Flowserve Hydraulic Heavy Duty Actuators User Manual
Page 2
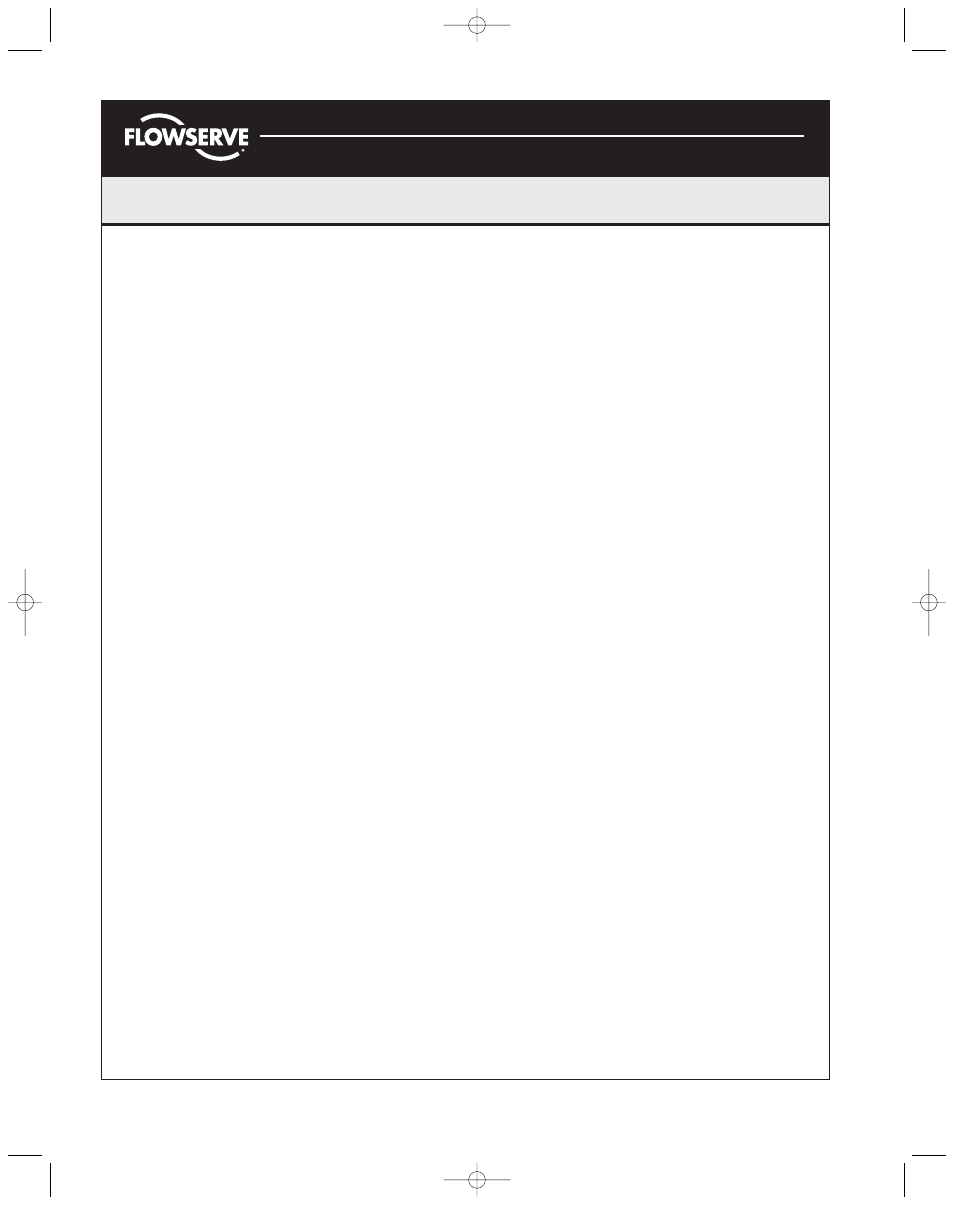
© 2004, Flowserve Corporation, Printed in USA
Automax Valve Automation Systems
Installation, Operation and Maintenance Instructions
Flowserve Corporation
1350 N. Mountain Springs Parkway
1978 Foreman Dr.
Flow Control Division
Springville, Utah 84663-3004
Cookeville, TN 38501
www.flowserve.com
Phone: 801 489 2233
Phone: 931 432 4021
Disassembly Procedures
1.
Disconnect all hydraulic and electrical supplies
from actuator.
2.
Remove all accessories from actuator and
dismount from valve.
Spring Group
Note:
Personal Injury may result if Step 2 is
attempted before Step 1 is completed.
1.
Apply hydraulic pressure to the cylinder to
release spring pressure from Stop Bolt (16).
Remove both Stop Bolts (16) and remove hydraulic
pressure. This will relieve majority of spring load.
2.
The Spring Cartridge (11) is welded as an
integral component and cannot be disassembled.
To remove from actuator remove Spring Cartridge
Nuts (41) and Lockwashers (42). At this point all
spring forces are contained within welded cartridge
and spring may be removed from body.
Note:Support Spring Cartridge (11) during removal
so as not to damage Piston Rod (3).
Pressure Group
Note: Rod pusher pressure group will not have a
piston. Step 3 is not applicable.
1.
Remove Tie Rod Nuts (28), Tie Rods (27), and
Endcap (29).
2.
Slide Cylinder (23) over and off Piston (24),
being careful not to scratch or dent honed and
chrome plated surface of cylinder (23).
3.
Remove Piston Bolt (25), Piston Bolt
Lockwasher (26), Piston (24), and Piston Face
Seal (32).
4.
Remove Adapter Bolts (43) and carefully slide
the Adapter (22) over the Piston Rod (3).
Note: A double acting actuator will have a rod
pusher pressure group on the opposite side of
the main pressure group (in place of spring
cartridge). Follow disassembly procedure as
above, skipping step 3.
Housing (Body Group)
1.
Unscrew Inspection Cover Screw (9) with Lock-
washers (10) and remove Cover (8) and Cover
Gasket (35).
Note: Prior to disassembly of remainder of Body
Group visually check inspection opening to
determine whether further disassembly is
necessary. If Yoke (4), Yoke Pin (5), and Yoke
Rollers (6) are in good condition, do not
disassemble further.
2.
To remove Piston Rod (3) and Piston Rod Bearing (2),
center Yoke in mid- or 45 degree position.
R2 actuators: To remove the Yoke Pin Retainers (7),
use snap ring pliers with 90
°
tips. Access snap
rings through inspection cover opening. Turn
Piston Rod (3) to remove Yoke Pin Rollers (6) and
Yoke Pin (5) through inspection cover opening.
MAINTENANCE INSTRUCTIONS
R3 and R4 actuators: Remove both freeze plugs
located in Housing near Bearing Retainer (13).
Through these openings, both Yoke Pin Retainer
Rings (7) can be removed. Yoke Pin Rollers (6)
can be slipped off Yoke Pin (5). Push Yoke Pin (5)
through Piston Rod (3) and out opening in other
side of Housing (1).
3.
Unscrew Bearing Retainer Bolts (14) and remove
Bearing Retainer (13), Retainer Gasket (37), and
Torque Shaft Seal (38) from valve mounting side
of actuator.
4.
Remove Torque Shaft (20) by tapping with a soft-
faced hammer. Use care not to drop shaft or
Bearing (12) as they come out. After removal of
Torque Shaft (20) repeat step 3 on accessory side.
FCD AXAIM00010-00
(AUTO-10) 08/04
Page 2 of 4
Reassembly Procedures
1.
Inspect all parts for wear and replace any worn
parts as needed. Normally all seals and gaskets
should be replaced when reassembling an actuator.
2.
Clean and grease all components with a multipurpose
“polymer” fortified grease such as DuBois Chemical
MPG-2. (Different greases may be required for low or
high temperatures; consult factory).
3.
Reverse the disassembly procedures to reassemble.
Use the proper torque from the torque chart on the Tie
Rod Locknuts (28), the Adapter Bolts (43), the Spring
Cartridge Nuts (41), and the Piston Bolt (25). These
threads should be lubricated with Locktite
Threadlocker 242 or equivalent prior to assembly.
4.
See attached drawing which depicts all required
spare parts.
5.
Test the actuator for smooth operation and hydraulic
leakage at service pressure before re-installing.
© TriCom, Inc., 2004, All Rights Reserved.
(AXAIM00010) KP 8/13/04 3:33 PM Page 2