Flowserve Gearex Rotary Gear Pumps External and Internal Bearing User Manual
Page 30
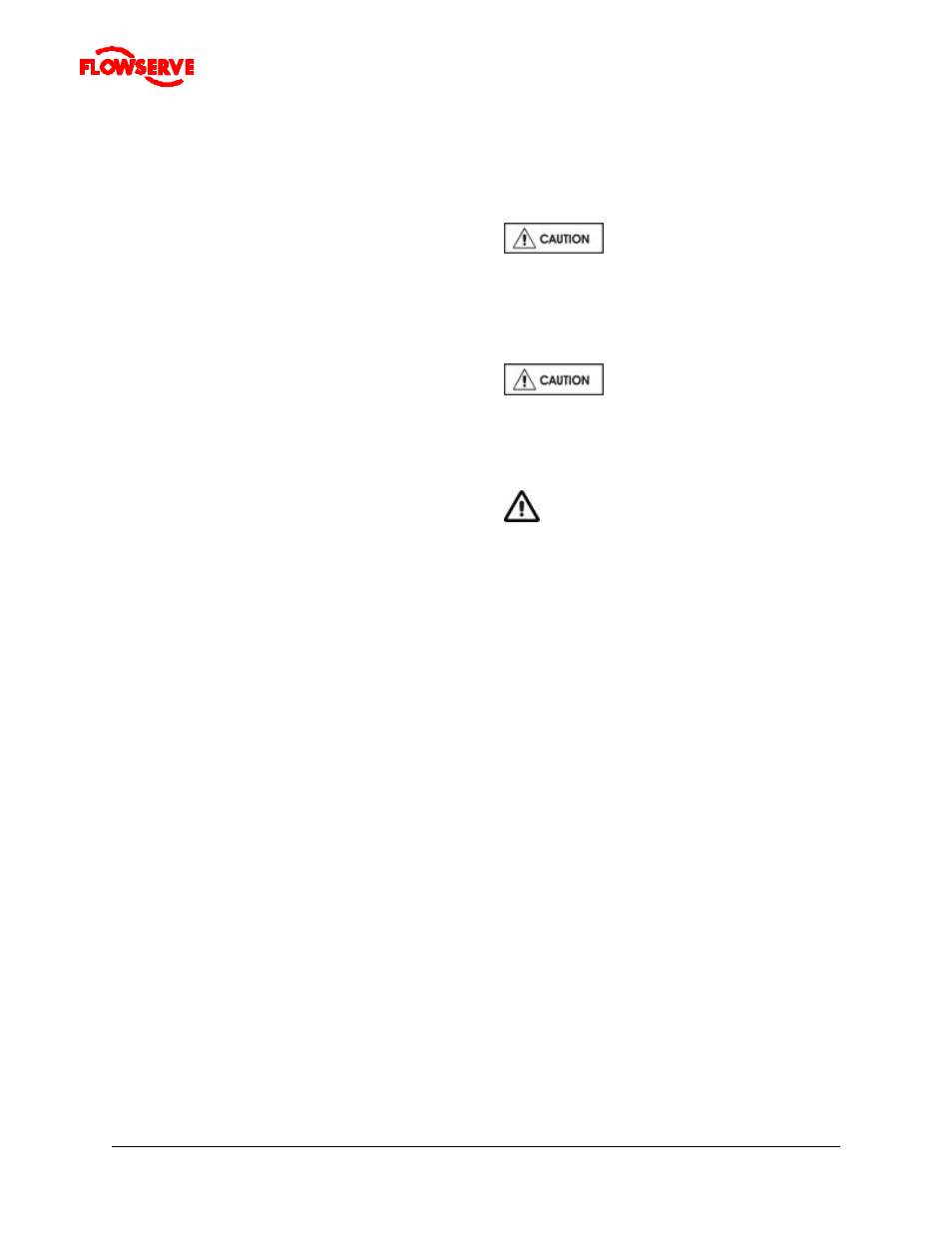
EXTERNAL GEAREX USER INSTRUCTIONS ENGLISH 71569246 (2167B-E1)
Flowserve Pump Division 30
®
Oils used in the bearing housing should meet the
following requirements.
1. Oxidation Stability Specification per AGMA
Standard 250.04 table 1, page 9.
2. Foam Suppression Specification per AGMA
Standard 250.04 table 1, page 9.
At initial start-up, oil must be drained completely and
replaced after one week or 100 hours running time
(except for temperatures above 121
°
C (250
°
F)).
For normal running temperatures between 10
°
and 65
°
C (50
°
and 150
°
F):
Indoor installations or outdoor summer conditions
with ambient temperature of –5
°
to 35
°
C (20
°
to 95
°
F).
Oil should meet AGMA Standard 250.04 AGMA
Lubricant No. 5, viscosity range 198 to 242 cST at
40
°
C.
Typical oils per Column "A" in Section 5.2.1. Change
oil every six months or seasonally.
For winter running temperatures between –18
°
and 38
°
C (0
°
and 100
°
F):
Cold Starting conditions with ambient temperatures
of –5
°
to 10
°
C (20
°
to 50
°
F).
Oil should meet AGMA Standard 250.04 AGMA
Lubricant No. 2EP, viscosity range 60 to 75 cST at
40
°
C.
Typical oils per Column "B" in Section 5.2.1. Change
oil every 6 months or seasonally.
For high temperature service between 60
°
and
120
°
C (140
°
and 250
°
F):
Oil should meet AGMA Standard 250.04 AGMA
Lubricant No. 7 (not compounded), viscosity range
414 to 506 cST at 40
°
C.
Typical oils per Column "C" in Section 5.2.1.
60
°
to 82
°
C (140
°
to 180
°
F) - change oil every
four months
82
°
to 104
°
C (180
°
to 220
°
F) - change oil every
two months
104
°
to 120
°
C (220
°
to 250
°
F) - change oil
every month
For temperatures above 120
°
C (250
°
F):
Same requirements as for high temperature service
between 60
°
and 120
°
C (140
°
and 250
°
F).
Initial start-up oil must be drained and replaced after
24 hours running time.
Change oil weekly.
5.3 Direction of rotation
Ensure the pump is given the same
rotation as the pump direction arrow cast on the
pump casing.
To avoid dry running the pump must either be filled
with liquid or have the flexible coupling disconnected
before driver is switched on.
If maintenance work has been carried
out to the site's electricity supply, the direction of
rotation should be re-checked as above in case the
supply phasing has been altered.
5.4 Guarding
Guarding is supplied fitted to the pump set. If
this has been removed or disturbed ensure that all the
protective guards around the pump coupling and
exposed parts of the shaft are securely fixed.
5.5 Priming and auxiliary supplies
Before starting any rotary pump it is absolutely
necessary that both the pump and suction line be
primed with liquid. This can be accomplished by one
of the following methods:
1. Remove pipe plug from discharge side of body
and install a temporary filling line. Pour
approximately 264 cubic metres (one gallon) of
the liquid being pumped into the pump through
this line while rotating the pump by hand in the
opposite direction from that shown on the
rotation arrow. This will cause the oil to work into
the pumping rotors to help seal while priming.
Turn temporary filling line down and direct into
the baseplate drip pan or some other suitable
container. Start the pump, running it in the
rotation shown on the rotation arrow. When a
solid stream of oil is achieved from the filling line,
stop the pump, remove the piping and replace
the pipe plug.
2. When the liquid supply level is above the pump
discharge valve, it is primed by opening the
suction and discharge valves. The in-flowing
liquid will displace the air and fill the suction line,
pump casing and discharge line up to the level of
supply.