Maintenance schedule, Possible faults and related permitted remedies – Powerplus POWXQ8105 COMPRESOR 1600W 24L LUBRICATED EN User Manual
Page 7
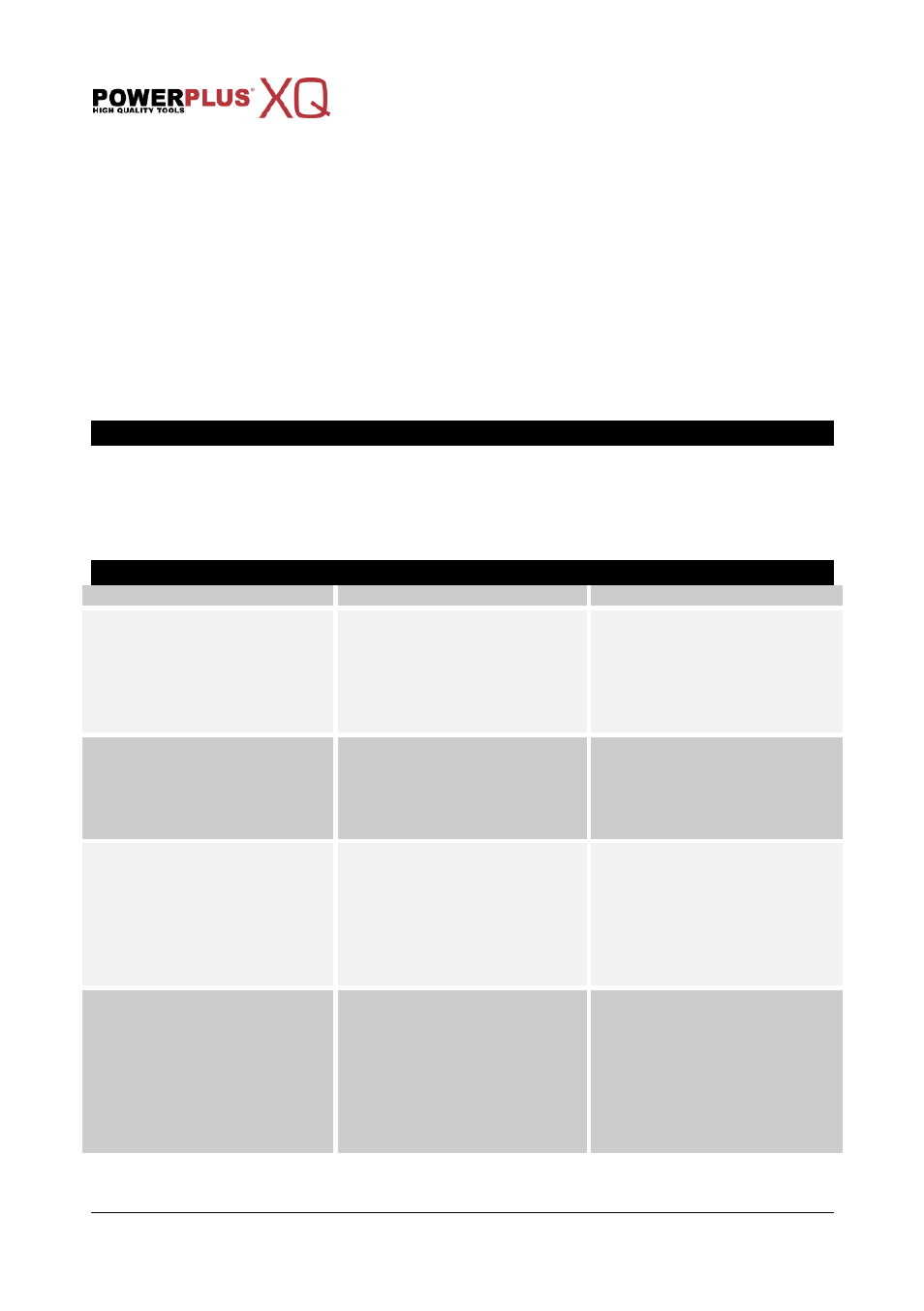
POWXQ8105
EN
Copyright © 2014 VARO
P a g e
| 7
www.varo.com
After loosening any safety screws (fig. 12a), clean the intake filter according to the type of
working environment and at least every 100 hours (figures 12b-12c). If necessary, replace
the filter element (clogging of the filter reduces compressor performance and an inefficient
filter causes increased wear).
For lubricated models, replace the oil after the first 100 hours of operation and every 300
hours subsequently (figures 13a-13b-13c). Remember to check the oil level at regular
intervals. Use API CC/SC SAE 40. (For cold climates, API CC/SC SAE 20 is
recommended). Never mix different grade oils. If the oil changes color (whitish = presence
of water; dark = overheated), it is good practice to replace the oil immediately.
Periodically (or after working with the compressor for more than an hour), drain the
condensate that forms inside the receiver (fig. 11) due to the humidity in the air. This
protects the receiver from corrosion and does not restrict its capacity.
Spent oil (lubricated models) and condensate MUST BE DISPOSED OF in accordance
with environmental protection regulations and current legislation.
10 MAINTENANCE SCHEDULE
Cleaning of intake filter and/ or substitution of filtering element: every 100 hours
Change of oil: After the first 100 hours + every 300 hours
Tightening of head tension rods: The check must be carried out prior to the first
compressor starting
Draining tank condensate: Periodically and at the end of work
11 POSSIBLE FAULTS AND RELATED PERMITTED REMEDIES
FAULT
CAUSE
REMEDY
Leakage of air from the valve
of the pressure switch with
the compressor off.
Check valve that, due to
wear or dirt on the seal, does
not perform its function
correctly.
Unscrew the hexagonal head
of the check valve, clean the
valve seat and the special
rubber disk (replace if worn).
Reassemble and tighten
carefully (figures 14a-14b).
Reduction of performance.
Frequent start-up. Low
pressure values.
Excessive performance
request, check for any leaks
from the couplings and/or
pipes. Intake filter may be
clogged.
Replace the seals of the
fitting, clean or replace the
filter.
The compressor stops and
restarts automatically after a
few minutes. In the V, 3 HP
versions, it is does not start.
Tripping of the thermal cutout
due to overheating of the
motor.
Clean the air ducts in the
conveyor. Ventilate the work
area. Reset the thermal
cutout. On lubricated and V
type models, check oil level
and quality. On V models,
have the voltage checked.
After a few attempts to
restart, the compressor.
Tripping of the thermal cutout
due to overheating of the
motor (removal of the plug
with the compressor running,
low power voltage).
Activate the on/off switch.
Ventilate the work area. Wait
a few minutes. The
compressor will restart
independently. On V, 3 HP
models, reset the thermal
cutout. Remove any power
cable extensions