Foam markers, Dye markers, Tank rinse systems – Smithco Turf Spraying Guide User Manual
Page 16
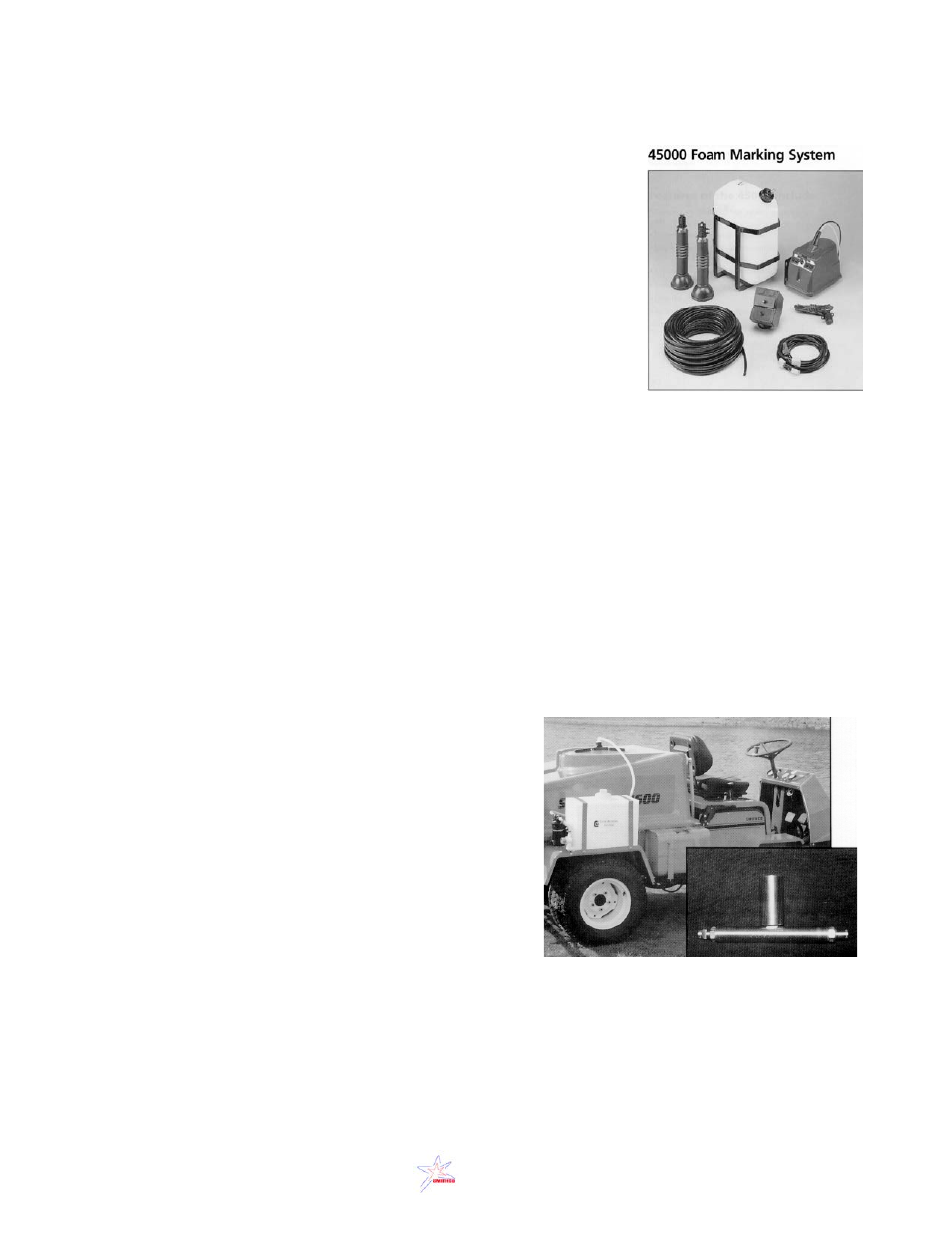
2. Foam Markers
A good spray practice is the use of some device to mark the outside
boundaries of each spray swath. Foam markers are advisable. Foam
Markers are used to mark the overlap area of the end of the boom for
making a return pass. They minimize the chance for missed areas or
double application.
They are devices that generate foam balls using a water and soap
mixture in a tank by pumping air into the mixture. Pressure forces it out
through some hosing from the foam generator to the ends of each
boom. Foam markers usually only can drop foam balls on one side of a
boom at one time. A newer foam marker made by Spraying System
differs in that the mixture and the air are both pumped out to the end of
the boom in smaller, separate tubes. Electric switches with red indicator
lights control the side that foam is dropped. This allows the user to generate foam much more quickly
(in as little as 10 seconds) to insure that the overlap patterns are accurate. And because it quickly and
reliably generates foam, balls can be dropped on both sides of the boom by switching left and right
sides on and off so that the first pass can be down the middle of the fairway.
3. Dye Markers
For many years, Blue dye has been added to spray tanks to mark where an operator has already
sprayed chemicals. Although very accurate, it leaves unsightly colored patches where it’s been put
down. It can also come off on the shoes and clothing of club members as well as being quite
expensive. Many members of golf clubs don’t like its use for these reasons. Dye markers are similar to
foam markers in function as these are devices are essentially small sprayers mounted to a larger spray
rig. They pump concentrated dye out of a pony tank to the end of the boom to put down a thin strip of
blue dye to mark the overlap pattern. It uses Tee-Jet flat fan tips mounted in the direction of travel to
keep the width of the mark to a minimum. While new to the market, its use is sure to grow.
4. Tank Rinse Systems
To properly dispose of chemical left over in spray tanks,
many EPA regulations state that the tank must be rinsed
with a neutralizing agent (Cleary’s, Neutrasol, etc.) and
then the sprayer driven back out onto the course to boom
spray the rinsate out at the original rate. Tank rinse
systems have been designed to easily solve this problem.
Again, a pony tank is mounted in a suitable position on the
sprayer so that the operator can pre-mix the neutralizing
agent to take out on the golf course (or other turf area).
The system includes an electric diaphragm pump and
hose that connects to a special nozzle mounted inside the
tank. The nozzle has opposed jets that spin when the
hydraulic pressure of the pump is turned on. When the operator is finished spraying for that event,
instead of returning to the maintenance area to mix and rinse, he simply flips a switch on the dash of
the sprayer, engaging the system. It takes approximately three minutes to empty the tank, the nozzles
cover 100 percent of the interior of the tank (up to 300 gallons), and then the operator turns on the
boom to drain the rinsate out. The time saving is substantial, as well as showing any regulatory agency
that your procedures exceed their requirements.
13