Maintenance – Paslode F350-S PowerMaster Plus 30 Framing Nailer User Manual
Page 12
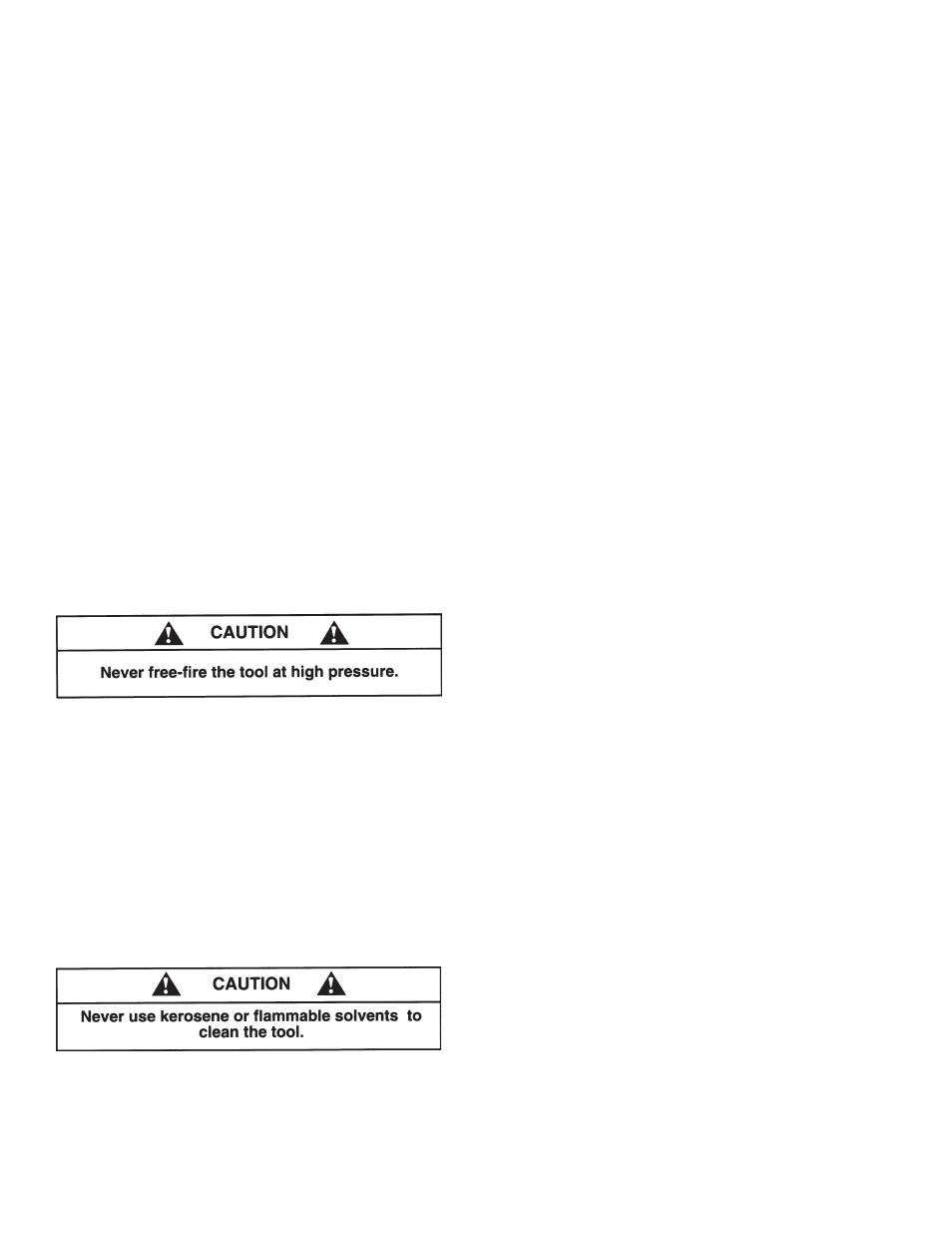
MAINTENANCE
Paslode
®
tools are built for ease of maintenance. A few
simple details will assure trouble-free operation and long
tool life. Anyone who uses or maintains the tool must read
the safety and maintenance instructions. Study the sche-
matic drawing before starting any repairs on the tool.
Air-operated tools must be inspected periodically, and
worn or broken parts must be replaced to keep the tool op-
erating safely and efficiently. Also the items on the mainte-
nance chart must be checked often.
Cold Weather Care
When temperatures are below freezing, tools should be
kept warm by any convenient, safe method. If this is not
possible, the following procedure should be used to warm
up the tools.
❑
Reduce the regulated air pressure to 30 psi.
❑
Remove all fasteners from the tool.
❑
Collect an air line and blank fire the tool. The reduced
air pressure will be enough to free-fire the tool. Slow
speed operation tends to warm up the moving parts. Slow-
ing up the piston helps the bumper and the O-rings to
become springy.
❑
Once the tool is warmed up, readjust the regulator to
the proper working pressure and reload the tool.
❑
Tool operators working outdoors or in unheated areas
in extremely cold temperatures should also:
Use Paslode pneumatic oil with antifreeze in the
lubricator, Part No. 219090 (8oz.)
Once a week, depending on the amount of tool
use, take the tool apart and wash away any
sludge with degreaser cleaner (Paslode Part No.
219086) to keep the tool operating efficiently.
Cleaning the air-operated tools with solvents removes the
thin coating of grease applied to the cylinder wall and
O-rings at the factory. To replace this coating of grease,
use Chemplex grease (Paslode Part No. 403734).
❑
Open the drain on the air compressor tank to drain any
moisture at least daily in extremely cold or humid weather.
A few ounces of anti-freeze in the tank will keep the air free
of frost.
Testing the Tool After Servicing
After replacing any part or parts, it is important to check the
tool for proper operation. This ensures that the tool was
put together correctly, is safe to use, and will perform the
job properly.
❑
Ensure that all hardware is tight.
❑
Ensure that the work contacting element is installed
correctly in relation to the trigger, and that both parts move
freely.
❑
Ensure that the magazine is properly attached.
❑
Ensure that the required safety information on the tool
is legible.
❑
Use only Paslode approved fasteners in the tool, and
ensure that they are correct for the application.
❑
Ensure that a male air fitting is securely connected to
the tool.
❑
Test the tool by driving fasteners into a workpiece iden-
tical to the tool's application.
❑
Check the tool for air leaks during testing and for the
proper sequence of operation.
❑
Ensure that all fasteners are driven to the same depth
and that the crown of the fastener is flush with the work-
piece.
Tool Lubrication
It is most important that the tool be properly lubricated by
keeping the air line lubricator filled and correctly adjusted.
Without proper lubrication the tool will not work properly
and parts will wear prematurely.
Use the proper lubricant in the air line lubricator. The
lubricator should be of low air flow or changing air flow
type, and should be kept filled to the correct level. Use
only Paslode recommended lubricants. Substitutes may
harm the rubber compounds in the tools O-rings and other
rubber parts. Paslode Part No. 403720 is a pneumatic
lubricating oil specially made for pneumatic applications.
If a filter/regulator/lubricator is not installed on the air
system, air operated tools should be lubricated at least
once a day with 6 to 20 drops of oil, depending on the work
environment, directly through the male fitting in the tool
housing.
Most minor problems can be resolved quickly ans easily
using the maintenance table that follows. If problems per-
sist, contact your Paslode dealer for assistance.
10