Flowserve MSP User Manual
Page 27
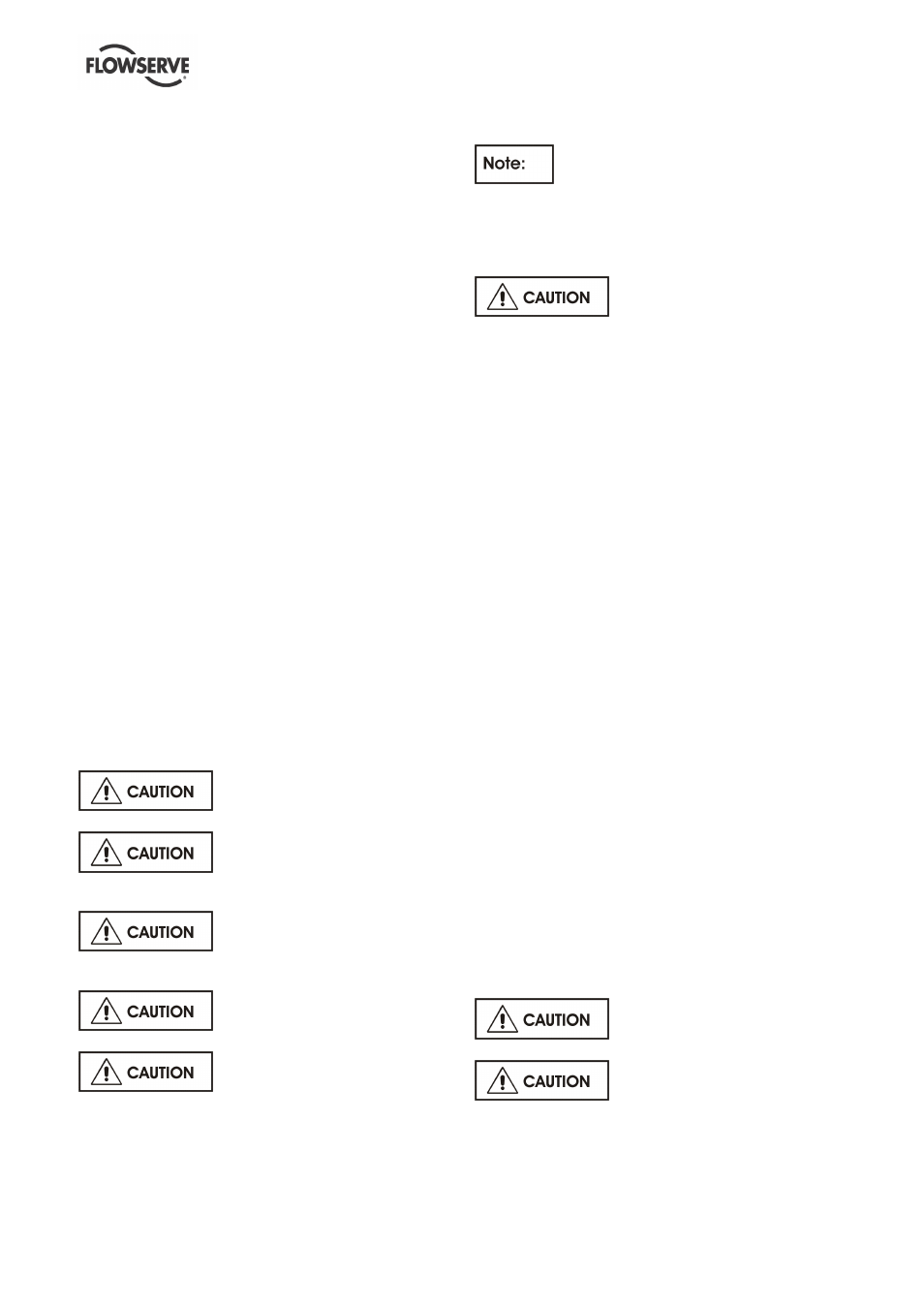
MSP USER INSTRUCTIONS ENGLISH - 07/14
Page 27 of 35
disassembled, refer to section 6.7.1 Dismantling
MSP.
The mechanical seal requires no adjustment
anymore. Check if the mounting plates are already
swung out.
Actions after start up:
Check all connections to the seal gland and the
mechanical seal itself against leakage. Check the
temperature of the seal gland. I slight increase of
temperature may be observed during the run in
period.
The faces of the inner mechanical seal are flushed by
the product (API Plan01). In Plan 01, product is
routed from the pump discharge via an internal port to
the seal chamber to provide cooling for the seal and
to vent air or vapors from the seal chamber. Fluid
then flows from the seal cavity back into the process
stream. Between the inner mechanical seal and the
outer (atmospheric) mechanical seal is a liquid buffer
fluid, which is unpressurized (API Plan 52). The
buffer fluid is contained in a seal pot (refer to drawing
of the seal pot), which is vented to a vent system,
thus maintaining the buffer fluid pressure close to
atmospheric.
Inner seal leakage will be product leakage into the
buffer fluid. There will always be some leakage
(max.5 ml/hour).
Plan 52 is used for flashing liquids, which have a
vapour pressure higher then the buffer fluid pressure.
So the product will flash in the seal pot and the
vapour can escape to the vent system.
All screw / flange connections have to be proofed.
Straight screw joints made of stainless steel have to be
tightened especially carefully.
Fill the seal system with a suitable
buffer fluid (refer to lubrication table).
Ensure that the valve GV for the
connection V is open (Barrier/buffer fluid vessel
drawing).
Open the Block & Bleed valve to
allow proper function of the PSH (set point 0.5 bar
(7.25 psi) above flare pressure).
Open all necessary valves in the
cooling and auxiliary piping and check the flow.
Disassembly of the seal cartridge
is only allowed by authorized personal. Contact
Flowserve for any service of the mechanical seal. We
recommend to have a spare cartridge seal on stock
for easy replacement.
7.1.5 Dual Mechanical Seal unpressurized with
API–Plan 11+52
Refer to mechanical seal drawing and
auxiliary piping drawing.
The pump is equipped with a dual mechanical seal.
The cartridge design allows to change the
mechanical seal without taking it apart.
Try to turn the rotor by hand.If the
rotor cannot be turned, the pump must be
disassembled, refer to section 6.7.1 Dismantling
MSP.
The mechanical seal requires no adjustment
anymore. Check if the mounting plates are already
swung out.
Actions after start up:
Check all connections to the seal gland and the
mechanical seal itself against leakage. Check the
temperature of the seal gland. I slight increase of
temperature may be observed during the run in
period.
The faces of the inner mechanical seal are flushed by
the product (API Plan11). In Plan 11, product is
routed from the pump discharge via an orifice to the
seal chamber to provide cooling for the seal and to
vent air or vapors from the seal chamber. Fluid then
flows from the seal cavity back into the process
stream. Between the inner mechanical seal and the
outer (atmospheric) mechanical seal is a liquid buffer
fluid, which is unpressurized (API Plan 52). The
buffer fluid is contained in a seal pot (refer to drawing
of the seal pot), which is vented to a vent system,
thus maintaining the buffer fluid pressure close to
atmospheric.
Inner seal leakage will be product leakage into the
buffer fluid. There will always be some leakage
(max.5 ml/hour).
Plan 52 is used for flashing liquids, which have a
vapour pressure higher then the buffer fluid pressure.
So the product will flash in the seal pot and the
vapour can escape to the vent system.
All screw / flange connections have to be proofed.
Straight screw joints made of stainless steel have to be
tightened especially carefully.
Fill the seal system with a suitable
buffer fluid (refer to lubrication table).
Ensure that the valve GV for the
connection V is open (Barrier/buffer fluid vessel
drawing).