified grease between the pinion
and the piston racks.
Flow Control Division
Worcester Controls