Vogt valves, Bolted bonnet ball check valves, Bolted bonnet swing check valves – Flowserve Vogt Forged Steel Gate User Manual
Page 41
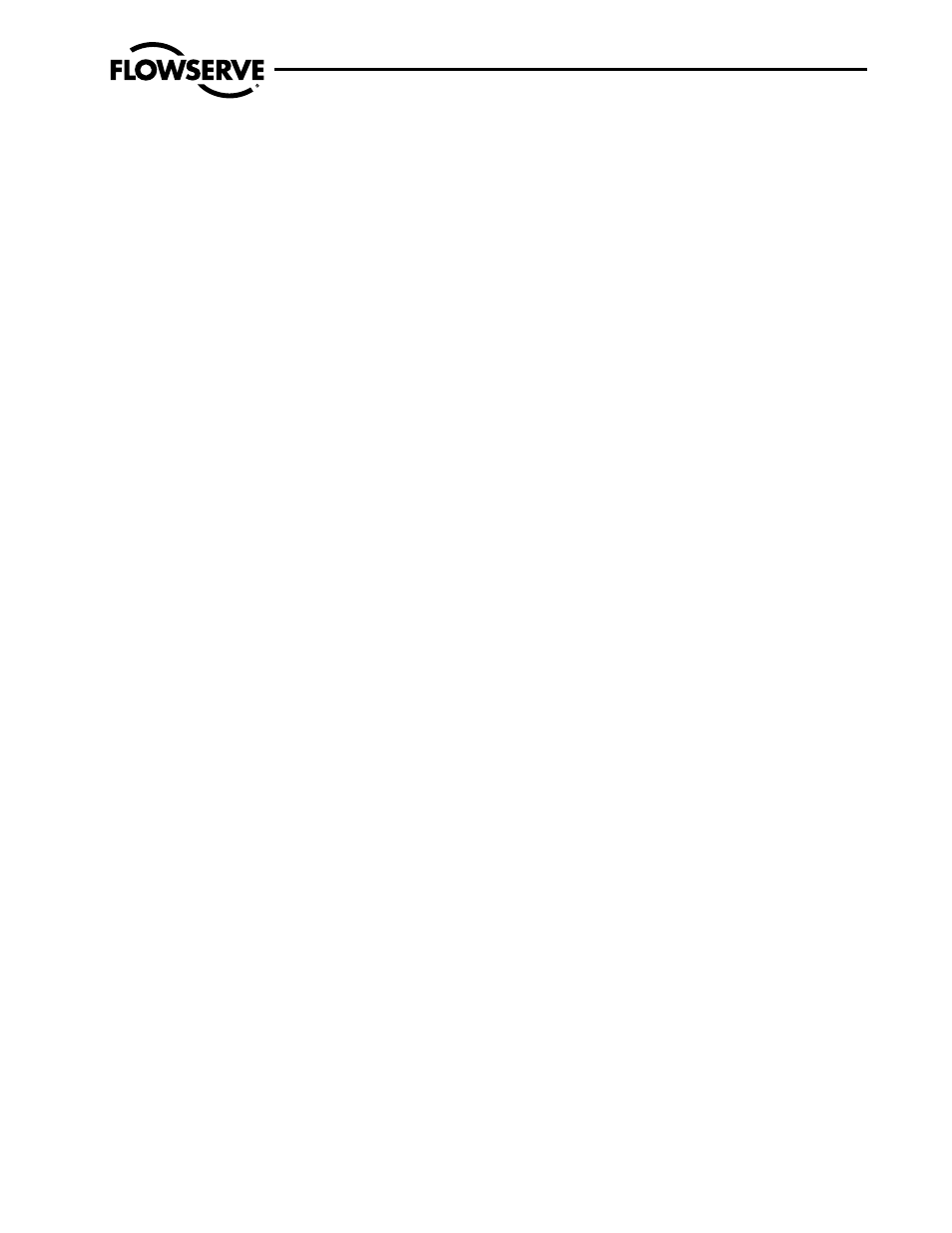
Flow Control
Vogt Valves
FCD VVENIM2000-02
Forged Steel Gate, Globe and Check Valves
41
4. If the gasket surface is not damaged and/or has been refur-
bished per the above machining process, replace the gasket
with a gasket part number noted in the Recommended Spare
Parts List of Section 1. Gaskets are available from distribution
on short notice.
5. Place the bonnet subassembly back on the valve and install the
bonnet bolting. Torque the bonnet bolting in accordance with
the torque requirements of Bonnet Torque Requirements of Sec-
tion 5.
6. Test the valve and, if acceptable, place back in service.
Valve Seat Leaker
1. Remove the bonnet. Inspect body, bonnet, and bonnet bolting.
2. Note any rust on the body, piston or disc. Internal rusting may
cause the valve to stick and close improperly.
3. Clean rust from valve.
4. Inspect the valve seat. If the seat has imperfections deeper than
0.010", repair may not be economical and may be impossible.
5. If the imperfections are less than 0.010" the valve seating
surfaces can be brought back into like-new seating condition by
lapping the piston/disc to the body seat.
6. Flowserve has a special lapping tool that will engage the piston
and allow it to be rotated during the lapping process. Tool num-
bers are available from Flowserve.
7. The lapping process requires the piston/disc to be rotated
against the body seat with a lapping compound between the two
parts. The rotation of the piston can be done manually or with a
low-speed air tool. Rotation of the piston with an air tool should
be on the order of 40 rpm. Downward force should be limited to
the weight of the tool.
8. For the lapping process two grades of lapping compounds shall
be used. The first lapping shall be done with the following grade
of compound:
Fel Pro
Clover Sharpening Compound
Silicon Carbide
Water Soluble Gel
120 grit Part No. 51846 E
Coarse
This compound removes a considerable amount of metal and
should take 3–5 minutes to refurbish the seating surfaces.
Discontinue when the disc and body have continuous lapping
lines on the seating surfaces.
The final lap shall be done with the following grade of
compound:
Clover Grade 1A
320 Grit
Very Fine
The final lap should be 3–5 minutes depending on the appearance
of the lapping line on the piston. Since Vogt check valves have a line
contact, a continuous lapping line of width 0.040–0.050" is normal.
The lapped body shall have a similar continuous line. The piston
and body that have been lapped to each other shall be assembled
together.
The normal appearance of a properly lapped valve would be as
follows:
The disc would have a continuous black line when it is cleaned of the
lapping compound. The lapping compound is water-soluble and can
be cleaned with water. The black line represents the lapped surface.
The body should have a similar continuous black line as well, of
similar width. The lapping compound can be cleaned with water.
Once the body and piston have a continuous lapped line of contact,
the valve can be reassembled, tested and placed back in service.
Bolted Bonnet Ball Check Valves
The previous procedures apply except that the lapping of the body
seat shall be done with a Vogt piston normally used with the valve.
This restores the seat in the valve body. The ball shall be inspected
and replaced if it contains any nicks that would cause leakage.
Bolted Bonnet Swing Check Valves
Bonnet leakers shall be handled per the above. Call Flowserve for
gasket part numbers. Seat leakers for removable seat valves shall be
corrected as follows:
1. Remove the seats.
2. Lap the seats on a flat plate.
3. Remove the clapper and lap on a flat plate.
4. Reassemble the bonnet subassembly and valve body. Ensure
that the clapper mechanism has the correct orientation to the
seat. Rotate bonnet slightly to ensure that clapper and seat have
good contact.
5. Reassemble, test and place back in service.
A persistent leakage may be the result of “cracked hard facing” on
the valve body seat. If so, the body and/or valve have to be replaced.
Cracked hard facing cannot be repaired.