Technical information 6. maintenance – Sealey SGA1 User Manual
Page 5
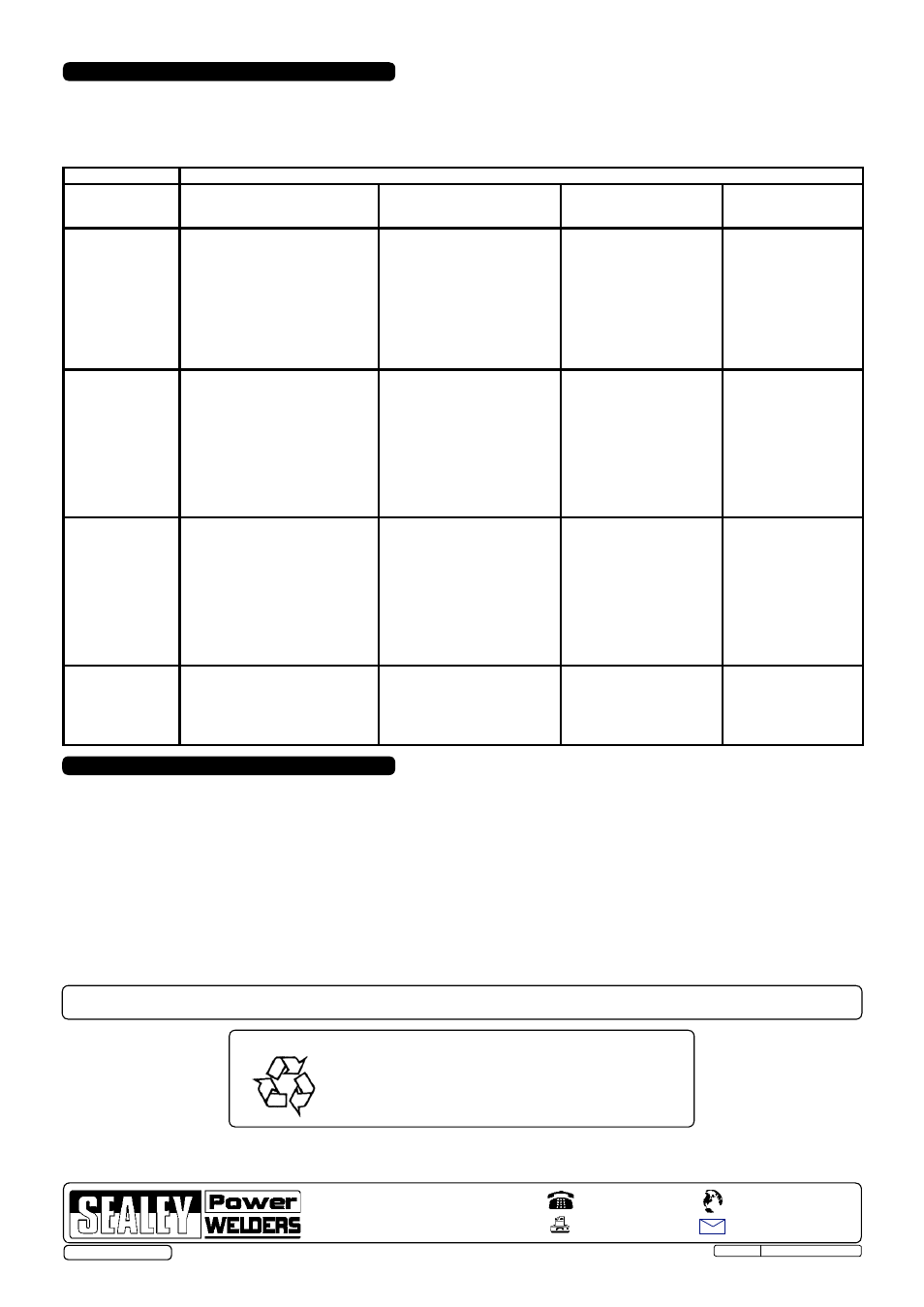
01284 757500
01284 703534
www.sealey.co.uk
Web
NOTE:
It is our policy to continually improve products and as such we reserve the right to alter data, specifications and component parts without prior notice.
iMPORtant: no liability is accepted for incorrect use of this product.
waRRantY: guarantee is 12 months from purchase date, proof of which will be required for any claim.
inFORMatiOn: for a copy of our catalogue and latest promotions call us on 01284 757525 and leave your full name, address and postcode.
7.1 cuttinG caPacities
Mild
nozzle
Operating Pressure (bar - lbf/in²)
Gas consumption (ltr/m - ft³/h)
steel size
Oxygen acetylene
O2 - cutting
O2 - Heating
acetylene
6mm / 1/4”
1/32”
1.4 - 20
0.30 - 4
14.15 - 30
8.5 - 18
8.0 - 17
13mm / 1/2”
3/64”
2.1 - 30
0.35 - 5
30.70 - 65
10.4 - 22
9.4 - 20
25mm / 1”
1/16”
2.8 - 40
0.40 - 6
67.50 - 143
13.2 - 28
11.8 - 25
50mm / 2”
1/16”
3.1 - 45
0.40 - 6
78.30 - 166
13.2 - 28
11.8 - 25
75mm / 3”
1/16”
3.5 - 50
0.40 - 6
88.70 - 188
13.2 - 28
11.8 - 25
7.2 weldinG caPacities
Mild
nozzle Operating Pressure (bar - lbf/in²)
Gas consumption (ltr/m - ft³/h)
steel size
Oxygen acetylene
O2 - welding
O2 - Heating
acetylene
1.2mm / 18sWg
lW02
0.14 - 2
0.14 - 2
11.8 - 25
4.2 - 9
3.8 - 8
2.6mm / 12sWg
lW05
0.28 - 4
0.21 - 3
23.5 - 50
4.2 - 9
3.8 - 8
4mm / 8sWg
lW10
0.35 - 5
0.28 - 4
56.6 - 120
4.2 - 9
3.8 - 8
7. tecHnical inFORMatiOn
6. Maintenance
6.1
Annual maintenance should be carried out by a person who has sufficient practical experience of oxyacetylene gas equipment and a
detailed theoretical knowledge of the functioning of the equipment, the properties of gases used and potential defects and hazards
which may occur and their importance to the integrity and safety of the equipment.
6.2
regulator elastomers and seals will wear and deteriorate in service and will also deteriorate out of service. regulators stored for 1
year or over without use should receive inspection as per the annual maintenance schedule.
eQuiPMent
Maintenance
each time equipment is used
annual
Replacement/
Replacement/
(By the operator)
Refurbishment
Refurbisment
intervals
Guideline
regulAtors
Visual examination to determine
functional tests to ensure
5 years or manufactuers
replace with a new,
and their
suitability for service (e.g. correct correct operation
recommendations.
repaired, or service
integral protective gas, pressure rating, damage,
note: If regulators are
exchange unit.
devices.
condition of threads and sealing
repaired or refurbished
surfaces, oil or grease
this shall be done in
contamination.
accordance with the
BcgA code of practice
leak test all joints at working
cP17 by a reputable
pressure.
repairer.
flAsHBAcK
Visual examination to determine
check unit for flow restriction. 5 years or manufacturers
replace with a new,
Arrestors
suitability for service (e.g. gas,
reverse flow to ensure
recommendations.
repaired, or service
and their integral
pressure rating, damage,
correct operation of non-return
exchange unit.
cut off valves
condition of threads and sealing
valves and pressure sensitive
surfaces, oil or grease
cut off valves where fitted. If
contamination.
of the pressure sensitive type
check shut off in the tripped
leak test all joints at working
condition in the direction of
pressure.
flow.
Hose
Visual safety check to determine
reverse hose to ensure the
determined by local
replace as required.
AsseMBlIes
suitabilty for service (e.g gas,
correct operation of non-return operating conditions.
(including non-
pressure rating, damage),
valve where fitted. Bend hose
return valves )
condition of cover (e.g. kinking
in a tight radius to ensure
and twisting ), threads and
reinforcement is not visible.
sealing surfaces. check
anti-whip restraints where fitted.
leak test all joints at working
pressure.
BloWPIPes
Visual examination of the nozzle
test valve functions. Blank
determined by local
replace with a new,
and inlet seatings for damage.
exits and leak test for internal operating conditions.
repaired, or service
leak test all joints at working
malfunctions.
exchange unit.
pressure.
© Jack sealey limited
Original Language Version
sgA1.V3 Issue: 1 - 27/09/13
sole uk distributor, sealey Group,
Kempson Way, suffolk Business Park
,
Bury st. edmunds, suffolk, IP32 7Ar
environmental Protection.
recycle unwanted materials instead of disposing of
them as waste. All tools, accessories and packaging
should be sorted, taken to a recycle centre and
disposed of in a manner which is compatible with the
environment.
Parts support is available for this product. to obtain a parts listing and/or diagram, please log on to www.sealey.co.uk
or phone 01284 757500.