8 examination of parts, 9 assembly, 0 auxiliaries 7.1 seal and seal systems – Flowserve MSP User Manual
Page 25
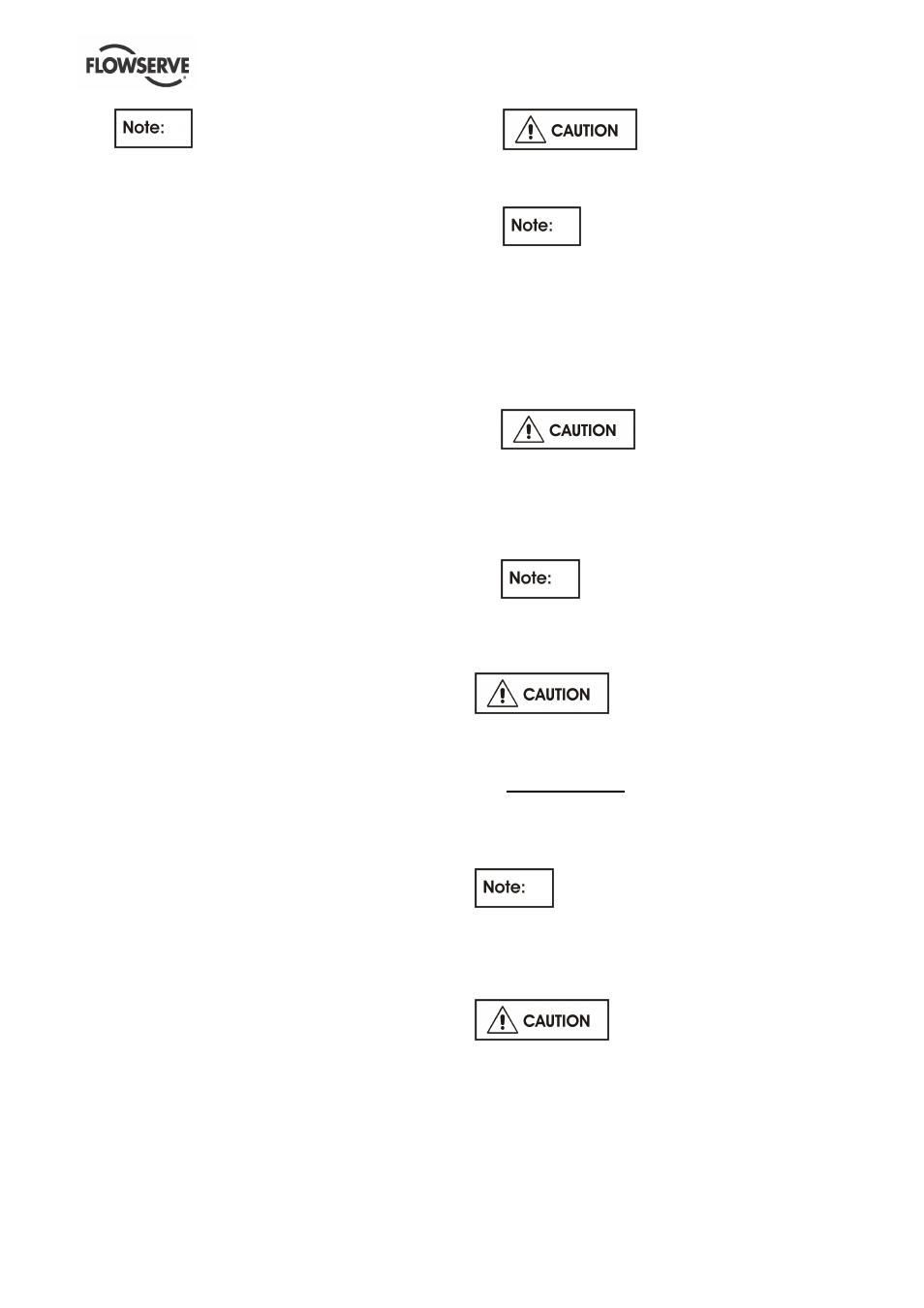
MSP USER INSTRUCTIONS ENGLISH - 07/14
Page 25 of 35
Pump shaft [2100] shall be pulled off
only if required (see chapter 6.8) to keep axial
clearance of impeller.
6.8 Examination of parts
1) Pumps with semi open impeller have no wear
rings. Check the wear plate and the impeller
[2200] against any wear. Semi open and free flow
impellers have back vanes, which shall be
checked against any wear.
2) Check all parts against corrosion and erosion.
3) Carefully check the coupling against any wear.
4) Rotate the angular contact bearing by hand, to
check against abnormal sound. Check the
bearing cages against any wear and the outer
and inner race against running marks. Check the
runout of the shafts. TIR (Total Indicated Runout)
shall not exceed 0.04 mm/m (0.0005 in./ft) of
length. TIR shall not exceed 0.08 mm (0.003 in.)
over total shaft length.
5) Check the bearing sleeve [3400] and bearing
bushing [3300]. The diametrical clearance shall
not exceed 0.8 mm (0.03 in.).
6.9 Assembly
To assemble the pump consult the sectional
drawings.
Ensure threads, gasket and O-ring mating faces are
clean. Apply thread sealant to non-face sealing pipe
thread fittings.
6.9.1 Assembly of pump – 1 stage, 2 stage
If the pump shaft [2100] has not been pulled off, use
reverse disassembly procedure.
6.9.2 Assembly of the hydraulic cartridge
This procedure shall be used, if the pump shaft
[2100] has been pulled off.
1) Mount the mechanical seal into the casing cover
[1221]. Tight hex nuts [6581.3] of studs [6572.3].
2) Insert carefully the pump shaft [2100] into the
shaft seal assembly and install the tool into the
foreseen shaft nut. Move the hydraulic assembly
upwards until the tool touches the pump casing
cover [1221]. Now the shaft needs to be fixed in
this position by locking the clamping ring [2542].
3) Put the clamping ring [2542] to the pump shaft
[2100] and slide the hydraulic cartridge consisting
of mechanical seal, pump shaft [2100] and casing
cover [1221] to the motor shaft.
4) Fix the hydraulic cartridge with the socket head
cap screws [6579.3] to the bearing lantern [3140].
Now the pump shaft [2100] has reached its
correct axial position.
5) Tight the clamping unit crosswise with the
required torque of 7 Nm (5.2 lbf.ft)
The clamping surfaces must
be absolutely grease free.
6) Open the socket head cap screws and remove
the tool .
Store the tools outside the pump for
better use.
7) Insert the O-ring [4610.2] and slip on the liner
[1649] to the casing cover [1221]. Tight the
socket head cap screws [6579.2].
8) Put in the key [6700] and slip on the 2
nd
stage
impeller [2200]. Now put on the liner [1649] and
push in the interstage plate [1471]. Fix the
interstage plate [1471] with socket head cap
screws [6579.1].
Insert O-ring [4610.1] into the
interstage plate [1471].
9) Slip on the bearing sleeve [3400] and the first
stage impeller [2200] and the lockwasher
[6541].Tight the assembly with the impeller nut
[2912] (right hand thread) and secure it with the
lockwasher [6541].
If the pump is equipped with an
inducer [2215] replaces the shaft nut.
10) Now the complete motor hydraulic assembly can
be put into the pump casing [1110]. Tight hex
nuts [6581.2] of the studs [6572.2].
Take care of the cylindrical pin
[6811] to ensure correct position of the motor
hydraulic assembly in the casing.
7.0 AUXILIARIES
7.1 Seal and seal systems
7.1.1 Single Mechanical Seal with API – Plan 01
Refer to mechanical seal drawing and
auxiliary piping drawing.
The pump is equipped with a single mechanical seal.
The cartridge design allows to change the
mechanical seal without taking it apart.
Try to turn the rotor by hand.If the
rotor cannot be turned, the pump must be
disassembled, refer to section 6.7.1 Dismantling
MSP.
Actions after start up:
Check all connections to the seal gland and the
mechanical seal itself against leakage. It is usual that
at the seal faces a small leakage occurs after start