Allstar Performance ALL18207 User Manual
Allstar Performance Spare parts
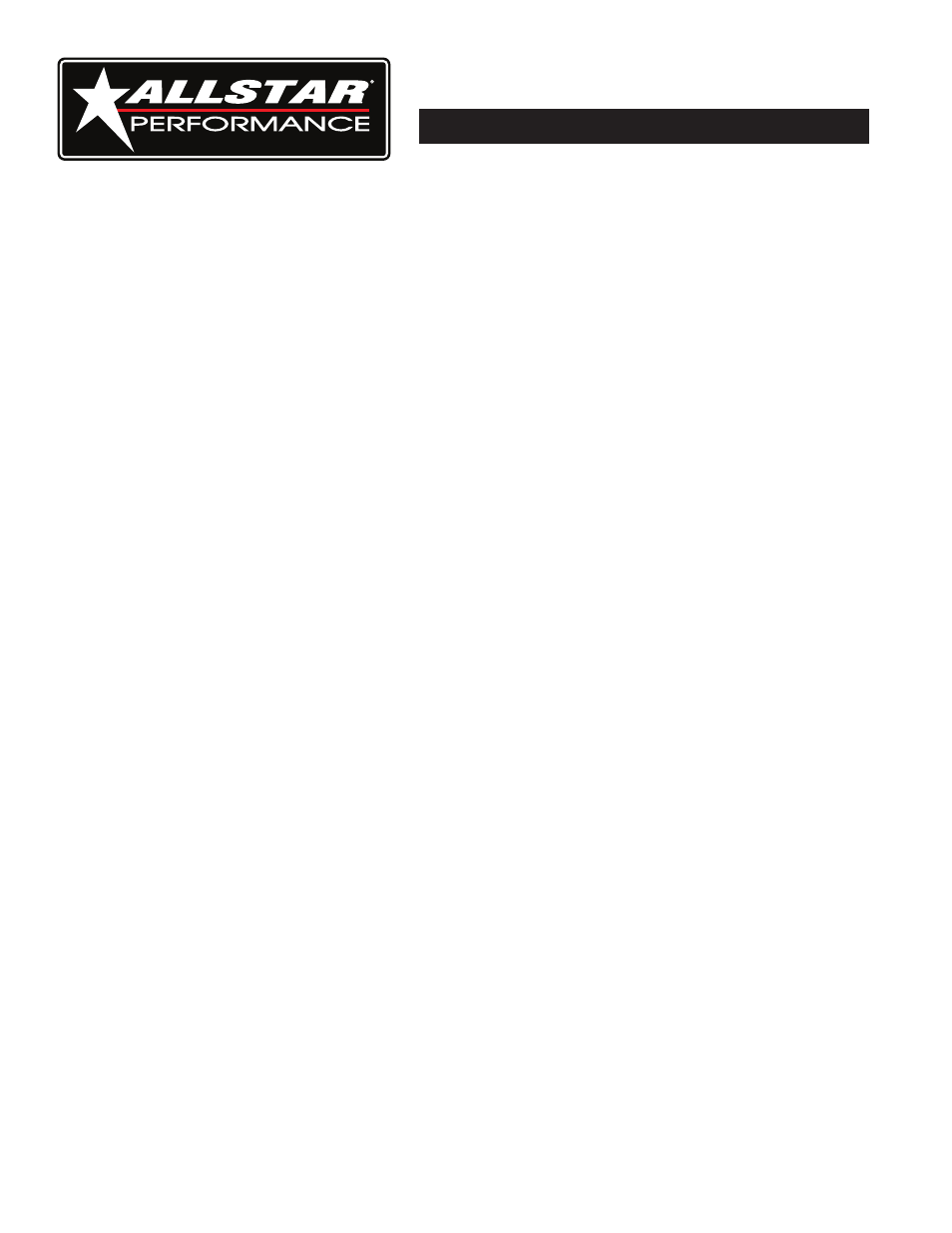
Allstar Performance 8300 Lane Dr., Watervliet, MI 49098
Phone: (269) 463-8000 Fax: (800) 772-2618 www.allstarperformance.com
Form 1134
Page 1 of 2
Rev. 022514
ALL18207
RIVET GUN INSTRUCTIONS
Specifications
Rivet Setting Capacity 3/16" diameter
Traction power 1940 lbs
Operating air pressure 85-95 PSI
Air consumption 4 CFM
Air Inlet 1/4" NPT
Malfunction
1. Mandrel gripped by jaws but rivet does not set and mandrel does not
break:
CAUSE: Low air pressure or loss of oil.
REPAIR: Increase air pressure but do not exceed 100 PSI at tool.
Make sure all fittings including frame cap and frame head are tight. If
malfunction persists, add oil as follows:
Disassemble air cylinder, frame, and frame head. Before adding oil,
check to be sure oil piston is at the bottom of its stroke, by hand pulling
jaw case front away from the frame. Oil piston should bottom its stroke
automatically when removing frame head. If jaw case front moves
downward by hand power, the return spring must be replaced. Care
must be exercised to avoid damage to O-rings. Pour machine oil into
the frame while tool is upside down. Before assembling also check for
oil appearing in air cylinder or frame head. If oil is found in any of these
areas, replace O-rings as needed. Reassemble tool.
2. Mandrel does not enter nosepiece or fails to eject.
CAUSE: Jaw case rear and nut have changed position.
REPAIR: Adjust so that the distance between the plane underside of
the frame and the front edge of the securely-assembled jaw case front
is approximately 2-13/16". This can be measured with the cut-out gauge
on spanner tool before assembling frame head
3. Tool takes more than one stroke under ideal conditions to set
rivet and break mandrel.
CAUSE: Insufficient oil.
REPAIR: See repair instructions under malfunction, 1.
CAUSE: Not enough air pressure.
REPAIR: Increase air pressure but do not exceed 95 PSI at tool.
CAUSE: Loose nosepiece.
REPAIR: Tighten nosepiece with spanner.
CAUSE: Jaw case rear too far forward.
REPAIR: See procedure under section 2 above.
Safety glasses should be worn at all times while operating tool.
General Information
The ALL18207 pneumatic/ hydraulic riveting tool is designed to set
rivets in all materials in sizes from 3/32" to 3/16" diameter. ALL18207
is supplied with a 3/16" nosepiece installed in the operating position.
Standard nosepieces for 3/32", 1/8" and 5/32" diameter rivets are also
included among the accessories supplied with the tool.
Maximum Air Pressure At Tool Is 95 PSI.
Accessories
Wrenches to service the tool are included. The spanner tool has a cut-
out gauge used in adjusting the tool as described below. The included
safety cap catches ejected mandrels when attached to the back of
tool.
Maintenance
In order to achieve maximum efficiency and economy, the ALL18207
pneumatic/hydraulic riveting tool should be serviced and maintained
on a regular basis. No special skills or tools other than the ones
provided are needed to properly service and maintain the device.
The operative parts of the tools requiring regular inspection and
maintenance are as follows:
1. The jaws should be periodically inspected, cleaned, and when
necessary, replaced with new jaws (see cleaning and changing jaws
under procedures below).
2. The frame of the tool should be checked periodically to ensure that
the oil level is maintained and that there are no leaks or breakdowns
in the seals. (See repair sections under malfunction for procedures).
Maintenance Procedures
1. Cleaning and Changing Jaws
IMPORTANT – Disconnect the ALL18207 from the air pressure line
before proceeding with inspection or repairs. Use spanner tool
to remove the frame head. Use spanner gauge to remove the jaw
case front while at the same time holding the jaw case rea with the
spanner open-end wrench. Clean jaws with solvent or a steel brush.
Replace with new jaws (Allstar replacement part ALL18209) if excess
wear is apparent. Always coat outer or smooth surface of jaws with an
oil film before assembling.
Reassemble by reversing order of above procedure. It is important
the jaw pusher engages the conical parts of the jaws. DO NOT
CHANGE THE POSITION OF PARTS. If these parts are inadvertently
changed, see readjustment instructions under malfunction.
2. Changing Nosepiece
Connect ALL18207 to air pressure and press trigger until nosepiece
has been removed and new nosepiece fully tightened. When the
trigger has been released and tool is at rest there should be a circular
opening visible in the nosepiece.