Troubleshooting – Super Systems Bazooka Probe User Manual
Page 8
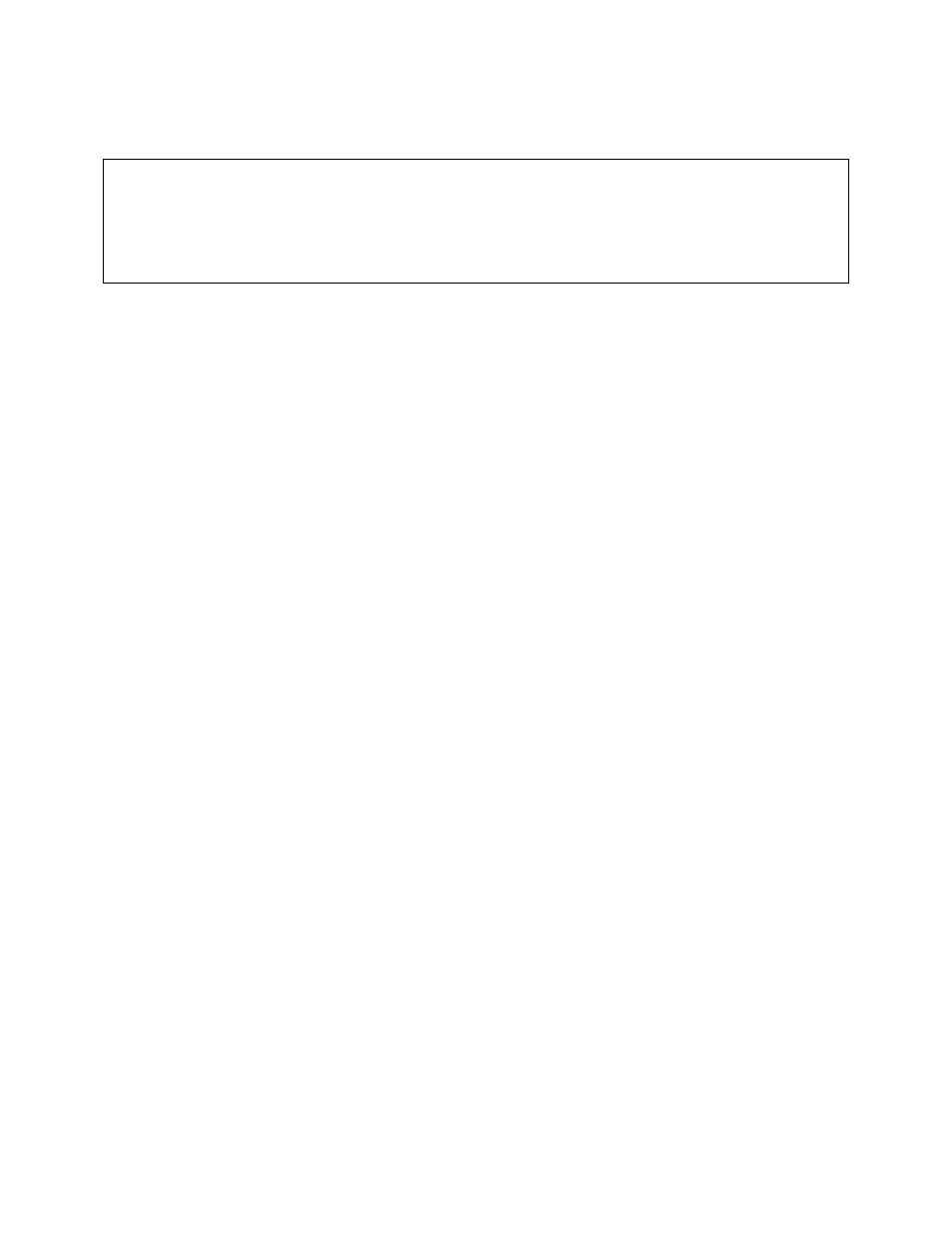
Bazooka Probe
TM
Operations Manual
Super Systems Inc.
Page 8 of 10
Troubleshooting
WARNING!
When troubleshooting, follow all proper safety precautions. Use proper eye protection and hand
protection at all times.
If problems are encountered in operation, it is necessary to verify the integrity of the probe and
its supporting equipment, the control instrument, signal transmission lines, or the process,
including the controlling elements, such as solenoid or motor driven valves. If there is
disagreement between the probe’s indicated value and dew point analysis, the following simple
tests can be conducted to eliminate the probe as a source of problems. The probe must be at
temperature and under stable control.
Reference air flow 0.5 to 1.0 CFH
•
Sample flow 2.0 to 3.0 CFH
Check the probe resistance. It should be less than 10 kilohms. If not, burn off the
probe and retest.
Test the speed of response after switching the control instrument to manual control.
First, record the mV output. Then short the probe for 5 seconds, remove the short
and measure the time required to return to within 1% of the original reading. If it
exceeds 30 seconds, conduct a burnoff and repeat the test after the reading has
stabilized.
Turn off the reference air supply for three minutes. Read the probe millivolts, and
then turn the air back on. If the reading changes (immediately) by more than 25 mV,
replace the probe. The substrate is cracked or broken.
If these fundamental tests show that the probe is functional, check the following possible
reasons for disagreement:
Contamination of the reference air supply with combustibles
Air leak into the sample line. Check with a dew pointer at the probe entry
Faulty insulation in the signal lines
Instrument out of calibration. Check with a DVM or calibrator that the instrument
reading matches the open loop probe or temperature reading.
If you experience problems and cannot find the solution after troubleshooting, please call SSi
Technical Support at (513) 772-0060.