Important – Yaskawa Sigma II Series Servo System User Manual
Page 255
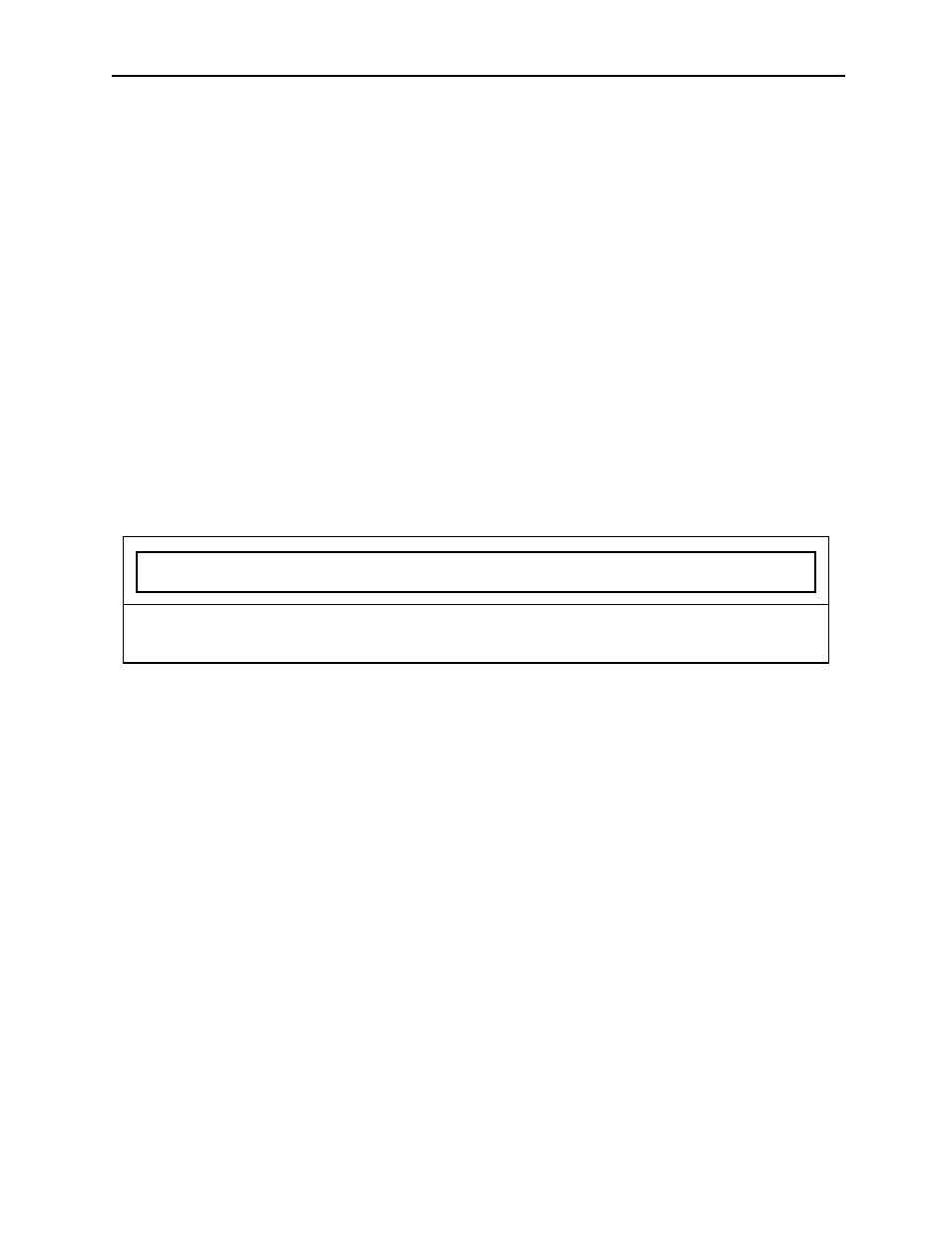
Sigma II User’s Manual
Chapter 6: Servo Adjustment
6 - 23
set these gains to the same numerical value.
3.
Repeat step 2 to increase the speed loop gain while watching the position error of
the analog monitor to observe the setting time and the torque reference of the
analog monitor to observe any occurrence of vibration. If there is any oscillating
noise or noticeable vibration, gradually increase the time constant of the torque
reference filter in Pn401.
4.
Gradually increase only the position loop gain. When it has been increased
about as far as possible, then decrease the speed feedback compensation in
Pn111 from 100% to 90%. Then repeat steps 2 and 3.
5.
Decrease the speed feedback compensation to a value lower than 90%. Then
repeat steps 2 through 4 to shorten the setting time. If the speed feedback com-
pensation is too low, however, the response waveform will vibrate.
6.
Find the condition in which the shortest setting time is obtainable within the
range where the position error or torque reference waveform observed through
the analog monitor is not vibrating or unstable.
7.
The servo gain adjustment is completed when no further shortening of the posi-
tioning time is possible.
• Speed feedback compensation usually makes it possible to increase the speed loop gain and position loop
gain. The machinery may vibrate excessively if the compensation value greatly changes or Pn110.1 is set to
“1” (i.e., speed feedback compensation disabled) after increasing the speed loop gain or position loop gain.
IMPORTANT