Flowserve Gearex Rotary Gear Pumps External and Internal Bearing User Manual
Page 42
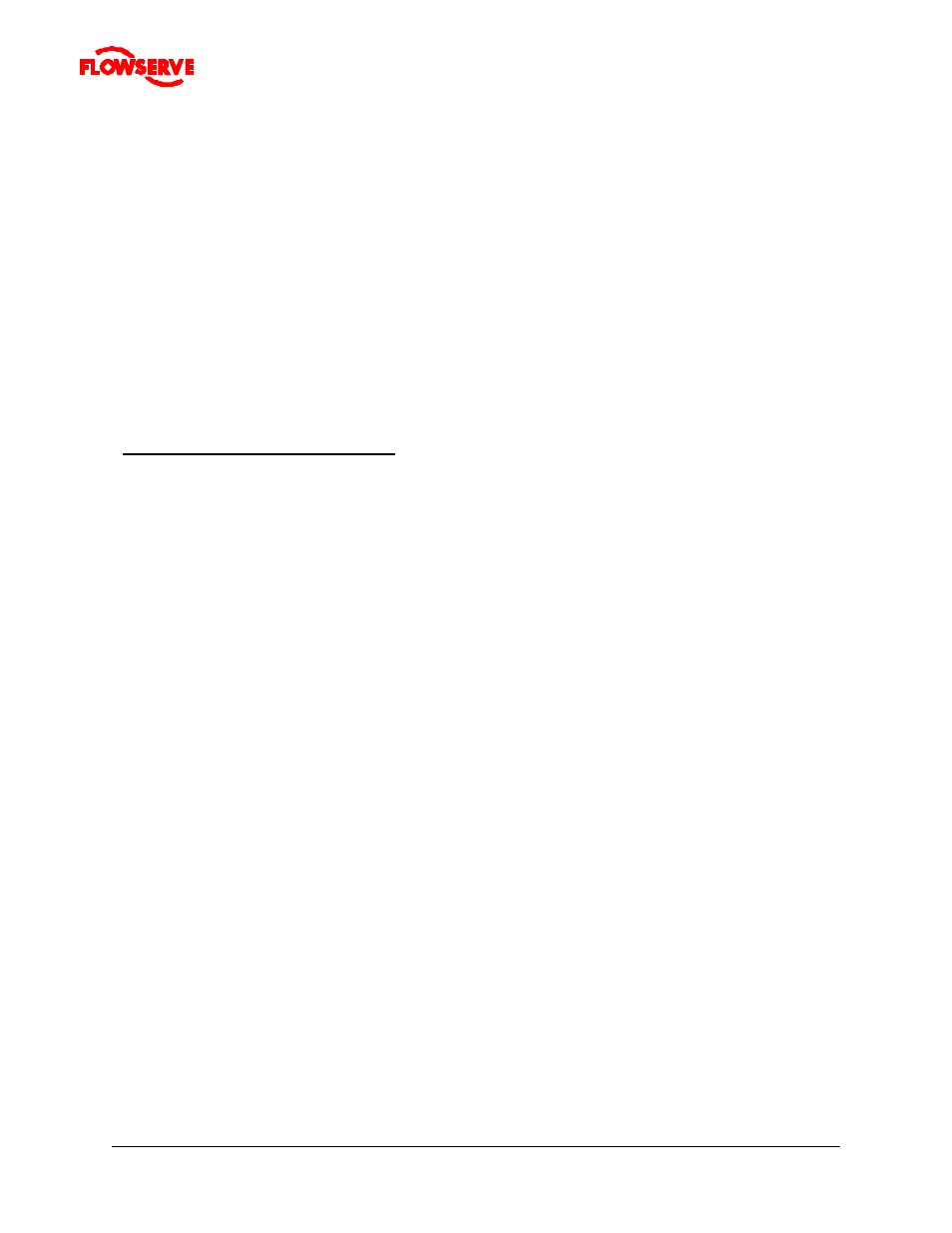
EXTERNAL GEAREX USER INSTRUCTIONS ENGLISH 71569246 (2167B-E1)
Flowserve Pump Division 42
®
the radial clearance between the rotors and the
body bores with a feeler gauge.
d) Using a large mallet move the front and rear
heads radially to equalize the clearance between
the outside diameter of the pumping rotors and
the body bores, checking for the pump to turn
freely.
e) Once the pump is turning freely, tighten all head
capscrews.
f) Continue with step r) in section 6.9.1, step q) in
6.9.2 or step s) in 6.9.3.
If the pump does not turn freely after executing this
procedure it is due to incorrectly dimensioned parts or
a timing problem. Contact the nearest Flowserve
Service Representative for assistance. Section Timing
Gear replacement, provides guidance in verifying the
timing of the rotating element.
7
TIMING GEAR REPLACEMENT
If new timing gears are to be installed on the rotating
elements, they must be timed before key slotting. The
reason for this is that the timing gear angular position
on the shaft determines, in part, the critical clearance
between the pumping rotors. Since the normal
clearance of meshing rotors varies with the size of
pump and viscosity of the fluid that the pump was
designed for, very accurate key slotting is essential for
proper operation. The original rotor clearances are
stamped on the pump body at the bracket flange.
This number represents the total clearance. One half
of it is the proper axial distance between the meshing
rotor teeth.
To replace the timing gears, the following procedure
should be used.
1. For optimum results it is highly recommended
that a set of timing stands as shown in Fig. 9 be
manufactured.
2. Mount the rotor shafts intermeshed onto the
timing stands resting the shafts on the bearing
diameters. The bearings are not mounted on the
shafts at this time.
3. Install the driven shaft timing gear key.
4. For “B” size units, proceed directly to step 15.
5. Slide the driven shaft timing gear partially onto its'
respective shaft diameter, engaging the key.
6. Slide the drive shaft timing gear partially onto its'
respective shaft diameter with the existing
keyway 180
°
away from the shaft keyway,
meshing with the driven shaft gear. (Fig. 6 & 7).
7. Place feeler gauges with a thickness equal to half
of the total side clearance on each side of the
rotor tooth on the drive shaft. This will eliminate
contact between the drive and driven rotors.
8. Rotate the drive shaft gear in the direction of
rotation of the pump until the teeth of both gears
are in contact. (Fig. 8).
9. Place the drive shaft gear key into the keyway at
a right angle to the shaft and against the timing
gear face. (Fig. 8).
10. Scribe a line on both sides of the key on the time
gear face. (Fig. 8)
11. Mark the position of the drive gear with respect to
the driven gear with 3 punch marks. (Fig. 8).
12. Remove the drive gear from the shaft and cut a
keyway the width as scribed.
13. Install the drive gear and key and intermesh with
the driven gear according to the 3 punch marks.
14. Slide the timing gear lockwashers onto the shafts
and fit the timing gear locknuts. Tighten securely.
15. Proceed to Reassembly step a).