Installation, Packing replacement, Seat and seal replacement – Flowserve DI-B800 User Manual
Page 2: Mccanna/marpac
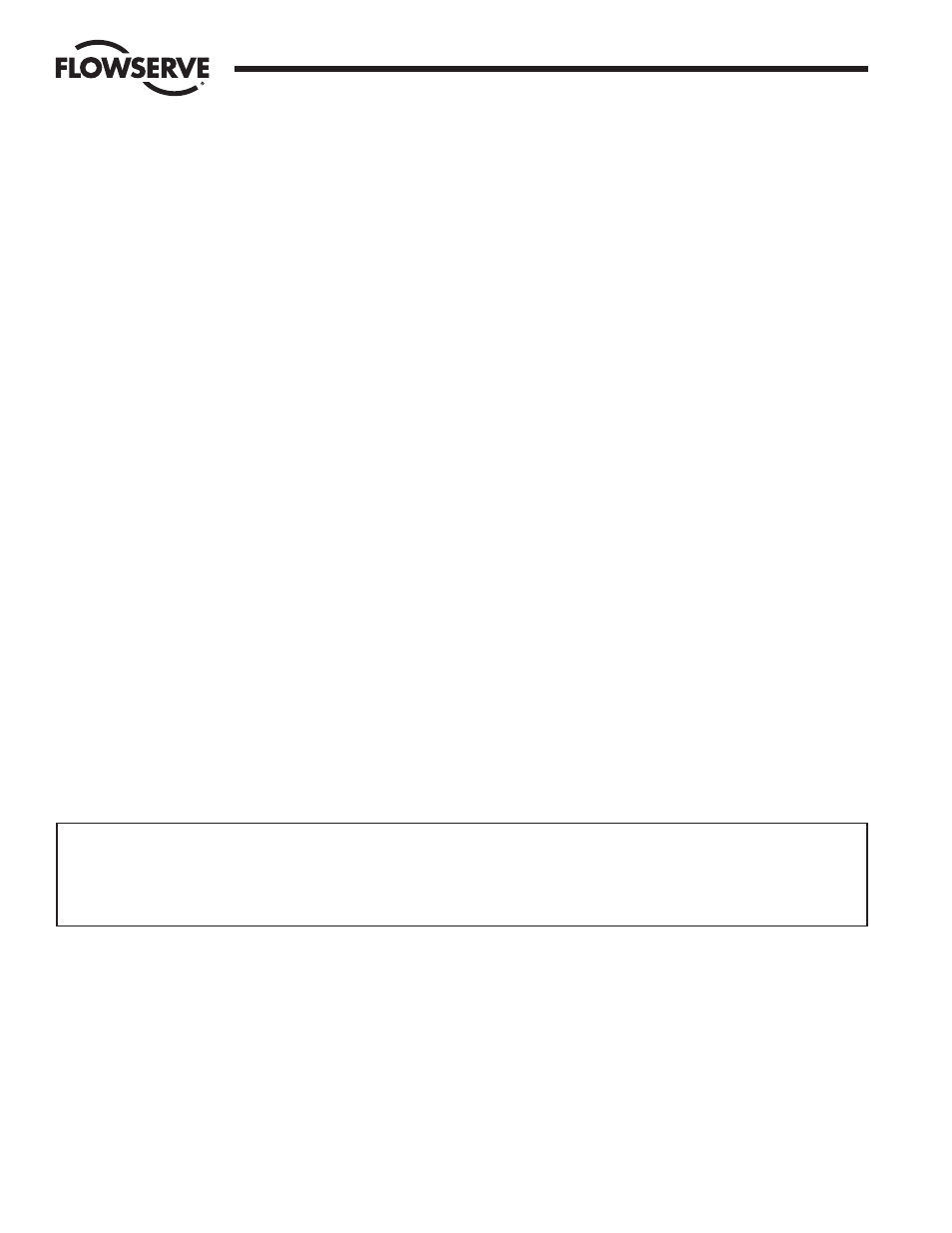
1. Installation
A. Good operating procedure requires periodic observation to ensure that
the valve is functioning properly. The frequency of observation will
depend on the application.
B. This valve may be installed in any position, utilizing standard pipe fitting
practices. Flow can be in either direction.
C. Periodically check and tighten body bolts (12) and two gland bolts (14).
D. If leakage is evident in stem packing area, tighten two gland bolts (14)
evenly, a little at a time. If leak persists replacement of stem packing (8)
is indicated (See Packing Replacement below).
2. Packing Replacement
There must be no line pressure on the valve at this time.
A. Remove lever of tee handle, not shown in Figure 1 (optional equipment).
B. Loosen “allen” type set screw (17) in stop plate (13) and lift off stop
plate.
C. Completely unscrew both 5/8" gland bolts (14) and remove stop washers
(15) and gland flange (16).
D. Remove stem (7) by following steps 4A through 4D under Seat and
Seal Replacement. At this point, push down on stem (7) and remove it
from body (4).
E. Remove thrust washer (6) from stem (7) and remove stem packing (8)
and gland (11) from stuffing box.
Reassembly
A. Place one thrust washer (6) on stem (7) and insert stem into body (4)
and up through the body.
B. Follow steps A through G of Reassembly procedure under Seat and
Seal Replacement.
C. Three rings of packing (8) are then dropped over the stem (7).
D. Drop gland (11) over stem (7).
NOTE: When stem packing (8) is fully shouldered on stem (7), gland
(11) will project approximately 1/8" out of stuffing box.
E. Gland flange (16) and gland bolts (14) with stop washers (15) are then
replaced in that order.
F. Put stop plate (13) over stem square and tighten set screw (17).
G. If valve comes equipped with handle, replace.
3. Seat and Seal Replacement
There must be no line pressure on the valve at this time.
A. Unscrew six 1/4" hex head body bolts (12).
B. Remove body end (1). One seat (3) should come out with body end (1).
Remove end seal (2) from body (4).
C. Rotate stem (7) so ball (5) is in fully closed position and remove ball (5).
NOTE: Extreme caution should be taken to avoid damage to the
ball surface.
D. Take out other seat (3).
Flowserve recommends replacement of all soft parts whenever the valve
is dissassembled for reconditioning (See Section 2, Packing
Replacement). The replacement parts can be ordered in kit form.
Reassembly
A. Place one seat (3) in body.
NOTE: Seats are to be installed with concave surface positioned against
the ball.
B. Turn the stem (7) to a position with the lower stem tang flats parallel to
the ball cavity of the body.
C. Install the ball (5).
NOTE: Ball should be carefully examined for nicks, scratches, pitting or
corrosion and replaced as necessary.
D. Put body seal (2) into shouldered counterbore in valve body (4).
E. Place other seat (3) into body end (1) seat cavity (See NOTE under
Reassembly, Section 2A).
F. Put body end (1) back into body (4) and line up bolt holes.
NOTE: Be careful not to damage body seal (2) when putting body end
(1) into body (4).
G. Evenly torque six body bolts (12) back into place.
Flow Control Division
McCANNA/MARPAC
Flowserve Corporation has established industry leadership in the design and manufacture of its products. When properly selected, this Flowserve product is designed to perform its intended function safely during its useful life.
However, the purchaser or user of Flowserve products should be aware that Flowserve products might be used in numerous applications under a wide variety of industrial service conditions. Although Flowserve can (and often
does) provide general guidelines, it cannot provide specific data and warnings for all possible applications. The purchaser/user must therefore assume the ultimate responsibility for the proper sizing and selection, installation,
operation, and maintenance of Flowserve products. The purchaser/user should read and understand the Installation Operation Maintenance (IOM) instructions included with the product, and train its employees and contractors in
the safe use of Flowserve products in connection with the specific application.
While the information and specifications contained in this literature are believed to be accurate, they are supplied for informative purposes only and should not be considered certified or as a guarantee of satisfactory results by
reliance thereon. Nothing contained herein is to be construed as a warranty or guarantee, express or implied, regarding any matter with respect to this product. Because Flowserve is continually improving and upgrading its
product design, the specifications, dimensions and information contained herein are subject to change without notice. Should any question arise concerning these provisions, the purchaser/user should contact Flowserve
Corporation at any one of its worldwide operations or offices.
For more information about Flowserve Corporation, contact www.flowserve.com or call USA 1-800-225-6989.
FLOWSERVE CORPORATION
FLOW CONTROL DIVISION
1978 Foreman Drive
Cookeville, Tennessee 38501 USA
Phone: 931 432 4021
Facsimile: 931 432 3105
www.flowserve.com
© 2003 Flowserve Corporation, Irving, Texas, USA. Flowserve and Worcester Controls are registered trademarks of Flowserve Corporation.
MMAIM2001 9/03 Printed in USA
NOTICE:
McCANNA Valves are designed and manufactured using good workmanship and materials, and they meet all applicable industry standards. Flowserve Corp. is anxious to avoid injuries
and property damage which could result from misapplication of the product. Proper valve selection is imperative. Examples of the misapplications or misuse of a valve include but are
not limited to use in a service in which the pressure/temperature rating is exceeded or in a chemical service incompatible with the valve materials; use of undersized valve actuators;
use of extremely fast valve actuation and/or continuous valve cycling on standard valves; making modifications of the product of any kind; failure to use caution in operating valves in
high temperature, high pressure, or highly hazardous services; and the failure to maintain valves as recommended. The right is reserved to change or modify product design or
construction without prior notice and without incurring any obligation to make such changes and modification on products previously or subsequently sold.