Flowserve APEX 5000 Analog Feedback Options User Manual
Apex 5000 analog feedback options
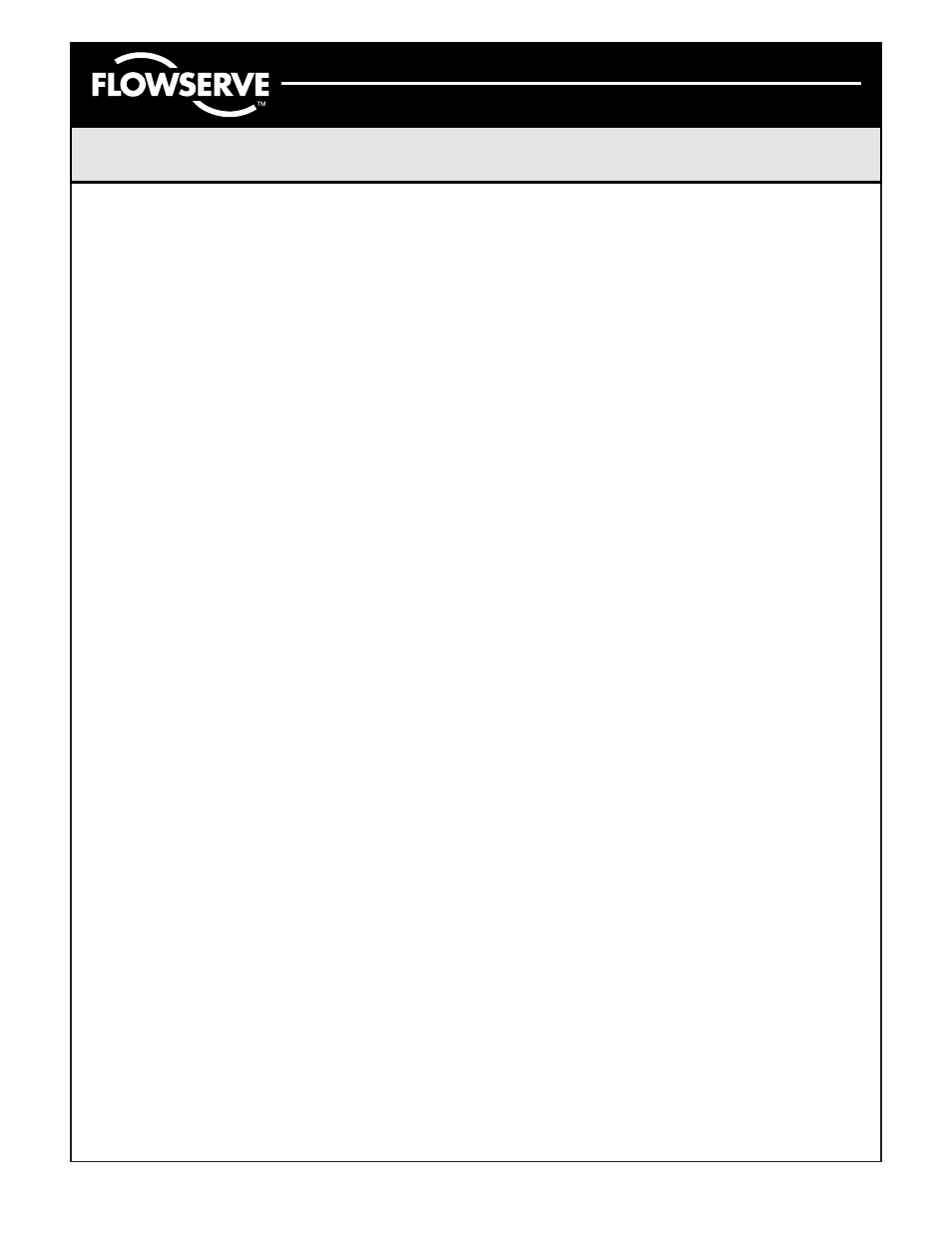
B00063-0 (AUTO-71) 4/00
Page: 1 of 4
© 2000, Flowserve Corporation, Provo, UT
Automax Valve Automation Systems
Installation, Operation and Maintenance Instructions
Introduction:
The Apex 5000 Modular Positioning System (AMPS) has
three options for internal analog feedback modules:
TYPE F
4-20 mA Current Transmitter
Voltage req’d: 6-30 Vdc
Input resistance: 750 ohms max @ 24 Vdc
Temp. Range: 32 to 158 deg. F
TYPE G
0-1K ohm Resistive
1 Watt max. load
TYPE H
0-10K ohm Resistive
1 Watt max. load
Each of these options is easily installed and adjusted
in the field with no housing modification required.
Components are mounted on a bracket and prewired to a
terminal strip. Resistive feedback modules use a 1% pre-
cision potentiometer operated by precision gears off of a
special positioner shaft. The 4-20 mA current transmitter
adds a current controller card. Factory installed units are
complete with minimum current or resistance set at the
full clockwise position. Field installation kits include (1)
feedback module, (1) positioner shaft (complete with
gearing), (2) replacement snap rings, and (2) feedback
module mounting screws.
Installation:
Caution: Be sure supply air pressure is removed and no
pressure exists in actuator before installation.
1. Remove positioner from actuator (it is not necessary
to remove air lines) and remove cover.
2. Remove positioner shaft snap ring on outside of
housing.
3. Push span arm away from shaft to remove pressure
on cam. Holding cam, remove cam/shaft assembly.
4. Install (1) snap ring on analog feedback shaft in
groove closest to gear.
5. Apply a light coat of lubricant (Lubriplate MAG-1
grease or equivalent) to shaft between grooves.
6. Push span arm out of the way and install shaft in
positioner. Make sure cam and shaft flats are properly
aligned (see “Mounting” and “Cam Installation” in
Positioner IOM B00062).
7. Install (1) snap ring in bottom shaft groove to secure
shaft in positioner.
8. Place feedback card in positioner, align holes and
fasten with (2) screws. Holes are slightly oversized
to allow for proper spacing (no backlash) between
potentiometer gear and positioner shaft gear.
9. Replace positioner on actuator. Note: Changing shaft
may affect positioner calibration. Check and recali-
brate positioner if necessary.
10. Remove conduit plug (use 3/8" Allen wrench) and
make electrical connections following applicable
electrical code requirements (refer to Figure 2 for
resistive feedback or Figure 3 for 4-20 mA transmitter
wiring diagram).
11. Calibrate (see “Calibration”).
12. Replace cover.
Special Requirements for Applications
Involving Weather or Periodic Hose-down:
The Apex 5000 positioner requires unrestricted exhaust.
A breather is provided in the housing bottom. If the posi-
tioner is mounted such that rain or hose-down fluid might
get inside through the breather, special preparation is
necessary. Water or other fluid ingression may short out
analog feedback module. Two options are available:
1. Plug breather port (using a 3/8" NPT pipe plug) and
allow the positioner to exhaust out through electrical
conduit. This requires that no conduit seals be used
and that the user provide means for exhaust air to
escape conduit.
2. Pipe a suitable breather line to the breather port.
Avoid the use of loops or other configurations that
might trap fluid or otherwise restrict exhaust flow and
affect positioner performance. Use a simple vertical
line six to twelve inches long with output towards the
ground (see Figure 1).
APEX 5000 Analog Feedback Options
Flowserve Corporation
765 South 100 East
Phone: 801 373 3028
Flow Control Division
Provo, Utah 84606
Facsimile: 801 489 2228
www.flowserve.com
Email: [email protected]