5 valve maintenance, Mark 100 – Flowserve Valtek Mark 100 Control Valve User Manual
Page 5
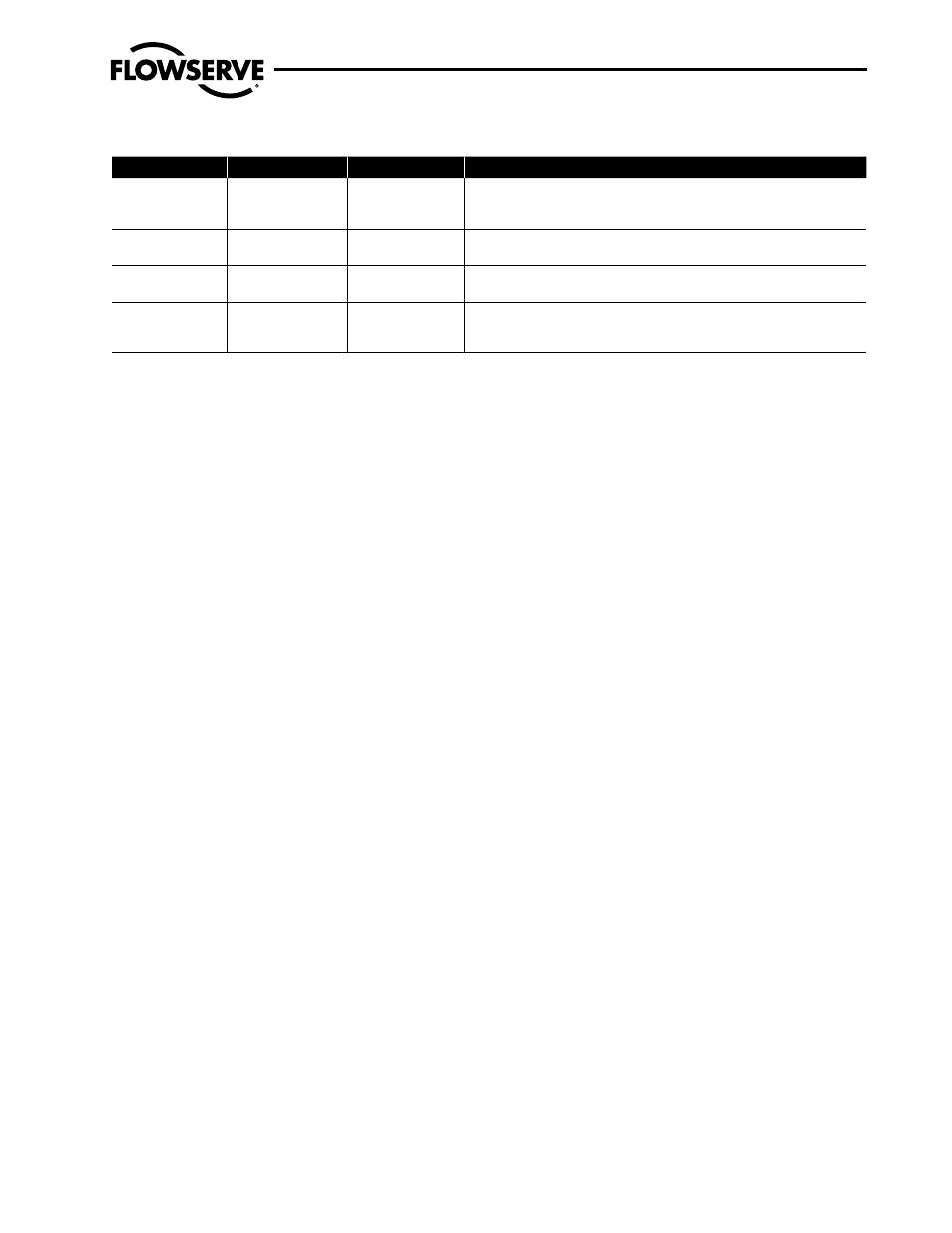
Flow Control Division
Mark 100
FCD FCAIM0100-02
Mark 100 Installation, Operation and Maintenance Instructions
5
Table 3: Common Packing Lubricants
Lubricant
Manufacturer
Temperature Range
Applications, Description
Krytox 206
E.I. DuPont
-5° to 550°F
-20° to 285°C
Fluorinated general purpose grease; handles common liquids and gases; good
lubricity in harsh mediums; nonflammable, chemically inert; will not harm plastic
or metal parts
GP 460
Graphite Products Co. 32° to 1000°F
0° to 540°C
Graphite in petrolatum; high pressures; anti-galling, graphite remains above
600°F / 316°C
Aeroshell Grease 7
Shell Oil Co.
-100° to 300°F
-75° to 150°C
Synthetic oil-based; low-temperature applications
Garlock Luball
Garlock Inc.
32° to 500°F
0° to 260°C
General purpose molybdenum disulfide lubricant economical; good in water,
steam and common chemicals; not good in harsh mediums where Krytox 206 is
recommended
5 Valve Maintenance
At least once every six months, check for proper operation by fol-
lowing the preventative maintenance steps outlined below. These
steps can be performed while the valve is in-line and, in some cases,
without interrupting service. If an internal problem is suspected,
refer to the “Valve Disassembly and Reassembly” section.
1. Look for signs of gasket leakage through the end flanges and
bonnet. Retorque flange and bonnet bolting (if required). See
Table 2.
2. Check for fluid leakage to the atmosphere through the body
drain plug, if applicable.
3. Examine the valve for damage caused by corrosive fumes or
process drippings.
4. Clean valve and repaint areas of severe oxidation.
5. Check packing box bolting for proper tightness. Refer to the
packing installation manual for specific details on maintaining
the style of packing supplied.
a
CAUTION: Do not overtighten packing. This can cause
excessive packing wear and high stem friction that may
impede stem movement.
6. If the valve is supplied with a lubricator fitting, check lubricant
supply and add lubricant if necessary. See Table 3 for common
lubricants.
7. If possible, stroke the valve and check for smooth, full-stroke
operation. Unsteady stem movement could indicate an internal
valve problem.
NOTE: Due to excessive friction, graphite packing can cause the
plug stem to move in a jerky fashion.
c
WARNING: Keep hands, hair and clothing away from all
moving parts when operating the valve. Failure to do so
can cause serious injury.
8. Make sure positioner linkage and stem clamp are securely fas-
tened. If the stem clamp is loose, check plug thread engagement
(refer to the “Reassembling the Actuator” section for the correct
procedure on aligning the plug with the seat.) Tighten stem
clamp nut.
9. Ensure all accessories, brackets and bolting are securely fas-
tened.
10. If possible, remove air supply and observe actuator for correct
fail-safe action.
11. Check rubber actuator bellows for splits, cuts or wear.
12. Spray a soap solution around the cylinder actuator retaining
ring, adjusting screw and actuator stem guide to check for air
leaks through the O-rings.
13. Clean any dirt and other foreign material from the plug stem.
14. If an air filter is supplied, check and replace cartridge if
necessary.