3health and safety (cont.), 4preparation for installation – Flowserve Serck Audco Twin Isolation Plug Valve User Manual
Page 7
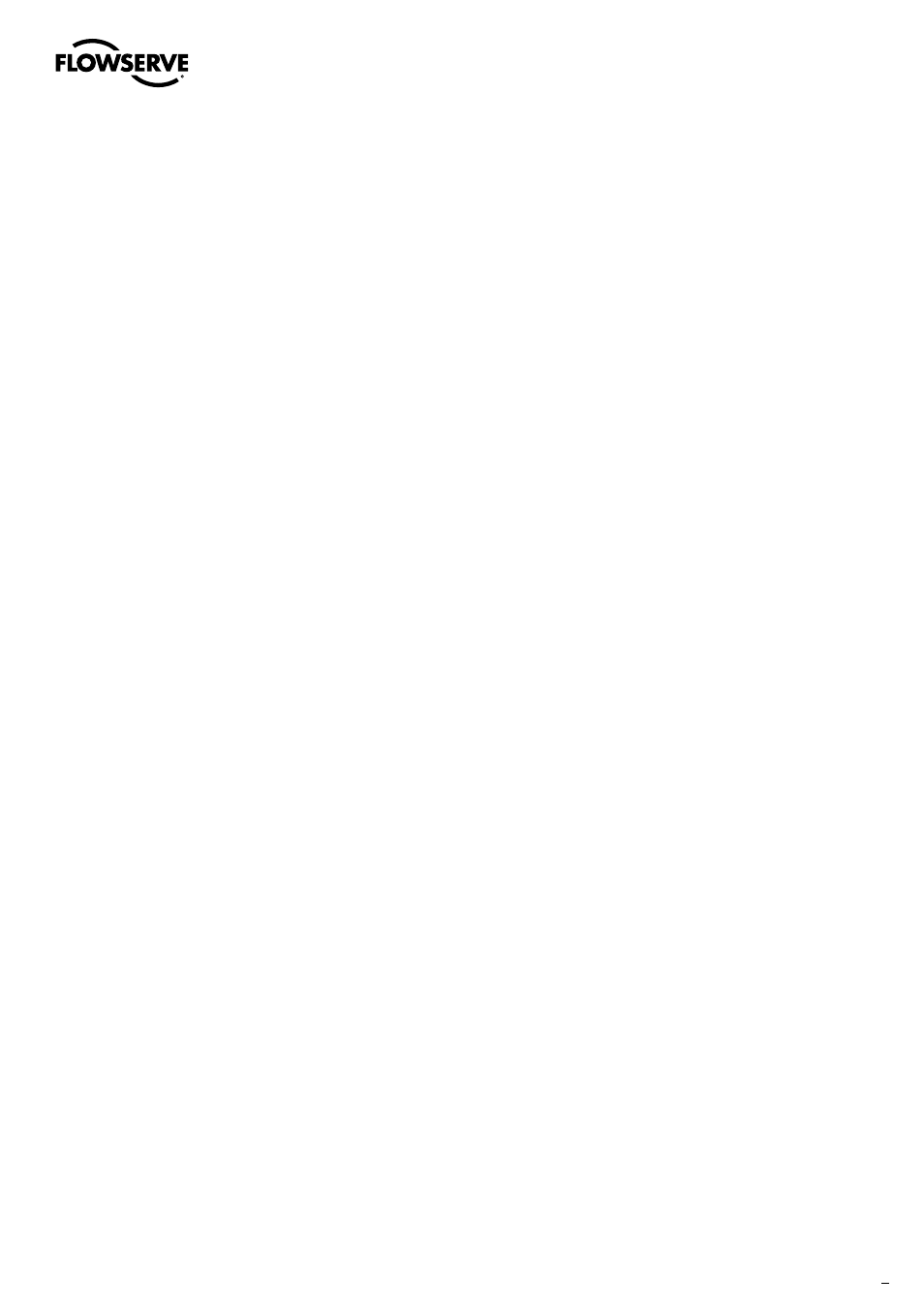
7
flowserve.com
Serck Audco TIPV Twin Isolation Plug Valve FCD - SRENIM0005-04 (A4) – 02/14
3
HEALTH AND SAFETY (cont.)
n)
End Flanges: The end flange design of this product has been verified by either:
ASME Boiler and Pressure Vessel Code Section VIII Division 1 calculation method;
Finite Element Analysis in accordance with ASME Boiler and Pressure Vessel Code Section VIII
Division 2 - Alternative rules;
Experimental testing as defined in BS EN 12516-3, Valve Design Strength - Part 3 Experimental
Method.
Gaskets: The gaskets used in all methods are Spiral Wound to BS EN 1514-2 for PN rated Flanges
and ASME B16.20 for Class rated flanges. These have Gasket Factors and Design Stresses of 2.5 and
10000 psi respectively for Carbon Steel gaskets, and 3.0 and 10000 psi respectively for Stainless Steel
gaskets, as defined in the ASME Boiler and Pressure Vessel Code Section VIII Division 1.
If gaskets are used with higher Gasket Factors and Design Stresses than those stated above,
please consult Serck Audco Valves Technical sales.
Bolting: End flanges for steel valves have been verified by the methods stated above, using bolt
design stress values based on those for ASTM A193 B7, B7M, B8, B8M as defined in ASME Boiler
and Pressure Vessel Code Section II - Materials - Part D - Properties.
o)
Lethal Service. In accordance with the design verification code (ASME Boiler and Pressure Vessel
Code Section VIII Division 1) a casting quality factor of 1.0 is allowable for all products except those
intended for ‘lethal service’. All products for such service must have had non-destructive examination
carried out in accordance with Appendix 7 of the code. Refer to Serck Audco Valves Technical sales.
p)
If the processes or environments that the products are used in are likely to cause temperatures
(high or low) that may cause injury to personnel if touched, then adequate insulation/protection must
be fitted. It is recommended that the insulation allows easy access for maintenance, to the sealant
and stem packing compound fittings, and to the valve operator.
q)
If the equipment is to be used on unstable gas duty, ensure that the operational parameters as
indicated on the product identification plate cannot be exceeded.
r)
This equipment should be protected by other devices to prevent over-pressurisation.
(i.e. caused by external fire, etc).
s)
This equipment must be installed in a system that is designed to prevent excessive forces acting
on the flanges, connections, etc.
4
PREPARATION FOR INSTALLATION
All protective packaging must be removed before installation.
It is recommended that additional sealant be injected prior to re-test and operation so as to ensure
tight shut off, it is also recommended to re-energize the injectable stem packing compound.
Any excess sealant found around the plug port should be removed by using a scraper.
Clean end connections to remove any unwanted paint or rust inhibitor.
Significant problems can arise with any valve installed in an unclean pipeline.
Ensure that the pipeline has been flushed free of dirt, weld spatter, etc. before installation.
The working area should be clean and clear of any debris which could contaminate the valve.
The valve should be fully opened or fully closed during cleaning operations.
Water and inert gases such as carbon dioxide and nitrogen are unlikely to affect the sealant.
If solvents or steam cleaning are used, it is recommended that the valves are reinjected with sealant
after completion of the cleaning operation.