0 auxiliaries 7.1 seal and seal systems – Flowserve HWX Worthington User Manual
Page 32
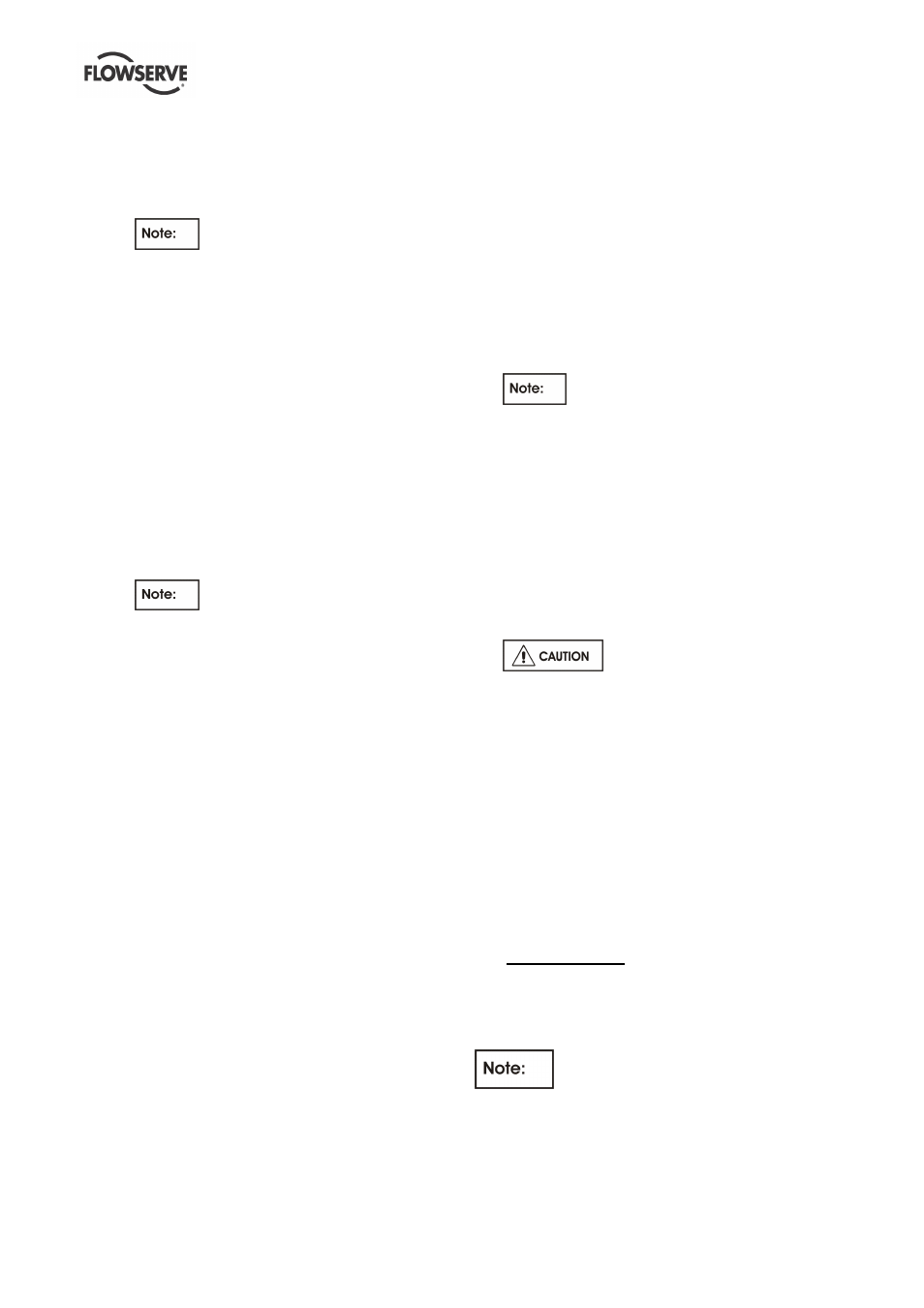
HWX USER INSTRUCTIONS ENGLISH - 07/14
Page 32 of 40
If you disassemble bearing housing,
reassemble it in accordance with the
procedure outlined above
•
Remove the dial indicator.
•
Install the impeller key [6700.1] and impeller
[2200].
As you face the impeller end of the
shaft, thread the impeller cap screw by
turning it counter-clockwise.
•
Remove the dial indicator.
•
Install impeller washer [2430] and impeller
lock washer against impeller [2200] and
screw impeller cap screw [2912] tightly
against washer, but do not bend a lock
washer tab. The impeller must be tight
against the shaft shoulder with no play.
•
Fix dial indicator to bearing housing register
face or another point so that it is rigid and
touch indicator button to either wear ring
[2300.1 – 2300.2].
•
Slowly, rotate shaft and record readings at
12, 3, 6, and 9 o'clock points; TIR shall not
exceed 0.04 mm (0.0015 in).
•
Repeat the two steps above to verify
concentricity of other wear ring.
If runout is excessive, check fit of
impeller on shaft (see Section 6.9.2) and
wear ring installations (see Section 6.9.1).
Should you be unable to determine the cause
of excessive runout, contact the nearest
FLOWSERVE Pump Sales Office.
•
Remove impeller cap screw [2912], impeller
lock washer, impeller washer, and impeller
[2200].
6.8.5 Shaft seal
6.8.5.1 Shaft seal – mechanical seal
a) Install, mechanical seal, and seal plate nuts.
Tighten nuts evenly, then turn casing cover [1221]
over, placing impeller-side up.
b) Use heat, if necessary, on impeller and slide it
over key [6700.1] and against shaft shoulder.
c) Secure shaft [2100] so that it will not move.
d) Install impeller washer and impeller lock washer
against impeller and tightly screw impeller cap
screw [2912] against washer to hold impeller on
shaft without any play. Bend a tab of the lock
washer against a face of the cap screw to secure
it in place.
e) Rotate the mechanical seal setting washers which
hold the shaft sleeve to the seal plate out of the
way and secure them for future use.
f) Heat half-coupling in dry heat convection oven to
300°F (149°C). Install the coupling key [6700.4]
on shaft, then slide the half-coupling onto the
shaft until it is positioned as shown by the Outline
Drawing.
g) Wrap soft cables or nylon lifting strap around
casing cover [1221] and bearing housing [3200],
then raise pullout element and transport it to
pump casing [1110].
Refer to any special instructions supplied with
the mechanical seal.
6.8.6 Pullout Element Installation
a) Install a new casing cover gasket [4590] in the
casing [1110].
b) Attach the pullout element lifting tool to the pullout
element, then install rigging gear to lift the
element.
Ensure that the pullout element is
properly aligned with the casing and auxiliary
equipment in accordance with the Outline
Drawing.
c) Raise the pullout element upward until the
impeller clears the lower flange of the bearing
lantern [3140] and install through the large
opening in the support head.
d) Install the hex bolts clamping the casing cover
[1221] to the casing [1110]. Torque the bolts
evenly in a star pattern to the torque value
specified on Section 6.5.
e) Turn shaft by hand to ensure that rotor turns
freely without binding or rubbing.
Use of odd size bolts and nuts
to couple half-couplings and spacer will cause
imbalance; use only bolts and nuts specified
by the coupling manufacturer.
f) Install coupling spacer in accordance with the
manufacturer’s instructions in the back of this
manual.
g) Install all seal piping, related instrumentation, and
electrical equipment that was removed prior to
disassembly.
h) Perform an alignment check of the pump in
accordance with Section 4.5, “Initial Alignment”
Ensure that bearing lubrication is provided prior to
operating the pump in accordance with Section 5.2,
“Pump Lubricants”.
7.0 AUXILIARIES
7.1 Seal and seal systems
7.1.1 Single Mechanical Seal with API–Plan 11+61
Refer to mechanical seal drawing and
auxiliary piping drawing.
The pump is equipped with a single mechanical seal.
The cartridge design allows to change the
mechanical seal without taking it apart.