Nexen Electronic Over Load Protection System Controller 964403 User Manual
Page 8
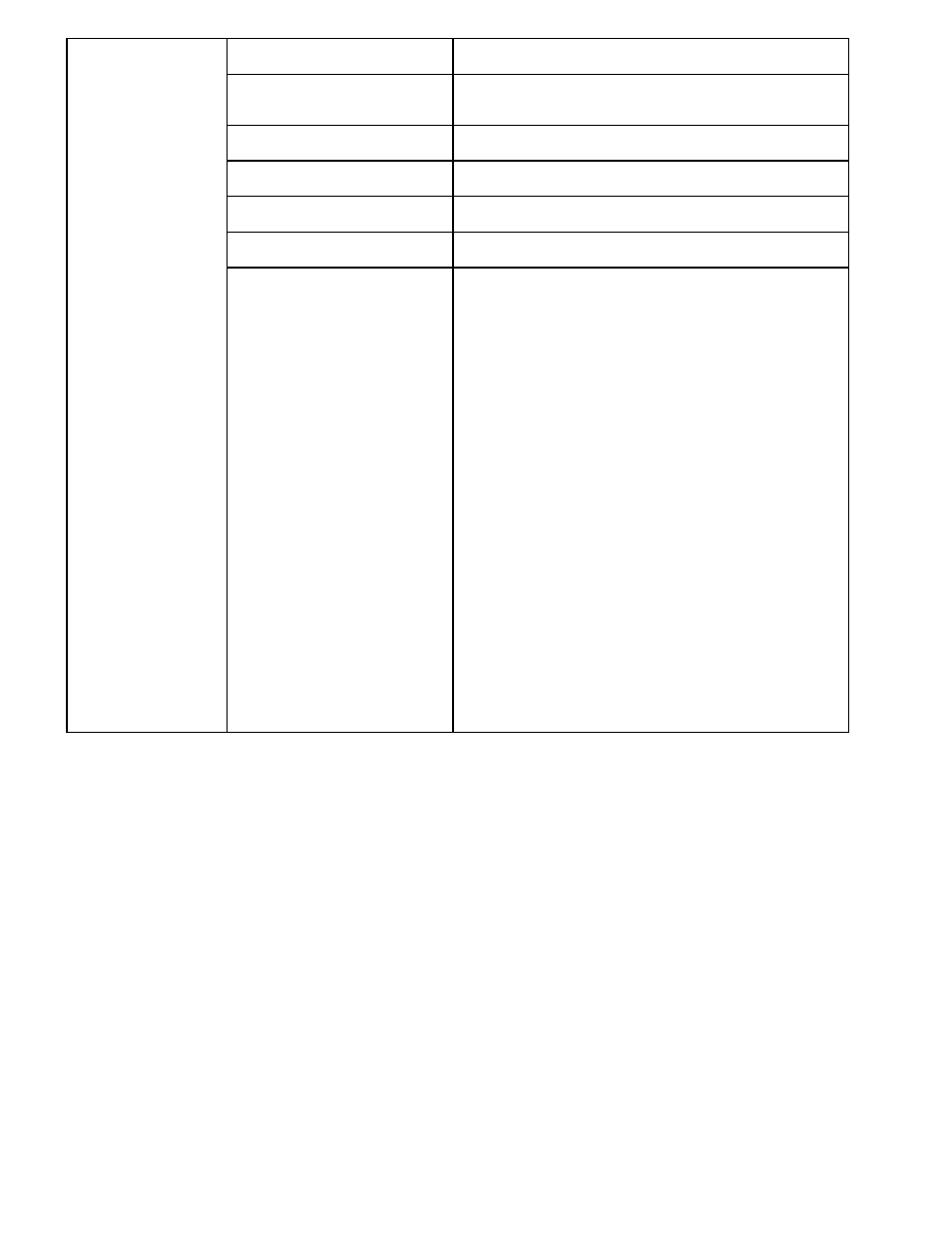
8
FORM NO. L-20309-A-1099
Continued from Page 7
Clutch disengages during
non-overload conditions.
Clutch size for the load.
Check clutch sizing to transmit required torque. Contact Horton Air
Champfi Technical Support (1-800-776-1AIR) for assistance.
Air pressure to the clutch.
Measure air pressure at the clutch while engaged to verify it can
transmit the required torque. Contact Horton Air Champfi Technical
Support (1-800-776-1AIR) for assistance.
Power supply to the OPS controller is
not being interrupted.
Measure the voltage to the OPS controller for adequacy and
non-interruption.
Sensor selection jumpers W1 and W2
are properly set.
Set jumpers W1 and W2 on the OPS printed circuit board to the
2 Wire Sensor position.
Electrical connections at the OPS
controller and clutch are tight.
Check all connections for tightness at the clutch’s electrical connector
and the OPS controller’s printed circuit board.
Air valve at the clutch is working
properly.
Examine the air valve on the clutch. Replace air valve if leaking.
Sensors in the clutch are functioning
properly.
Check the input and output shaft sensor’s yellow LEDs on the OPS
printed circuit board to see if they blink while the clutch is engaged and
turning very slowly. If the clutch turns too quickly, the LEDs will appear
continuously on but actually are blinking very fast. If both yellow LEDs
are blinking, suspect one of the previous problems. If none or one
yellow LED is blinking, a problem exists with one or both of the input
signals. Measure the voltage between terminals 1 (+) and 3 (-) and
between terminals 4 (+) and 6 (-) of J1. The supply voltage to the
sensors should be 12VDC or greater. Monitor the sensor signals
between terminals 2 (+) and 3 (-) and between 5 (+) and 6 (-) of J1.
While the clutch is engaged, jog the clutch and note the voltages at
these two places after the clutch stops. After several repetitions, the
voltages at these two places should vary between two states, 7.5VDC
and 1.0VDC, depending on whether a sensor sees a target or not
after the clutch stops. If a problem exists with this signal at connector
J1, monitor the same signals at the clutch’s electrical connector. This
time measure the supply voltage to the sensor between terminals 1 (+)
and 6 (-) and between terminals 3 (+) and 6 (-). Again the voltage
should be 12VDC or greater. Check the continuity in each line of the
signal cable. If a problem is detected in the cable, replace the cable.
Monitor the sensor signals at the clutch electrical connector terminals 2
(+) and 6 (-) and at terminals 4 (+) and 6 (-) as done previously. If a
problem exists with the sensor supply voltage or signals, suspect a
problem with the signal cable. Check the continuity of each line in the
signal cable and replace the signal cable if a problem is exists. If no
problem exists with the signal cable but the sensor signals are not
correct at the clutch’s electrical connector, the sensors are problematic.
Read the maintenance manual for the clutch and follow sensor
adjustment instructions. If readjusting the sensor(s) does not correct
the
problem, replace the sensor(s).