Flowserve PlugSeal User Manual
Page 11
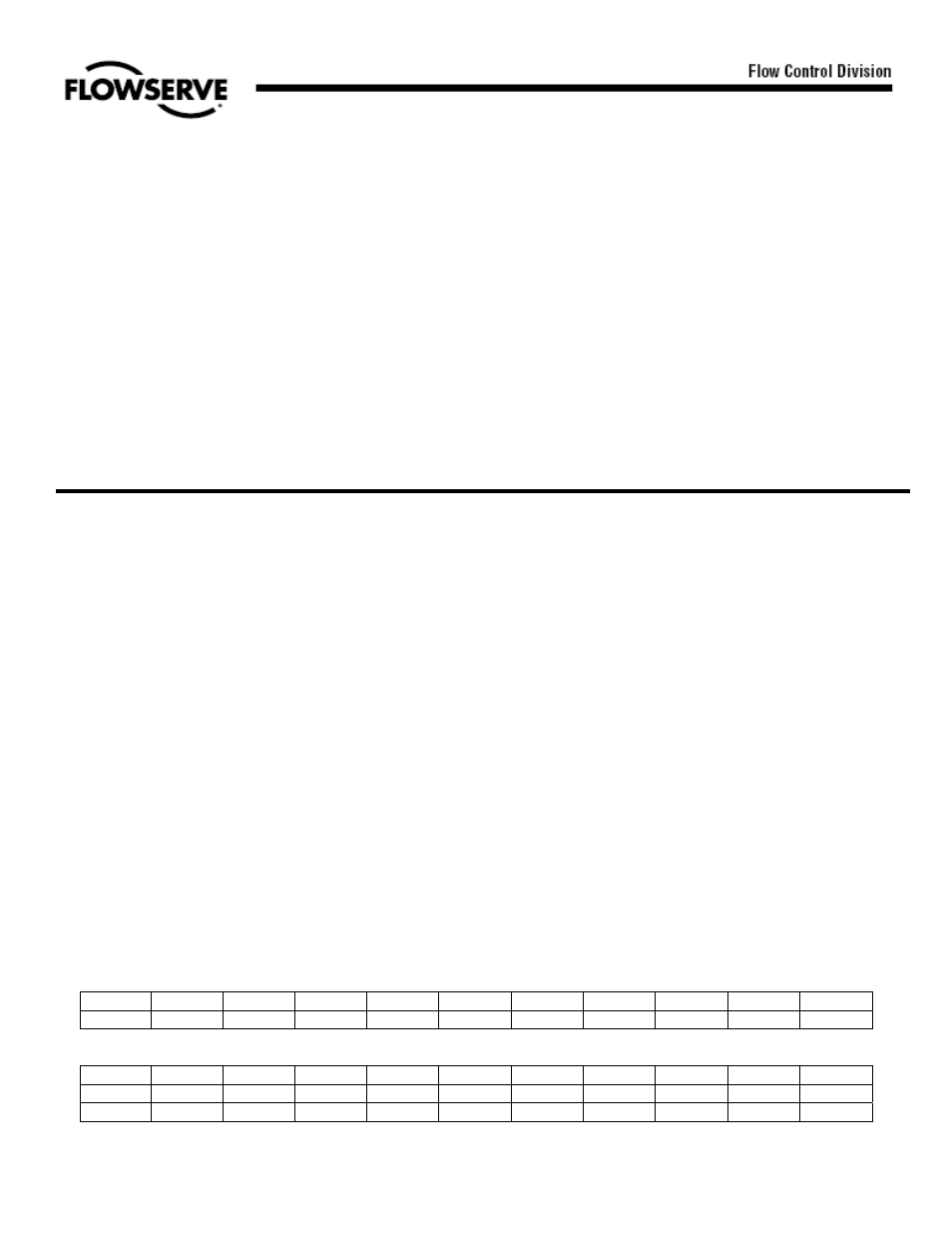
8
6. Turn plug (Part 4) in order to raise the plug to vent
any material trapped in the valve.
7. Once the plug has been turned, the adjuster
fasteners (Part 11) can be completely removed.
8. Gradually loosen but DO NOT REMOVE all of the
top cap fasteners (Part 10). Turn the plug until it is
loose from the body bore and all pressure has been
vented. (It may be necessary to use a mechanical
means to move the plug upwards.)
9. Remove the top cap fasteners and top cap (Part 9)
from the plug stem. Retain any identification tags for
attachment during re-assembly.
10. Remove the plug (Part 4) from the body (Part 1).
11. Remove the grounding spring (Part 8) and thrust
washer (Part 7) from the plug.
12. Remove the metal diaphragm (Part 6) and the PFA
diaphragm (Part 5) from the plug stem.
13. Inspect the plug for wear or damage, especially
scratches near the waterway on the sealing bands. If
wear or damage is excessive, the plug may require
replacement. Similarly, inspect the body bore for
wear or damage incurred by the process fluid.
Excessive scoring or erosion will reduce the valves
ability to seal.
14. Thoroughly clean all valve parts with an acceptable
cleaner.
15.
Inspect parts for damage. Look for marred,
scratched, or rough sealing surfaces on the valve
plug or machined body bore. NOTE: Reinstallation
of damaged or unclean parts will ruin any
replacement seals installed into the valve. Plugs will
need to be replaced when leakage rates exceed
tolerable levels due to PFA erosion or wear. Bodies
must maintain an RMS 16 surface finish for proper
operation.
SECTION VI.
VALVE ASSEMBLY
NOTE: Part number reference is shown in Figure 1.
1. Mount body (Part 1) in arbor press or table vise
holding one flange or supported in v-blocks near
the buttweld face. Ensure the body is
supported adequately to avoid movement while
assembling.
2. Assemble the PFA diaphragm (Part 5) over the
plug stem (Part 4) with the aid of a diaphragm
guide, Part series BY77543A (Figure V-A2). The
plug stem and diaphragm guide should be
checked for nicks before installing the
diaphragm. Nicks on these surfaces could result
in scratches on the lip of the diaphragm and
must be removed by polishing or replacement.
3. Place the metal diaphragm (Part 6) over the plug
stem with the raised center section up.
4. Place the thrust washer (Part 7) over the plug
stem.
5. Apply a thin film of lubricant to the plug and
place the assembled plug (complete with PFA
6. diaphragm, metal diaphragm and thrust washer),
in the open position into the body.
7. With the top cap on a table, thread the adjuster
fasteners into the top cap until the bottoms of
the fasteners are flush with the recessed
underside of the top cap.
8. Position the top cap (Part 9) over the plug
making sure the top cap is free to move
downward (Figure V-B3).
9. Place an H shaped support over the top of the
valve, resting on the top cap. Press the top cap
downward until the top cap is firmly seated in the
counterbore of the body.
10. Using all top cap fasteners (Part 10), tighten
evenly in a criss-cross method until the top cap
bottoms on the body counter bore.
Recommended top cap fastener torques are
shown in Table 4.
11. Tighten all adjuster fasteners in a criss-cross
pattern to the recommended torque in Table 5.
Table 4: Top Cap Fastener Torque
1 2 3 4 6 8 10
12
14
16
Ft-lbs 40 70 120 250 325 425 450 500 700
Table 5: Adjuster Fastener Torque
1 2 3 4 6 8 10
12
14
16
In-lbs
80
100
120
ft-lbs
20
40
50
* Torques are preproduction estimates and subject to change. Contact Factory for updated torques