0 maintenance requirements – Flowserve 1878 Piston Check Valve User Manual
Page 6
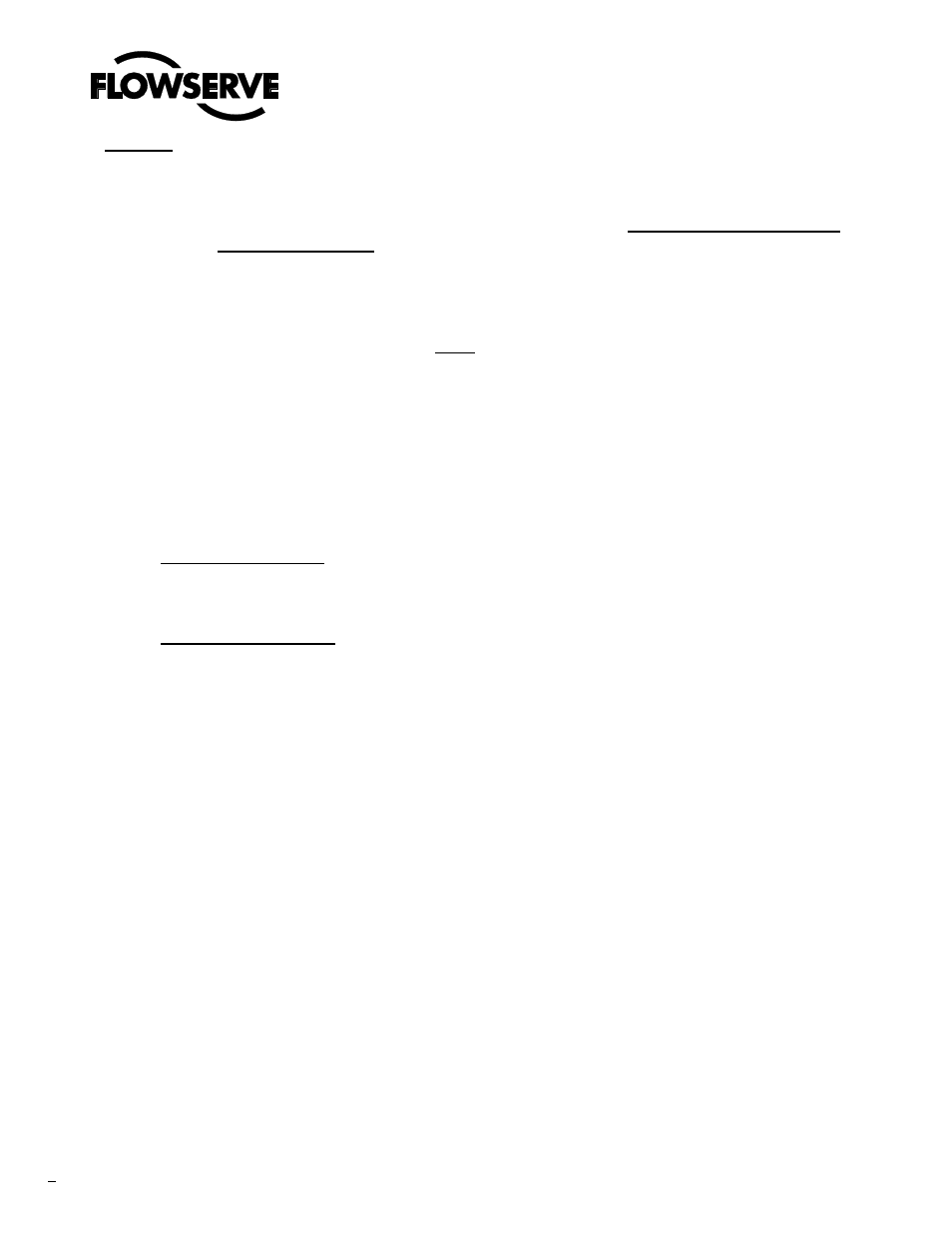
1878 Piston Check Valves FCD ADENIM0005-00
6
6.2
Installation (Continued)
6.2.3
Extreme caution should be taken when installing check valves. The arrow on the valve body
indicates flow direction. Therefore, when installing a check valve, place it so that the flow of the
incoming fluid will open the valve and return flow will close it. Check valves installed in reverse
position will stop the flow in the normal flow direction. Valves should be installed in a horizontal run
of pipe with the bonnet cap on top. Maximum deviation from the horizontal should be ± 15
°
.
6.2.4
The valves should then be blocked or slung into position with apparatus that is sufficient to hold the
valve assembly weight while the valve is being welded into the line. WELDING SHOULD TAKE
PLACE WITH THE DISC IN THE OPEN POSITION. This is particularly important for valves with
soft seats. Welding the valve with the disc closed will damage the resilient seat material. This may
require removal of the internals prior to welding.
6.2.5
Remove the end protectors and clean the ends with a solvent such as acetone in preparation to
welding.
7.0 Maintenance Requirements
7.1
Preventative Maintenance
7.1.1
Check all bolts periodically to ensure tightness and to forestall possible leaks.
7.2
Recommended Spare Parts
7.2.1
Recommended spare parts are pressure seal gasket (030), bonnet (002), disc assembly (004 &
005,245 & 306 if equipped with resilient seated disc) and spring (429). The recommended quantity
is 1 set for every 10 valves.
7.2.2
For consolidating spare parts (See 7.2.1), use the following guidelines:
-
½" thru 1" Piston Check Valves
Recommended spare parts are interchangeable throughout this size range. Note that similar
materials should be ordered for valve body type (i.e. carbon steel bonnet for carbon steel valve).