Operation, Emergency operation, Maintenance – Flowserve BA46 User Manual
Page 28
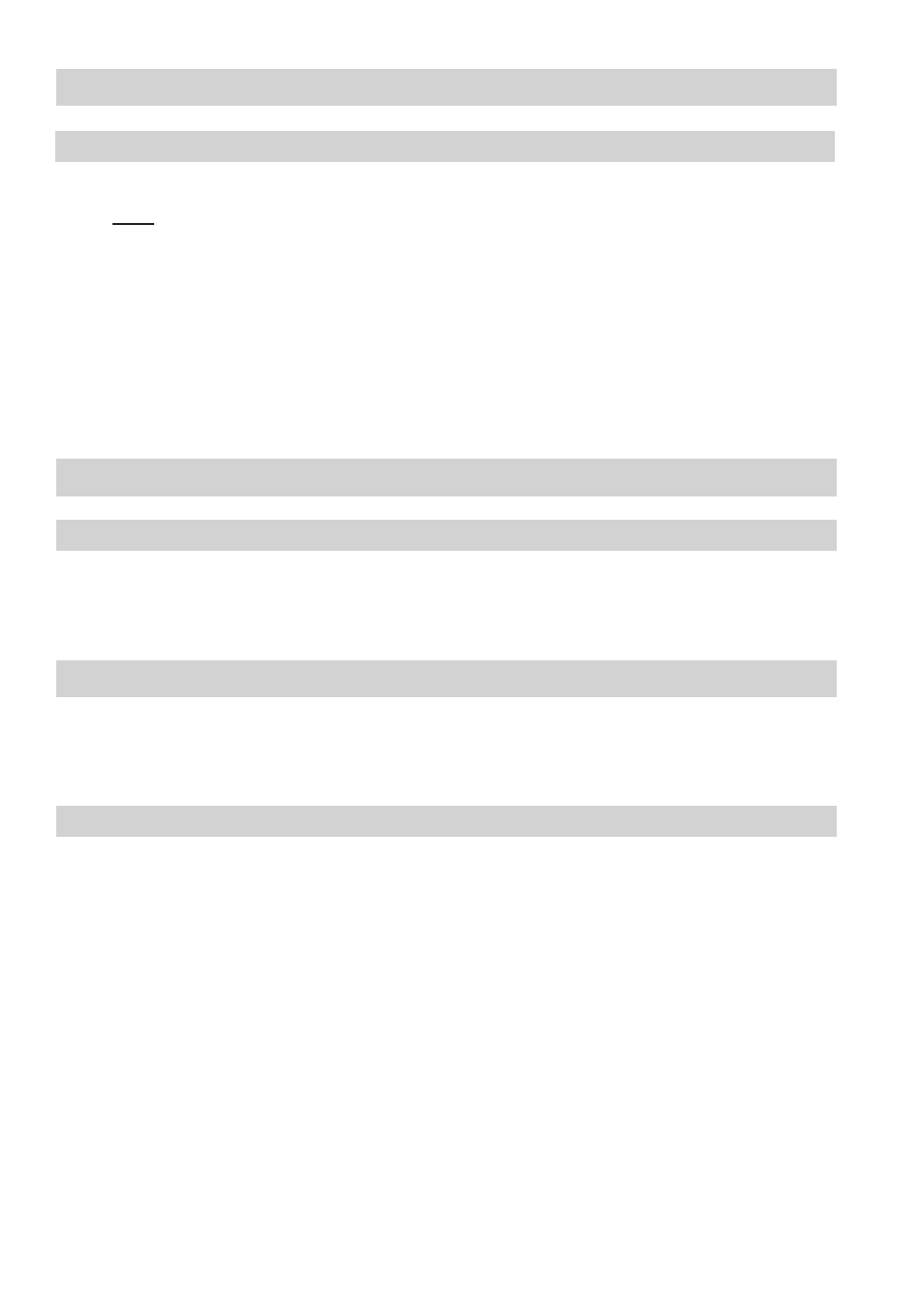
8
Calculating the amount of boiler blowdown
Amount of boiler water to be discharged
A = Q · S
K – S
A = Amount of boiler
blowdown [kg/h]
Q = Boiler capacity [kg/h]
S = Conductivity of feedwater
[
µs/cm]
K = Admissible conductivity of
boiler water [
µs/cm]
Example
Boiler pressure: 5 bar
Nominal size of the continuous blowdown valve: DN 0
Boiler capacity:
Q = 0000 kg/h
Conductivity of feedwater:
S = 00 µs/cm
Admissible conductivity of the boiler water:
K = 3000 µs/cm
Amount of boiler water to be discharged:
A ≈ 345 kg/h
0 % of which is intermittently blown out:
≈ 35 kg/h
Amount of continuous blowdown:
A
1
≈ 30 kg/h
Set control lever according to scale to an opening of 4 %,
Fig. 6
Operation
– continued –
Emergency Operation
BAE 46, BAE 47
.
Cut off power supply to the actuator and lift the coupling
8
approx. cm by hand
.
Fig. 13
.
Use the scale
S
on the control lever
U
to set the desired blowdown rate,
Fig. 13
Take heed of the danger note on page 5.
. Unscrew the hexagon nut
T
and detach control lever
U
with the aid of a pulling device.
3. Undo stuffing box screws
A
, remove stuffing box gland
C
, scale plate
B
, disk springs
D
and spring sleeve
E
.
4. Unscrew nozzle stem
R
and pull is out of the valve body.
5. Unscrew locking screw
P
and remove gasket
Q
.
6. Unscrew sealing plug
O
and remove gasket
N
.
7. Use a brass drift punch d = 4.8 mm to force out the internals
F
to
J
,
Fig. 14
8. Clean and, if required, exchange valve body
K
and internals.
9. Apply glue “Loctite
®
60” to seat bushing
J
and put it in place. Insert stage bushing
I
.
0. Align wearing bushing
H
in such a way that the groove is on the longitudinal axis of the locking
screw
P
.
. Screw in the locking screw
P
together with gasket
Q
and tighten it with a torque of
5 Nm (DN 5 – 3) or 11 Nm (DN 40, 50) when cold.
. Align and insert the guide sleeve
G
in such a way that the groove on the longitudinal axis is
on the locking screw
P
,
Fig. 12.
3. Insert new wiper rings and packing rings
F
as shown,
Fig. 12.
4. Apply lubricant (type WINIX
®
00) to the thread and sealing surface of the nozzle stem.
Changing packing and internals of BA 46, BA 47
Maintenance
The continuous blowdown valves BA 46, BA 47, BAE 46, BAE 47 do not require any special maintenance.
Depending on the quality of the boiler water it might be necessary to service the valve every one or two
years.