Please note while programming – HEIDENHAIN TNC 320 (340 55x-05) Cycle programming User Manual
Page 232
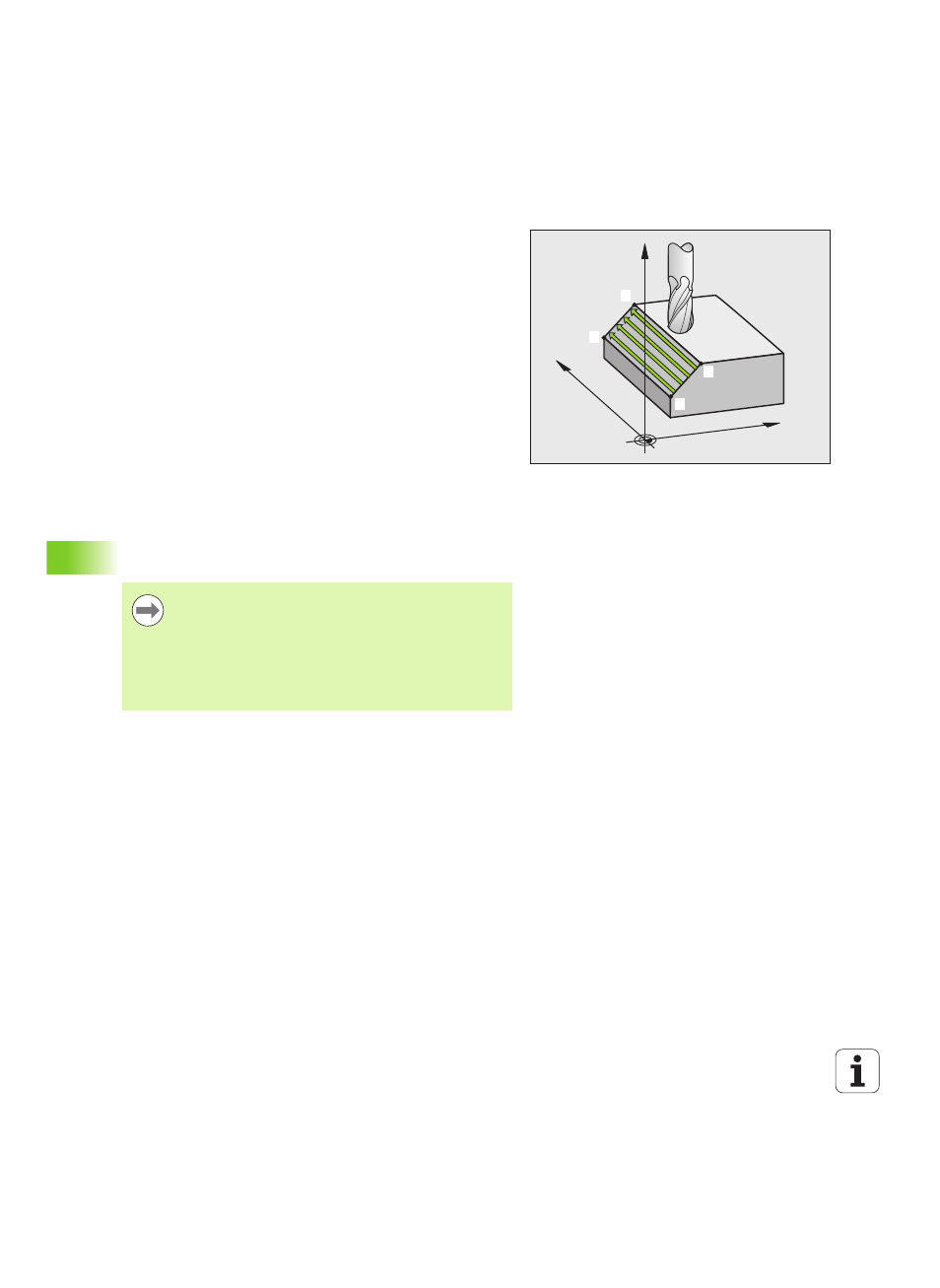
232
Fixed Cycles: Multipass Milling
1
0
.3 RULED SURF
A
C
E (Cy
c
le 231, DIN/ISO: G231)
Cutting motion
The starting point, and therefore the milling direction, is selectable
because the TNC always moves from point
1
to point
2
and in the total
movement from point
1
/
2
to point
3
/
4
. You can program point
1
at
any corner of the surface to be machined.
If you are using an end mill for the machining operation, you can
optimize the surface finish in the following ways:
A shaping cut (spindle axis coordinate of point
1
greater than
spindle-axis coordinate of point
2
) for slightly inclined surfaces.
A drawing cut (spindle axis coordinate of point
1
smaller than
spindle-axis coordinate of point
2
) for steep surfaces.
When milling twisted surfaces, program the main cutting direction
(from point
1
to point
2
) parallel to the direction of the steeper
inclination.
If you are using a spherical cutter for the machining operation, you can
optimize the surface finish in the following way:
When milling twisted surfaces, program the main cutting direction
(from point
1
to point
2
) perpendicular to the direction of the
steepest inclination.
Please note while programming:
X
Y
Z
1
4
3
2
From the current position, the TNC positions the tool in a
linear 3-D movement to the starting point
1
. Pre-position
the tool in such a way that no collision between tool and
fixtures can occur.
The TNC moves the tool with radius compensation R0 to
the programmed positions.
If required, use a center-cut end mill (ISO 1641).