Problem cause solution, Troubleshooting – Sealey 140XT User Manual
Page 4
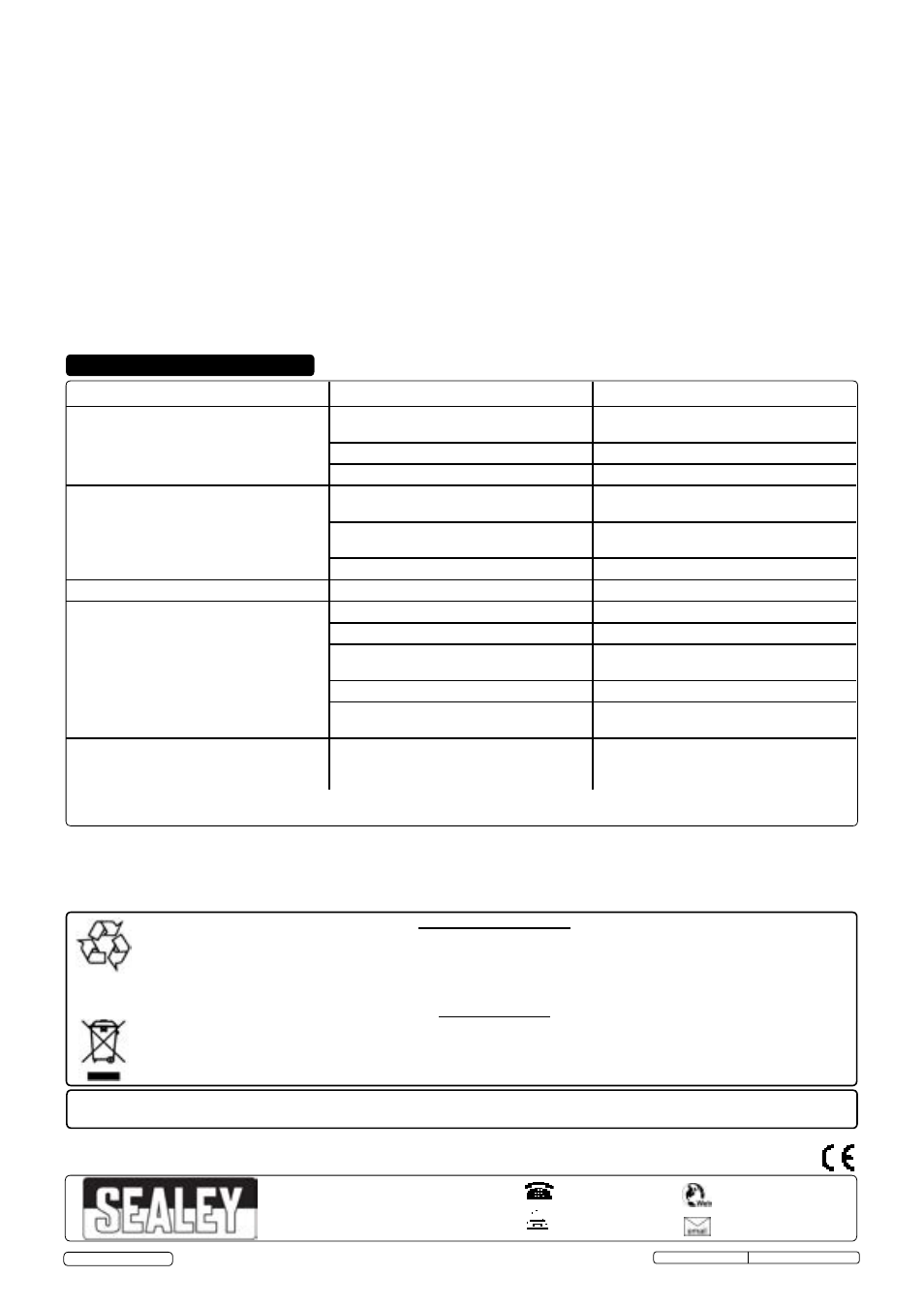
PROBLEM
CAUSE
SOLUTION
Power source fuse blown
Short circuit in either primary or secondary
transformer windings
Return to Sealey dealer for assessment/
repair
Electrode has touched earth clamp
Be vigilant to prevent this happening
Wrongly rated fuse
Install correct fuse
Welder frequently cuts out
The welder is being overworked causing the
thermostatic control to activate
Cut out will automatically reset when welder
has cooled
May also be due to a sticking electrode
Cut out will automatically reset when welder
has cooled
Broken fan causing overheating
Repair or replace cooling fan
Cooling fan not working properly
Starting capacitance disabled
Replace capacitior
Difficulty in striking or maintainig an arc
The electrode is damp
Heat it up to 60º - 70º before using
Wrong type of electrode
Use correct electrode
Bad connection between earth clamp and
workpiece
Grind connection area and reattach clamp
Regulation screw and nut worn out
Replace worn out parts
Partial short circuit in transformer windings
Return to Sealey dealer for assessment/
repair
Noise from within case when welding
Uneven gap between the moving iron core
and static iron core
Return to Sealey Dealer to have cores
adjusted
140XT.V2, 160XT.V2 Issue: 2 (SP) - 30/04/15
9. TROUBLESHOOTING
Environmental Protection
Recycle unwanted materials instead of disposing of them as waste. All tools, accessories and packaging should be
sorted, taken to a recycling centre and disposed of in a manner which is compatible with the environment.
When the product becomes completely unserviceable and requires disposal, drain off any fluids (if applicable)
into approved containers and dispose of the product and the fluids according to local regulations.
WEEE Regulations
Dispose of this product at the end of its working life in compliance with the EU Directive on
Waste Electrical and Electronic Equipment (WEEE). When the product is no longer required, it must be disposed
of in an environmentally protective way. Contact your local solid waste authority for recycling information.
NOTE: It is our policy to continually improve products and as such we reserve the right to alter data, specifications and component parts without prior notice.
IMPORTANT: No liability is accepted for incorrect use of this product.
WARRANTY: Guarantee is 12 months from purchase date, proof of which will be required for any claim.
01284 757500
01284 703534
Sole UK Distributor, Sealey Group,
Kempson Way, Suffolk Business Park
,
Bury St. Edmunds, Suffolk,
IP32 7AR
www.sealey.co.uk
Original Language Version
Parts support is available for this product. To obtain a parts listing and/or diagram,
please log on to www.sealey.co.uk, email [email protected] or telephone 01284 757500.
© Jack Sealey Limited
8.6.
Maintenance of the equipment. The equipment should be routinely maintained according to these instructions. All access and service
covers should be closed and properly fastened when the welding equipment is in operation. The welding equipment should not be
modified in any way except for those changes and adjustments covered in these instructions. In particular, the spark gaps of any arc
striking and stabilising devices should be adjusted and maintained according to the instructions.
8.7. Cables. The welding/cutting cables should be kept as short as possible and should be positioned close together, running at or close
to the floor level.
8.8.
Equipotential bonding. Bonding of all metallic components in the welding/cutting installation and adjacent to it should be considered.
However, metallic components bonded to the workpiece will increase the risk that the operator could receive a shock by touching
these metallic components and the electrode at the same time. The operator should be insulated from all such bonded metallic
components.
8.9.
Earthing of the workpiece. It is important that the workpiece is separately bonded to earth in addition to the welder/cutter return
cable. Where the workpiece is not bonded to earth for electrical safety reasons or because of its size and position, e.g. ship’s hull or
building steelwork, a connection bonding the workpiece to earth may reduce emissions in some, but not all instances. Care should be
taken to prevent the earthing of the workpiece increasing the risk of injury to others or damage to other electrical equipment.
Where necessary, the connection of the workpiece to earth should be made by a direct connection to the workpiece, but in some
countries where direct connection is not permitted, the bonding should be achieved by a suitable capacitance, selected according to
national regulations.
8.10. Screening and shielding. Selective screening and shielding of other cables and equipment in the surrounding area may alleviate
problems of interference. Screening of the entire welding/cutting installation may be considered for special applications.