Universal drilling (cycle 203) – HEIDENHAIN iTNC 530 (340 420) User Manual
Page 252
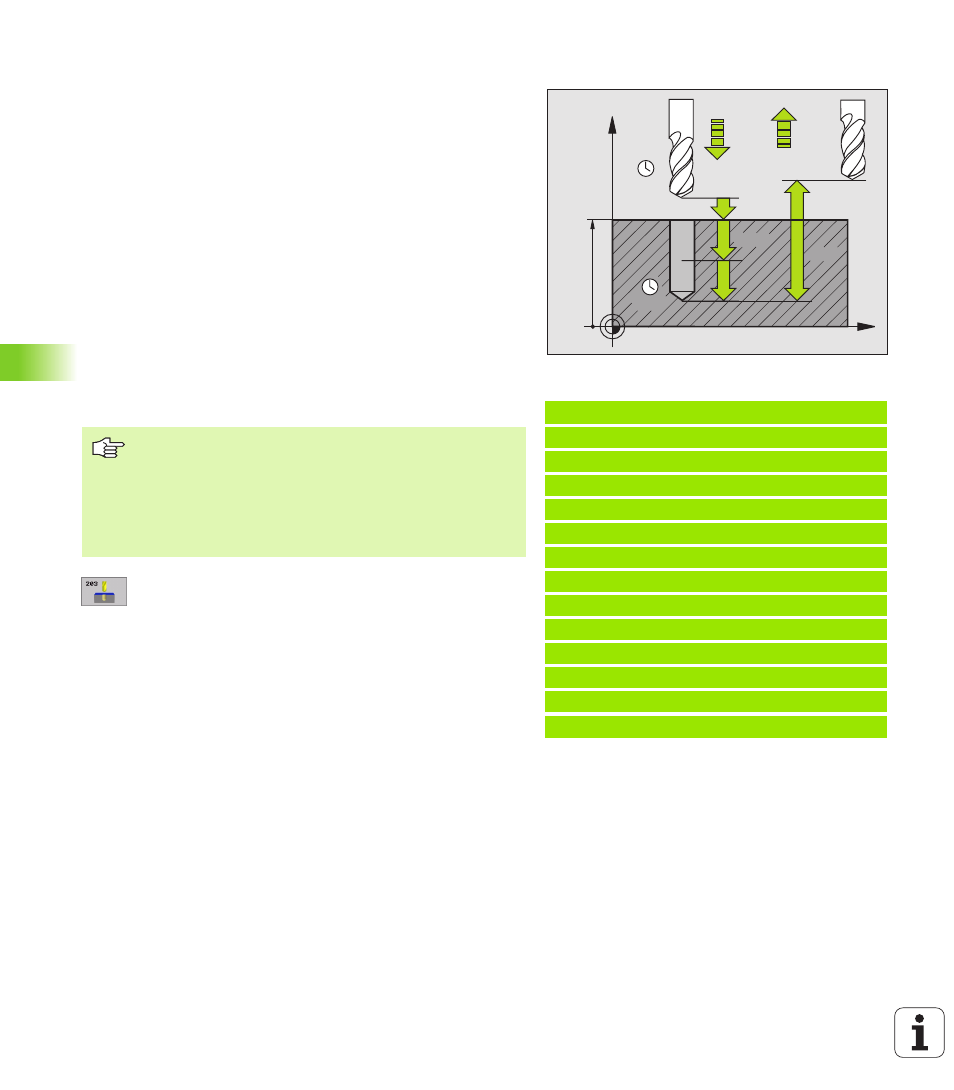
224
8 Programming: Cycles
8.3 Cy
cles f
o
r Dr
illing, T
a
pping and Thr
ead Milling
UNIVERSAL DRILLING (Cycle 203)
1
The TNC positions the tool in the tool axis at rapid traverse FMAX
to the programmed setup clearance above the workpiece surface.
2
The tool drills to the first plunging depth at the programmed feed
rate F.
3
If you have programmed chip breaking, the tool then retracts by
the entered retraction value. If you are working without chip
breaking, the tool retracts at the retraction feed rate to setup
clearance, remains there—if programmed—for the entered dwell
time, and advances again in FMAX to the setup clearance above
the first PLUNGING DEPTH.
4
The tool then advances with another infeed at the programmed
feed rate. If programmed, the plunging depth is decreased after
each infeed by the decrement.
5
The TNC repeats this process (2 to 4) until the programmed total
hole depth is reached.
6
The tool remains at the hole bottom—if programmed—for the
entered dwell time to cut free, and then retracts to set-up
clearance at the retraction feed rate. If programmed, the tool
moves to the 2nd set-up clearance with FMAX.
U
U
U
U
Set-up clearance
Q200 (incremental value): Distance
between tool tip and workpiece surface.
U
U
U
U
Depth
Q201 (incremental value): Distance between
workpiece surface and bottom of hole (tip of drill
taper)
U
U
U
U
Feed rate for plunging
Q206: Traversing speed of
the tool during drilling in mm/min
U
U
U
U
Plunging depth
Q202 (incremental value): Infeed per
cut. The depth does not have to be a multiple of the
plunging depth. The TNC will go to depth in one
movement if:
n
the plunging depth is equal to the depth
n
the plunging depth is greater than the depth
U
U
U
U
Dwell time at top
Q210: Time in seconds that the
tool remains at set-up clearance after having been
retracted from the hole for chip release.
U
U
U
U
Workpiece surface coordinate
Q203 (absolute
value): Coordinate of the workpiece surface.
Example: NC blocks
11 CYCL DEF 203 UNIVERSAL DRILLING
Q200=2
;SAFETY CLEARANCE
Q201=-20
;DEPTH
Q206=150
;FEED RATE FOR PLUNGING
Q202=5
;INFEED DEPTH
Q210=0
;DWELL TIME AT TOP
Q203=+20
;SURFACE COORDINATE
Q204=50
;2ND SAFETY CLEARANCE
Q212=0.2
;DECREMENT
Q213=3
;BREAKS
Q205=3
;MIN. INFEED DEPTH
Q211=0.25
;DWELL TIME AT DEPTH
Q208=500
;RETRACTION FEED RATE
Q256=0.2
;DIST. FOR CHIP BRKNG
X
Z
Q200
Q201
Q206
Q202
Q210
Q203
Q204
Q211
Q208
Before programming, note the following:
Program a positioning block for the starting point (hole
center) in the working plane with radius compensation R0.
The algebraic sign for the cycle parameter DEPTH
determines the working direction. If you program DEPTH
= 0, the cycle will not be executed.