Fig.3, Fig.4, Maintenance – Sealey SAC05030 User Manual
Page 3
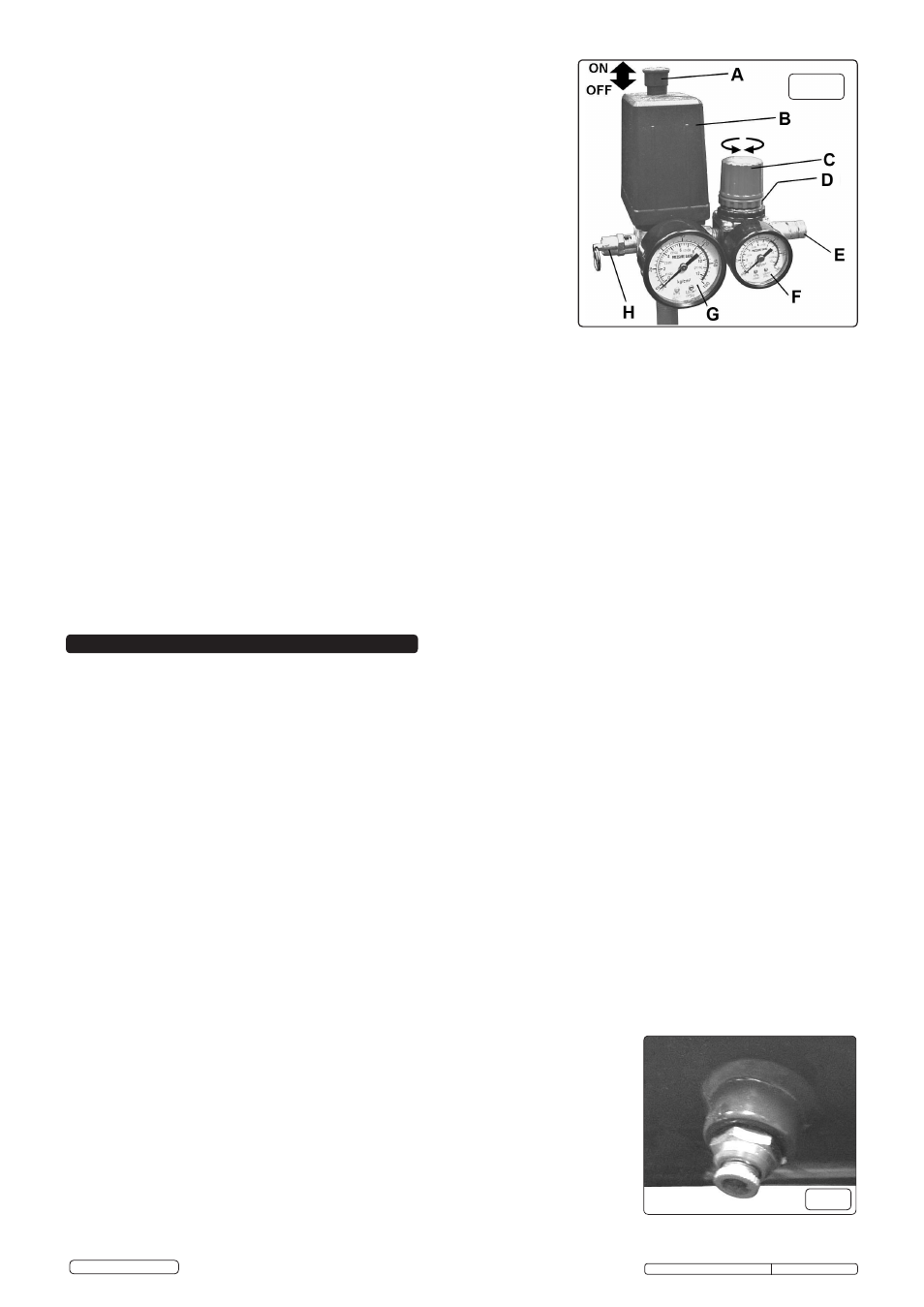
5. MAINTENANCE
In order to keep the compressor in good working condition, periodic maintenance is essential.
WARNING! Before performing any maintenance operation, switch off the compressor, disconnect from electrical supply and
release all air from the tank.
IMPORTANT! Failure to carry out maintenance tasks may invalidate the warranty on your compressor.
5.1. Operations to be carried out after the first 5 working hours:
a) Check that all nuts/bolts are tight, particularly those retaining the crankcase and cylinder heads.
5.2. Operations to be carried out after the first 100 working hours:
a) Replace the lubricating oil (see 5.6. below).
5.3.
Operations to be carried out daily:
a) Drain condensation by opening the valve located under the tank (fig.4). Place a container under the valve to collect any
condensation, as it may contain residual oil. Close valve after draining condensation and dispose of it safely.
b) Regularly clean dirt and dust away from the safety devices with a clean cloth or by blowing with low pressure compressed air.
Generally keep the compressor clean.
5.4. Operations to be carried out every 100 hours:
(or more frequently, if the compressor operates in a very dusty atmosphere)
a) Check oil level, top up if necessary.
b) Remove the filter elements. Turn off the compressor and using stored air from it's tank, clean the filters with compressed air. (Wear
eye protection and
DO NOT direct air towards the body or hands). DO NOT operate the compressor without the filters as foreign
bodies or dust could seriously damage the pump. Replace the filter elements.
c) Check for oil leaks.
5.5. Operations to be carried out every 200 hours:
a) Check the automatic cut-out at maximum pressure, and the automatic cut-in at 2 bar below maximum pressure.
b) Replace air filters (See 5.4).
5.6. Operations to be carried out every 400 hours:
a) Replace the lubricating oil. For oil specifications see below.
Remove the oil filler/breather plug (fig.2.A) then unscrew oil sight glass (fig.2.B). Drain oil into
a suitable container. Drain when the compressor is hot if possible, so that the oil drains rapidly
and completely. Incline the compressor to ensure complete drainage. Replace oil sight glass
and refill with fresh oil through the oil filler/breather aperture. Do not overfill. Replace oil
filler/breather plug.
WARNING! Never mix different oils and do not use non-detergent/low quality oils,
as the compressor may be damaged.
Recommended oils: Recommended oil for compressors, suitable for temperatures ranging
from +5°C to +25°C: SEALEY CPO or equivalent SAE 40 compressor oil.
WARNING! Dispose of waste oil only in accordance with local authority requirements.
b) Check all tube fittings and electrical connections.
c) Inspect pressure tank inside and out for damage or corrosion.
4.3.
STARTING THE COMPRESSOR.
4.3.1. The compressor is fitted with a push/pull type of ON/OFF switch (fig.3.A).
To turn the compressor ‘ON’ pull the switch knob upwards. To turn the
compressor ‘OFF’ push the switch knob downwards.
4.3.2. Check that the ON/OFF switch is in the “OFF” position and the regulator tap
(fig.3.C) is closed (Zero ‘0’ bar, Anti-clockwise).
4.3.3. Plug mains lead into mains supply and start the compressor by pulling the
ON/OFF switch knob upwards.
4.3.4. Leave the compressor running with the regulator tap (fig.3.C) set to maximum
pressure. Make sure that the pressure in the tank rises and that the compressor
stops automatically when the maximum pressure value allowed - written on the
specification plate and shown on the gauge (fig.3.G) - is achieved.
The compressor will now operate automatically. The pressure switch (fig.3.B) stops
the motor when the maximum tank pressure is reached, and will restart it when
pressure falls below the minimum threshold - approx. 2 bar (29psi) less than the
maximum pressure.
4.3.5. Stop the compressor by pushing the switch knob downwards (fig.3.A). The
compressed air inside the compressor head will flow out, making the restart easier
and preventing the motor from being damaged.
DO NOT, other than in an emergency, stop the compressor by switching off the mains socket, or by pulling the plug out of the socket,
as the pressure relief will not then occur and motor damage may result upon restart.
When the compressor runs correctly and is stopped correctly there will be:
(a) a whistle of compressed air when the motor stops,
(b) a protracted whistle (about 20-25 seconds) when the compressor starts with no pressure in the tank.
4.3.6. The output pressure is regulated by the pressure regulator tap (fig.3.C). Turn the tap clockwise to increase pressure and anti-clockwise to
reduce it. The tap can be locked at any required setting by tightening the locking ring (fig.3.D) up against the underside of the tap.
To determine the correct working pressure for any piece of equipment check the corresponding manual. When the compressor is not
being used, set the regulated pressure to zero so as to avoid damaging the pressure reducer.
NOTE: a) If the motor does not cut in and out, but runs continuously when using an air appliance, the capacity of the compressor may be too
small for the equipment or tool.
b) The larger gauge (fig.3.G) indicates the pressure inside the main tank. The smaller gauge (fig.3.F) indicates the pressure supplied to
the air equipment. Should the pressure in the main tank exceed the pre-set switch (fig.3.B) maximum, the safety valve (fig.3.H) will
activate.
WARNING! For this reason DO NOT tamper with, or adjust, the pre-set switch or safety valve (fig.3.B&H).
4.3.7. The compressor is fitted with an overload switch, and a reset trip button located in the connection box on top of the motor
(see fig.1.C & fig.6). Should the overload switch activate, switch the compressor off and leave for a few minutes before pressing the
trip reset button to reset, and then re-start the compressor. For possible causes of overload switch activation and remedies, see
Section 6.
fig.4
fig.3
Original Language Version
SAC10030.V2, SAC05030.V2 Issue: 1 - 14/05/13
© Jack Sealey Limited