Theory of operation – Daktronics E SERIES User Manual
Page 9
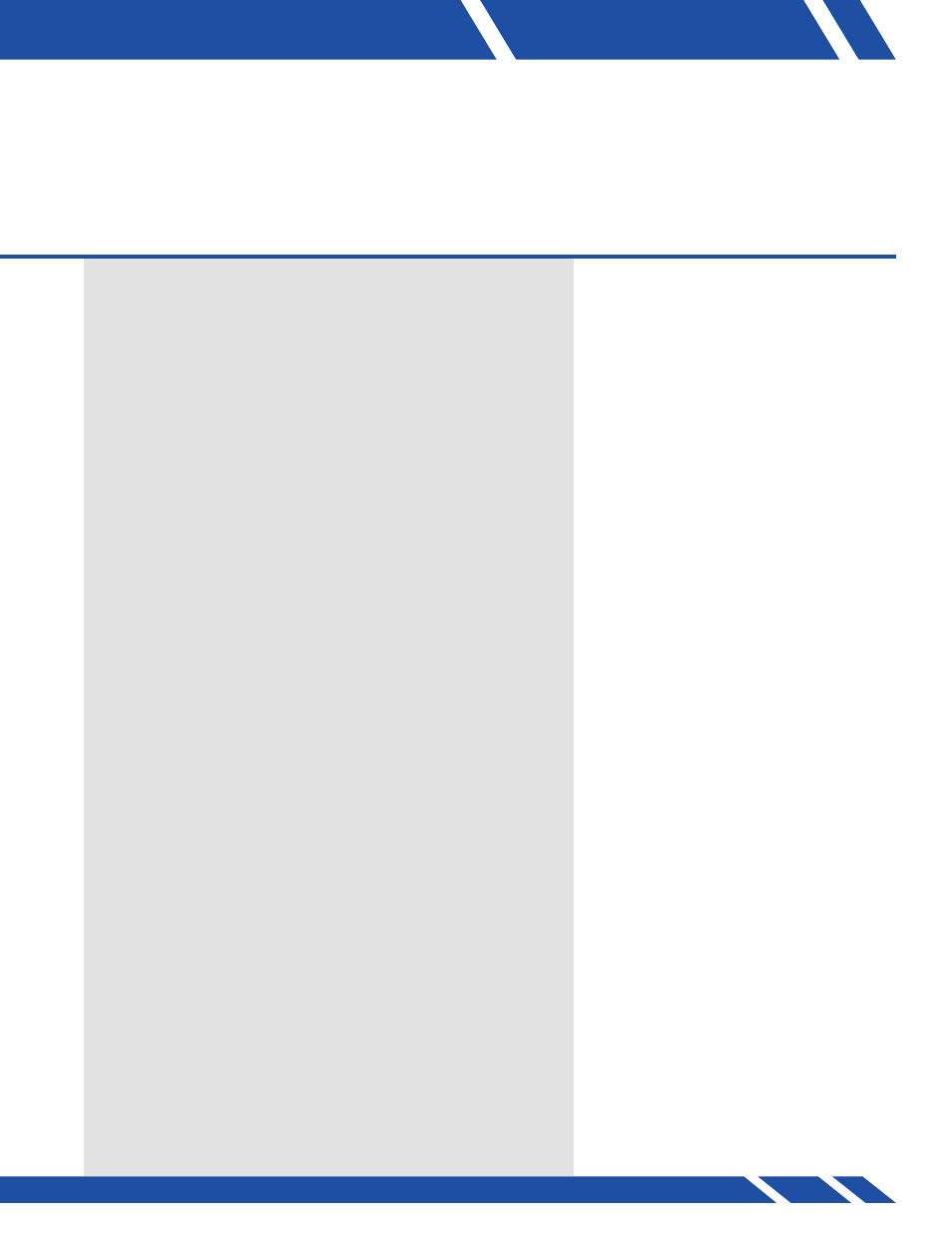
Each Vortek
®
hoist is connected to the main high voltage power buss through a safety twist-locking plug. This plug
brings in the main 3-phase power that is connected to the motor drive and motor brake located in each hoist
assembly. Also connected to each hoist assembly through safety locking connectors are 24 V DC power, E-Stop
circuit and a computer network cable.
The motor drive controls all movements of the hoist. Each drive on each hoist contains programming to identify it
to the network. This programming also includes but is not limited to maximum speed, acceleration and gear ratios.
Each motor drive monitors an incremental encoder and emergency stop status. The incremental encoder is used for
position control. The emergency stop status is used to detect the operation of the emergency stop system.
Monitoring of each hoist is done over the network using the master program running in the Human Machine
Interface (HMI). The HMI is typically located at stage level inside the master control cabinet. Inside the master
control cabinet is the HMI and the I/O module. A 24 V DC power supply that powers the I/O module and the
E-stop circuit is also located in the master control cabinet.
The HMI is a touch screen based PLC control system developed by Emerson’s Control Techniques. The PLC program
running inside the HMI allows the operator to operate any hoist connected to the system. The HMI is connected
directly to each hoist motor drive through a series of adapters forming a MODBUS driven token ring topology
network, as well as connected to the I/O module to allow the use of a remote pendant and manage the e-stop
circuit. During operation of the HMI, data is transmitted through the MODBUS network from the HMI to the selected
hoist motor drive. Likewise, data is received back through the MODBUS network to the HMI to relay encoder
information and load sensing information. The 24 V DC E-stop circuit is also connected to the E-stop button located
next to the HMI on the front of the master control cabinet.
Communication with the hoists is also possible using Ethernet protocol; however, in order for this type of
communication to be possible, the hoists must have an Ethernet module installed and the HMI configured and
wired properly to run the protocol. Ethernet switches are also necessary when using this type of communication
and would be installed in the low voltage wireways.
03
THEORY OF OPERATION
THEORY OF OPERATION
7