ONICON F-5100 Insertion User Manual
Page 30
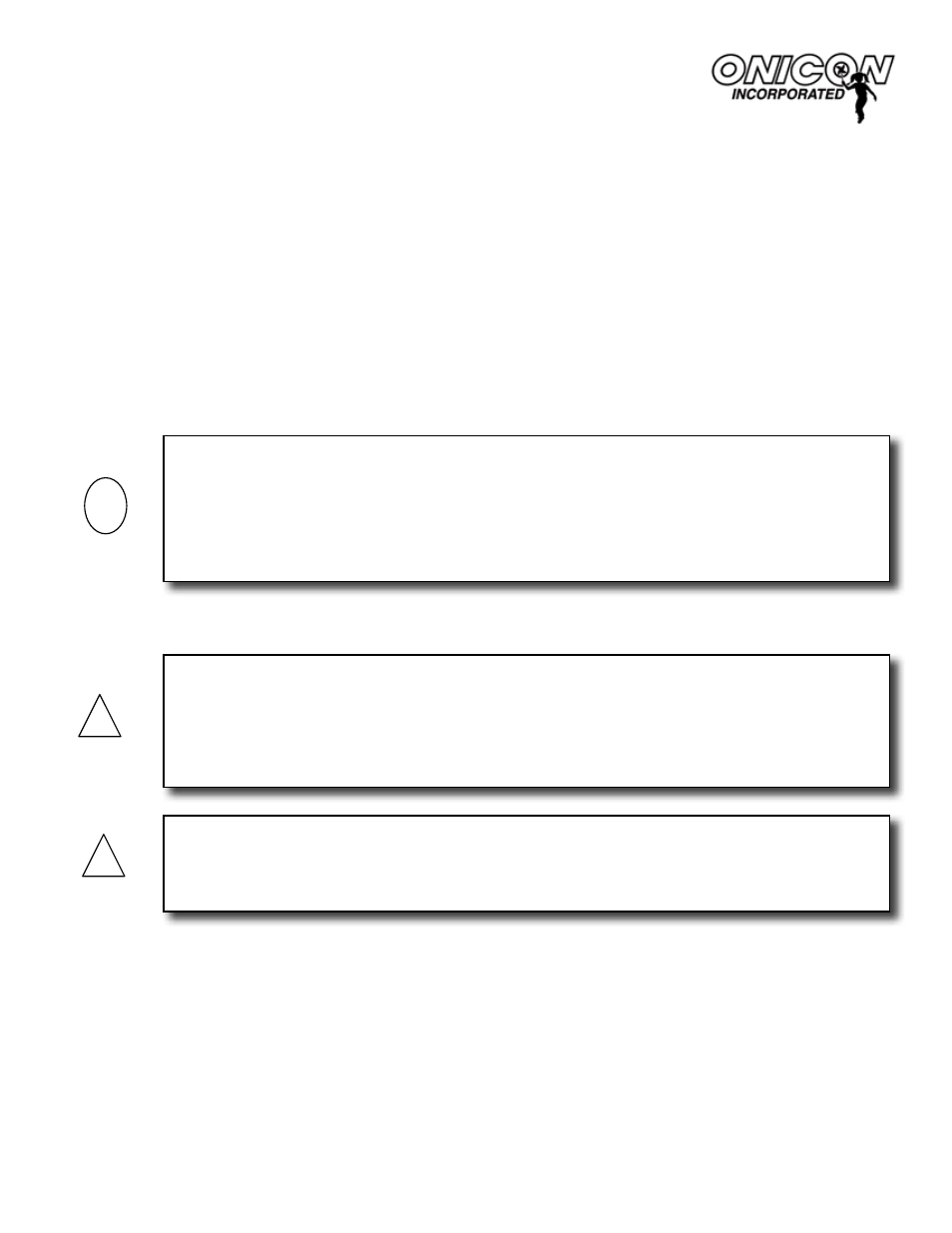
11451 Belcher Road South, Largo, FL 33773 • USA • Tel +1 (727) 447-6140 • Fax (727) 442-5699 • [email protected]
F-5100 Insertion Thermal Mass Flow Meter Manual 05/15 - 0663-20 / 18333
Page A-3
ZERO FLOW CALIBRATION TEST
The zero flow calibration test provides a simple, yet effective, method for periodic field validation of
the factory calibration. Prior to shipment to the customer, each ONICON F-5000 series flow sensor
undergoes a multipoint calibration. In this process, signal levels are recorded at a series of known
velocities over the specified operating range. The last data point taken in this process is taken at zero
flow (zero velocity). The value recorded at zero flow is part of the calibration record provided with the
sensor and is stamped on the sensor nameplate. By utilizing the mW output displayed by the sensor, it
is possible to duplicate the factory no flow condition (zero velocity) test in the field.
Successfully duplicating this test provides field validation of the current calibration. A successful
zero flow test confirms that the flow sensor circuitry operating characteristics have not changed and
validates that the zero velocity data point has not shifted or drifted. It also verifies that the sensor
assembly is clean and undamaged and does not require visual inspection. It essentially provides a
means to validate that the sensor is operating properly and can be used as part of a quality assurance/
preventative maintenance program or in lieu of scheduled annual factory calibrations.
IMPORTANT NOTE
The original factory zero flow calibration was performed with a vertically oriented sensor installed
through a valve located on the top of a horizontal test pipe. If the sensor is installed in a different
orientation the output at zero flow will be slightly different.
Depending on the orientation, sensors inserted horizontally into a pipe may increase the reading
by as much as 5-6 mW.
i
There are 3 ways to validate the sensor’s zero flow calibration.
WARNING
SYSTEM MAY BE UNDER HIGH PRESSURE. When removing the flow sensor, be sure to grasp
the electronics enclosure firmly by hand before slowly loosening the compression fitting. Failure
to do this will allow the pressure in the pipe to suddenly and rapidly force the sensor from the
pipe causing serious injury. The hand effort required to hold the sensor will be 0.2 times the pipe
pressure.
!
!
WARNING
Do not attempt to remove the sensor from a pipe pressurized to greater than 250 PSIG. For pipes
pressurized above 250 PSIG isolate flow and relieve pressure in the pipe before attempting to
remove the sensor.
Method 1
1. Close valves in the process supply line to stop all flow in the pipe where the sensor is located.
2. Wait up to 2 – 3 minutes to allow the sensor reading to stabilize at zero and note the mW
reading on the display.
3. Compare the reading to that stamped on the nameplate. The two readings should agree within ± 5mW.