Flowserve Worcester Controls Miser Ball Valves User Manual
Miser ball valves, A. installation, Wcaim2030
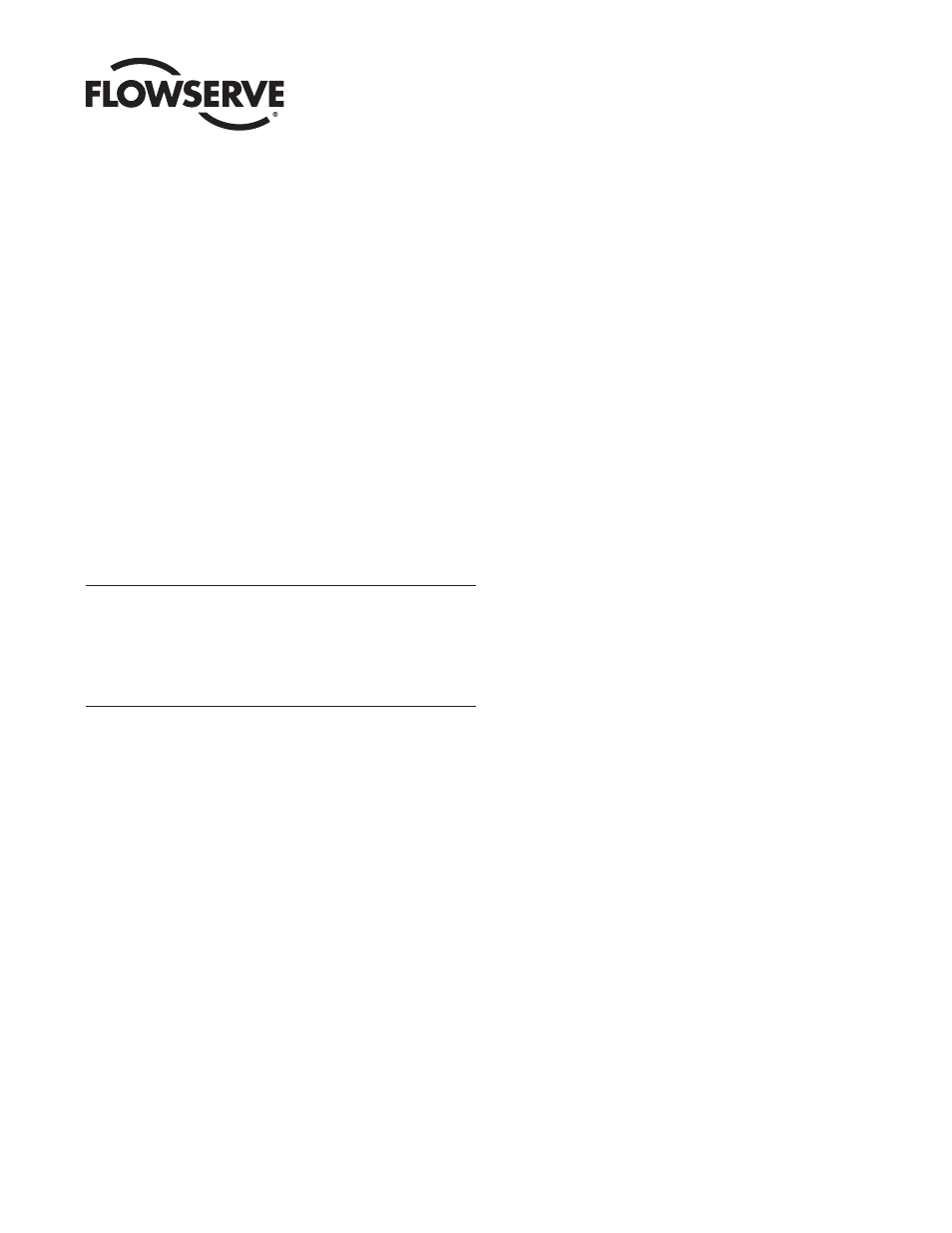
Worcester Controls
WCAIM2030
(Part 16474)
Miser Ball Valves
Installation, Operation and Maintenance Instructions
CAUTION: Flowserve recommends that all product which must be
stored prior to installation be stored indoors, in an environment
suitable for human occupancy. Do not store product in areas where
exposure to relative humidity above 85%, acid or alkali fumes,
radiation above normal background, ultraviolet light, or
temperatures above 120°F or below 40°F may occur. Do not store
within 50 feet of any source of ozone.
A. INSTALLATION
1. Miser valves may be installed for flow or vacuum in either
direction. Use care to exclude pipe sealants from the valve
cavity. Valves with upstream relief hole in ball (V3 option) are
one-way valves.
Miser Diverter Valves (D) may be installed using the bottom port
as the inlet port. The flow can then be diverted to either one of the
two side outlet ports.
Miser Three-Way Valves (T) may be installed using any of the
ports as inlet or outlet ports. The source can be selected from
either of two sources to be directed toward one outlet. It can also
be selected from one source to one outlet and then, by rotating
the valve, use that outlet as an inlet and use the third port as the
new outlet. The three-way valve does not have separate body
seals. This function is incorporated into the three-way seat.
Therefore, more care than normal must be taken to not damage
the back face of this seat upon disassembly and reassembly.
Note that for CL44 valves, the maximum pressure rating is 300 psi
per Chlorine Institute. The Chorine Institute recommends that the
relief hole in the ball be upstream, toward the pressure source. An
arrow stamped on the body or on a metal tag welded to the body
indicates flow path.
2. Weld End Valves (TE, SW, BW, SWO, XBO):
NOTE: Prior to welding or brazing, THOROUGHLY CLEAN ALL
JOINT SURFACES to prevent contamination. Worcester brass
valves are of leaded forging brass. Brazing can not be
successfully accomplished unless a white flux is used.
Valves with “PG”, “RG”, “XG”, “AG”, and “GG” seat and body seal
combinations and V67 option code are compatible with welding
temperatures. Therefore, these valves are weld-as-is and do not
have to be disassembled to be welded in the line. These valves
will have a red welding tag attached. If these valves are
disassembled, the graphite-coated stainless steel gasket body
seals and the seat back seals (used with “A” or “G” seats only)
must be replaced. When welding these valves, the ball must be
open to prevent adhesion of weld spatter to the ball. Use STICK or
MIG welding, and allow valve and joint to cool to the touch
between passes.
Valves with XBO pipe ends can be welded in line as assembled.
For all other weld, braze or solder valves:
a. Tack weld valve in place.
b. With valve open, remove three body bolts, loosen fourth and
swing out body.
NOTE: AF44 and FZ44 fire valves can not be swung out.
Remove fourth bolt and spread pipe ends to clear centering
ring, if any (rings are no longer used with revision R4 and
later fire valves are fire valves with “G” seats.).
Close valve, remove ball, seats, body seals or one-piece
(three-way) seat/body seals.
Return body to its original position and temporarily secure it
with two body bolts diagonally opposite each other.
1
/
4
" - 2" 4, 44 — Includes CL, H, MP, PT, S, W, W2 and WK44 Series
1
/
2
" - 2" D, T and FZ series
1
/
4
" -
3
/
8
" AF Series
1
/
4
" - 1
1
/
2
" 59 — Includes PT, W and W2 Series