2 lubrication, 6maintenance, 1 general – Flowserve T-series Thrust Bearing Pot User Manual
Page 13
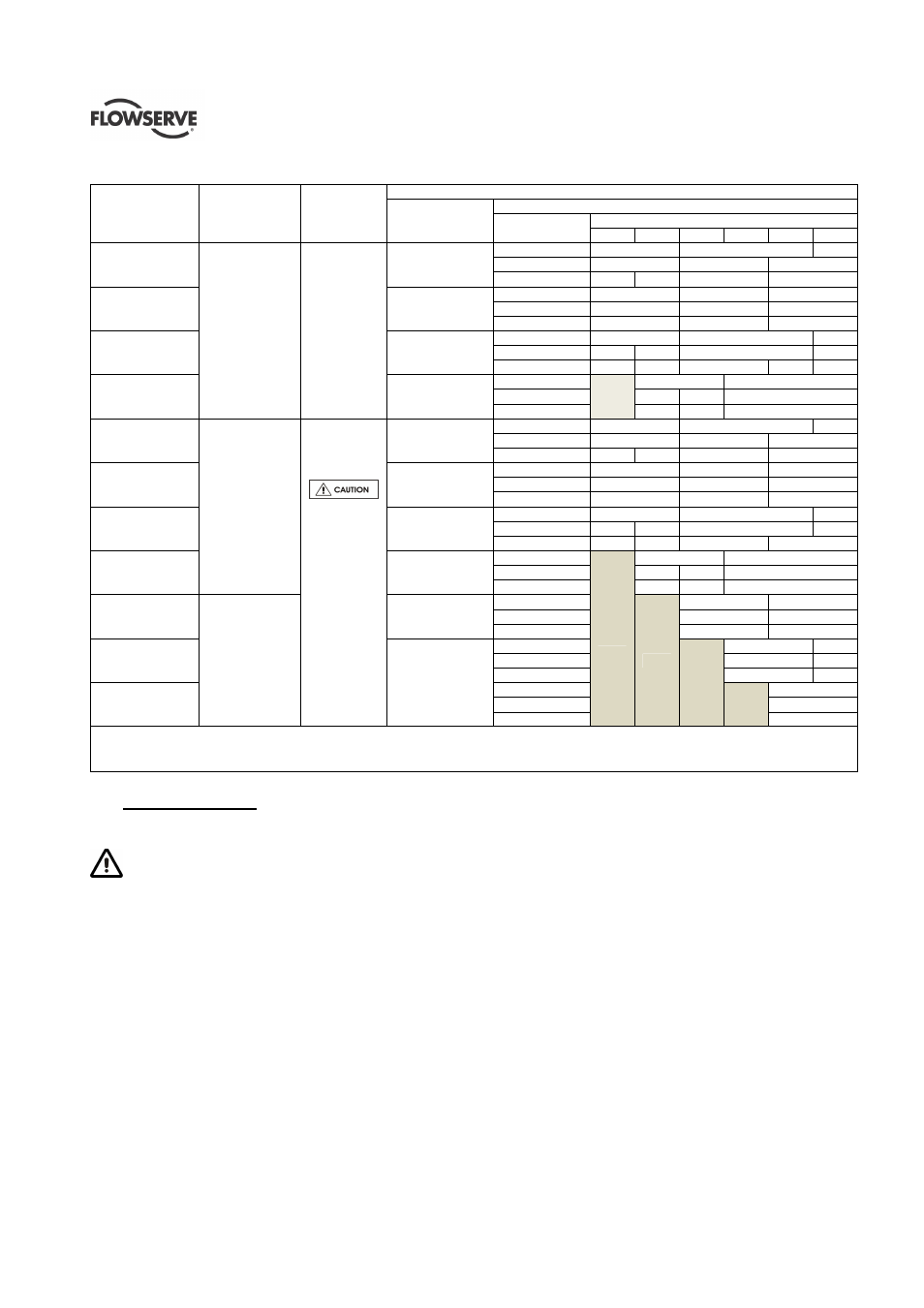
USER INSTRUCTIONS T-SERIES THRUST BEARING POT ENGLISH 26999907 01-2013
Page 13 of 24
flowserve.com
5.2 Lubrication
Size
Description
Cooling data
Lubrication data
Oil pan nominal
capacity
Litre (US pint)
Oil requirements
Oil temp
º C (º F)
Viscosity ISO VG @ min
-1
3 600 3 000 1 800 1 500 1 200 1 000
7211
Single row
angular contact
bearing
N
o
t
a
p
p
lic
a
b
le
0.13 (0.26)
60 (140)
22
32
46
70 (158)
32
46
68
80 (176)
32
46
68
100
7218
0.35 (0.74)
60 (140)
15
22
32
70 (158)
22
32
46
80 (176)
32
46
68
7318
0.6 (1.27)
60 (140)
15
22
32
70 (158)
15
22
32
46
80 (176)
22
32
46
68
68
7322
0.9 (0.90)
60 (140)
15
22
70 (158)
15
22
32
80 (176)
22
32
46
7211 & 6013
Single row
angular contact
and radial ball
bearings
Maximum
Pressure
3.0 barg
(43 psig)
Temperature
30 ºC
(86 ºF)
Flow
0.25 m
3
/h
(1.10 Usgpm)
0.35 (0.74)
60 (140)
22
32
46
70 (158)
32
46
68
80 (176)
32
46
68
100
7218 & 6020
1.0 (2.1)
60 (140)
15
22
32
70 (158)
22
32
46
80 (176)
32
46
68
7318 & 6022
0.9 (1.90)
60 (140)
15
22
32
70 (158)
15
22
32
46
80 (176)
22
32
46
68
7322 & 6028
1.3 (2.75)
60 (140)
15
22
70 (158)
15
22
32
80 (176)
22
32
46
29417 + 22217
Spherical roller
thrust and
spherical roller
bearings
1.2 (2.54)
60 (140)
22
32
70 (158)
32
46
80 (176)
46
68
29420 + 22220
5.75 (12.2)
60 (140)
22
32
70 (158)
32
46
80 (176)
46
68
29424 + 22224
60 (140)
22
70 (158)
32
80 (176)
46
•
For oil changes a dewaxed mineral oil with anti-oxidants, corrosion protection and anti-foaming additives should be used.
•
The first oil change should be after 100 hours operation. Subsequent oil changes after every 2 000 hours operation.
•
Oil consumption is negligible.
6
MAINTENANCE
6.1 General
It is the plant operator's responsibility to
ensure that all maintenance, inspection and
assembly work is carried out by authorized and
qualified personnel who have adequately
familiarized themselves with the subject matter by
studying this manual in detail. (See also section
1.6.)
Any work on the machine must be performed when
it is at a standstill
On completion of work all guards and safety
devices must be re-installed and made operative
again.
Before restarting the machine, the relevant
instructions listed in section 5, Commissioning,
start up, operation and shut down must be
observed.
Oil and grease leaks may make the ground
slippery. Machine maintenance must always
begin and finish by cleaning the ground and the
exterior of the machine.
If platforms, stairs and guard rails are required for
maintenance, they must be placed for easy access
to areas where maintenance and inspection are to
be carried out. The positioning of these
accessories must not limit access or hinder the
lifting of the part to be serviced.
When air or compressed inert gas is used in the
maintenance process, the operator and anyone in