Flowserve Valtek ShearStream HP Control Valves User Manual
Page 3
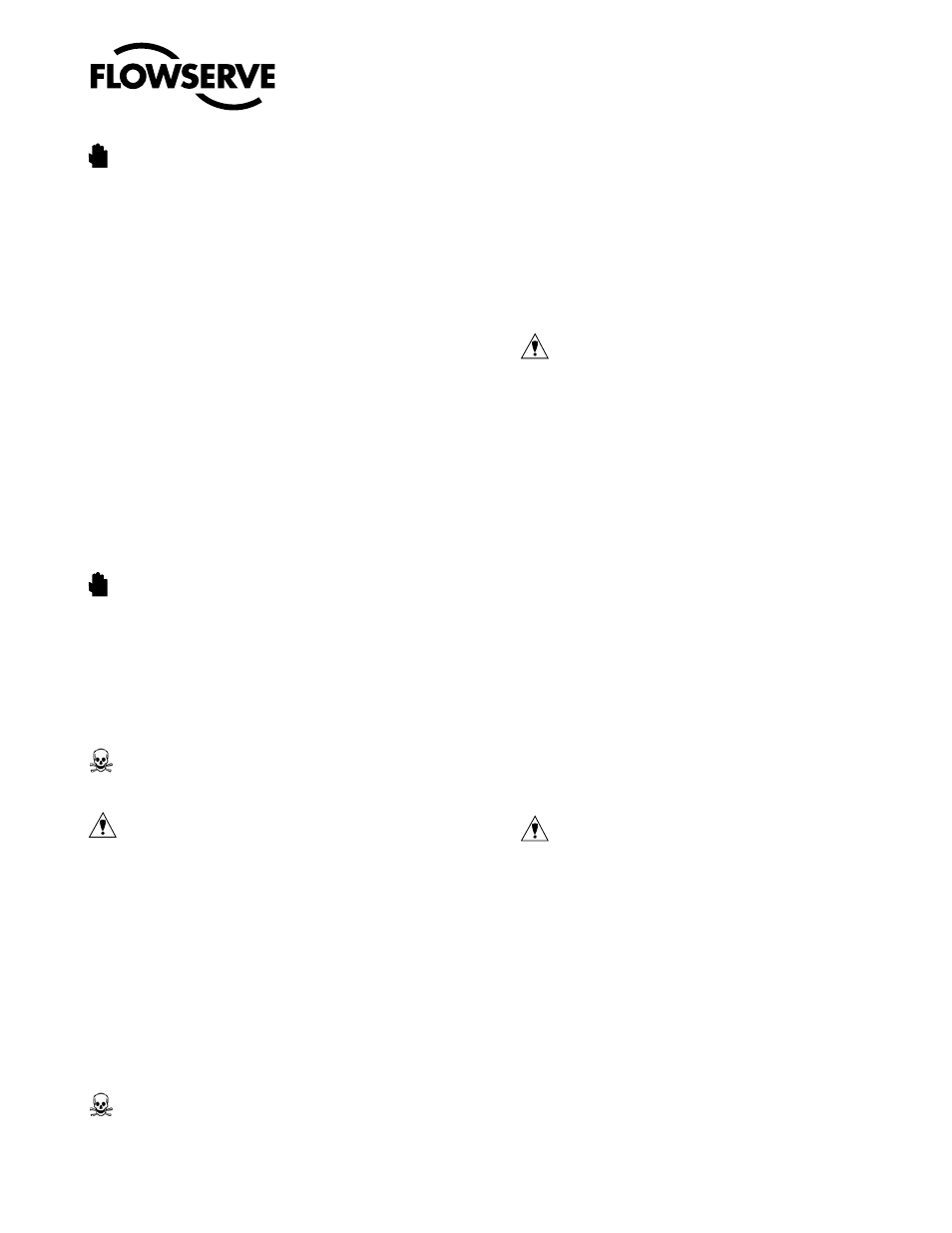
®
User instructions - Shearstream HP - VLENIM0027-01 03.08
3
WARNING: Before products are returned to Flowserve for
repair or service, Flowserve must be provided with a cer-
tificate that confirms that the product has been decontami-
nated and is clean. Flowserve will not accept deliveries if a
certificate has not been provided (a form can be obtained
from Flowserve).
.8
Storage
In most cases, Flowserve products are manufactured from
stainless steel. Products not manufactured from stain-
less steel are provided with an epoxy resin coating. This
means that Flowerve products are well protected from cor-
rosion. Nevertheless, Flowserve products must be stored
adequately in a clean, dry, environment. Plastic caps are
fitted to protect the flange faces and prevent the ingress of
foreign materials. These caps should not be removed until
the valve is actually mounted into the system.
2
UNPACkING
.
While unpacking the valve, check the packing list against
the materials received. Lists describing the valve and acces-
sories are included in each shipping container.
.
When lifting the valve from shipping container, use straps
through the yoke legs. Take care to position lifting straps to
avoid damage to the tubing and mounted accessories.
WARNING: When lifting a valve be aware that the center of
gravity may be above the lifting point. Therefore, support
must be given to prevent the valve from rotating. Failure to
do so can cause serious injury to personnel and damage to
the valve and nearby equipment.
.3
Contact you shipper immediately if there is shipping damage.
.4
Should any problem arise, call your Flowserve representa-
tive.
DANGER: Before installation check the order number, serial
number, and/or the tag number to ensure that the valve and
actuator being installed are correct for the intended applica-
tion.
CAUTION: Do not insulate extensions that are provided for
hot or cold services.
3
INSTALLATION
3.
Before installing the valve, clean the pipeline of all contami-
nation, carbon deposits, welding chips, and other foreign
material. Carefully clean gasket surfaces to ensure a tight
seal. Pipelines must be correctly aligned to ensure that the
valve is not fitted under tension.
3.
Fire protection must be provided by the user.
3.3
Check the direction of fluid flow to ensure that the valve
is correctly installed. Flow direction is indicated by the ar-
row attached to the body. All installation orientations for fit-
ting the valve into the pipeline are defined at the end of this
manual.
DANGER: To avoid serious injury, keep hands, hair, clothing,
etc away from the ball and seat when the valve is working.
3.4
Whenever possible, the valve should be installed so that
actuator is in an upright position. Vertical installation of the
actuator permits easier valve maintenance.
3.5
Connect the air supply and instrument signal lines. Throt-
tling control valves are equipped with a valve positioner.
Connections are marked for the air supply and the instru-
ment signal. Check that the actuator and positioner can
withstand the maximum air supply from the network. The
required air supply is indicated on a sticker located on the
actuator. An air regulator will be necessary in certain cases
in order to limit the supply pressure. A filter is recommend-
ed unless the air supplied is exceptionally clean and dry (air
quality without humidity, oil, or dust as per IEC 770 and
ISA-7.0.0). All connections must be completely tight.
CAUTION: On valves equipped with air filters, the air filter
must point down to perform properly.
3.6 Use the bolts indicated in Table I for installing the valve in
the pipeline, and then tighten alternately according to good
practice. The user must in all cases confirm the capacity of
the bolts to ensure a sufficiently tight gasket seal for the
expected service conditions.
3.7
Be sure to provide proper overhead clearance for the ac-
tuator to allow for disassembly of the actuator from the
valve body. Refer to the appropriate to the ShearStream HP
Technical Bulletin for proper clearances. ShearStream HP
Technical Bulletin is available at www.flowserve.com.
4
QUICk-CHECk
Before commissioning, check the control valve by follow-
ing these steps:
4.
Check for full stroke by varying the instrument signal set-
tings appropriately. Observe the ball position indicator
located on the actuator or the positioner. The ball should
change position with a smooth turning movement.
4.
Check all air connections for leaks. Tighten or replace any
leaking lines.
4.3
Check packing box bolting for proper tightness.
CAUTION: Do not overtighten packing. This can cause ex-
cessive packing wear and high stem friction that may im-
pede shaft movement. After the valve has been in service
for a short period, recheck the packing-box nuts. If the
packing-box leaks, tighten the nuts just enough to stop the
leak.
4.4
Make sure the valve fails in the correct direction in case
of air failure. This is done by positioning the valve at mid-
stroke and turning off the air supply and observing the
failure direction. If the action is incorrect, see the section
“Reversing the Air-action” in the instructions of the installa-
tion, operation and maintenance manual of the appropriate
actuator.
5
PREVENTATIVE MAINTENANCE
At least once every six months, check for proper operation
by following the preventative maintenance steps outlined
below. These steps may be performed while the valve is in-
line and without interrupting service. If an internal problem
is suspected, refer to section “Valve Disassembly”.
STOP!
STOP!