Installation, Manual operation, Automated operation – Marwin Valve 3L/T 2100F-A Series 3-Way Ball Valve User Manual
Page 2
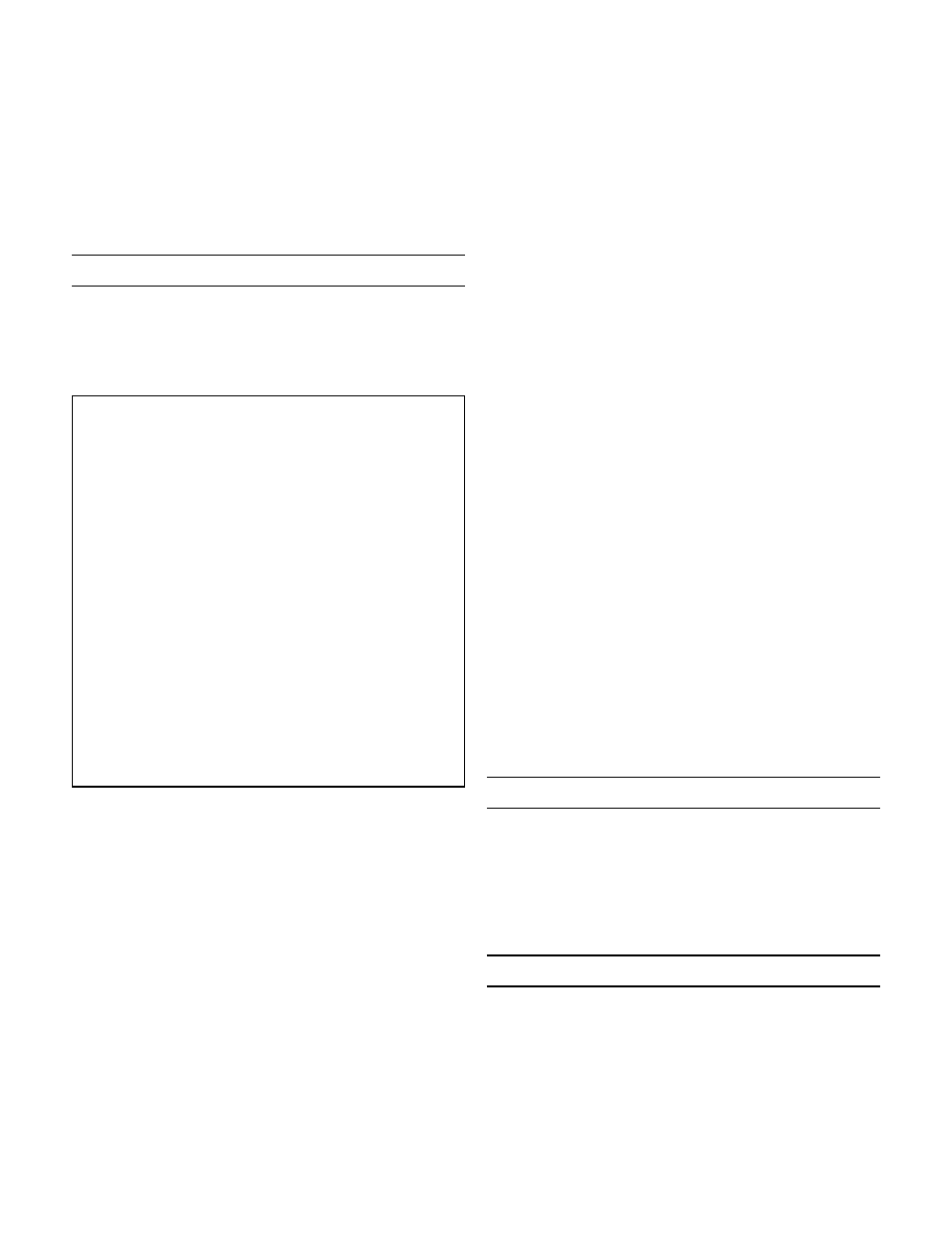
Maintenance During Storage Period
•
Internal surface should be inspected to check for
dust or other foreign objects.
•
Rust or dust must be removed by cleaning with
proper solvent.
•
After cleaning, ball valves must be lubricated with an
adequate lubricant.
•
Ball valves should be operated for at least two com-
plete cycles before installing or returning to storage.
Installation
The ball valves may be installed in any position using
standard pipe fitting practices. It is recommended
that unions be installed before each end of threaded
and welded multi-port valves for easy installation and
removal.
Caution: Before installation of the valve:
1. Pipe must be free of tension both during and
after installation.
2. Pipe must be flushed to clean dirt, welding resi-
dues, etc. which would damage ball or seats.
3. The valve should be kept in OPEN POSITION
during installation and protective plastic covers
should not be removed until the valve is installed.
4. Before shipment, the ball is lubricated with oil.
This can be easily removed with an application
compatible solvent if required.
5. If the valve was specified to be tested per ASME
16.34, there may be some trapped water be-
tween the ball and the body cavity. This can be
removed by partially opening the valve, thereby
exposing the cavity to the through port of the
ball.
6. When installing automated ball valves, insure that
the ball is in the proper position for the de-ener-
gized actuator.
Insure that the multi-port flow configuration is correct
before installing valve. Refer to the Marwin product bul-
letin for available flow (port) configurations. Flow direc-
tion can be found on the top of the stem.
Multi-port ball valves are generally not recommended for
throttling service because fluid now and the ball leading
edge can damage the resilient seats.
Installation of Threaded End Ball Valves
1. Unless otherwise specified, pipe threads are AMeri-
can National Standard Taper Pipe Threads (NPT) per
ANSI B1.20.1, and require that a pipe sealant be
used.
2. Use an anti-seize thread sealant to seal and prevent
galling
a. Marwin recommends PTFE-based liquid sealant
or Grafoil tape as thread sealants.
-2-
b. Use all pipe sealant products in accordance
with the manufacturer’s instructions and good piping
practices.
c. Correct lubrication of stainless steel pipe threads
is especially important to prevent galling.
3. To prevent distortion or damage to the valve, do
not apply torque through the valve. when tightening
valve, use wrench on the end nearest the pipe being
tightened.
4. Always leak test the system before using.
Installation of Flanged-End Ball Valves
1. Verify valve is in the full open position.
2. Use the appropriate size bolt and heavy hex nut.
3. Flange connection requires gasket (not included).
4. Follow gasket manufacturer’s recommended prac-
tice for tightening flange bolts.
Installation of Weld-End Ball Valves
To avoid overheating and damaging the body seals and
seats of weld end valves, the following procedure is
recommended:
1. Tack weld the valve in line.
2. Loosen end cap fasteners, spread pipe, and drop
the center section of the valve out of line.
3. Remove seats and seals from the end caps.
4. Weld end caps in line, using approved weld proce-
dure for the material.
5. Reinstall center section.
6. Check valve for body joint leaks during system pres-
sure test.
Note that this procedures require that the pipe can be
spread, or that provisions have been made to weld the
valve in a short section of removable pipe, and that a
repair kit be available so that the end cap seals can be
replaced if necessary.
Manual Operation
Reposition the valve by turning the handle one-quarter
turn (90°). The top of the stem shows the open ports.
Care must be taken to ensure valve open ports are
oriented as needed. The handle stops can be oriented in
90° increments. A special stop plate is required for 180°
rotation.
Automated Operation
A range of Marwin pneumatic and electric actuators are
available. Refer to the Marwin product bulletin for operat-
ing torques for actuator sizing. When automated, no stop
plate is fitted to the valve because the end stops are in
the actuator. Depending on the port configuration, the
pistons in spring return pneumatic actuators may need
to be reversed for counter-clockwise spring rotation to
insure the proper start/fail position.