Adjustment of tightness of spool brake, Shielding gas – Kemppi Pulse 2800 MVU User Manual
Page 7
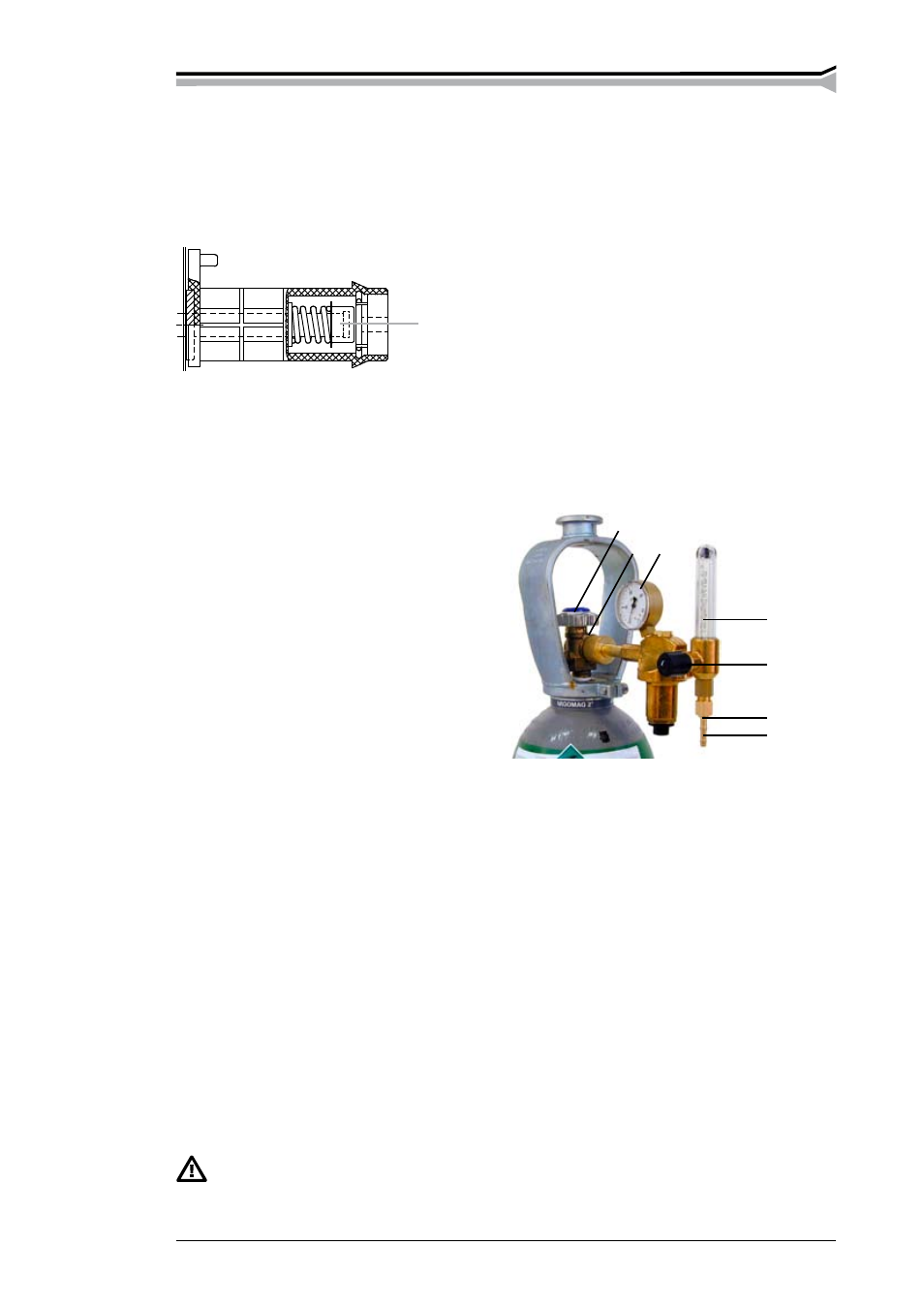
Kempact™ pulse 800 mVu automotiVe / 0709 – 7
© Kemppi oy
2.10. ADjUSTMENT OF TIGHTNESS OF SPOOL BRAkE
Brake force can be adjusted through the hole in the spool hub’s locking device of spool hub by
screwing the control screw with a screwdriver. Adjust the braking force so that it is sufficient to
prevent the wire from becoming too loose on the spool and spilling when the spool stops rotating.
The greater the wire feed speed, the greater the braking force required. Do not keep the brake
unnecessarily tight, since this will impose a strain on the motor.
2.11. SHIELDING GAS
The MIG shielding gas consists of carbon dioxide, mixed gases and argon. Shielding gas flow
rate is determined by the amount of welding current. The typical flow rate of gas in the welding
steel is 8-15 l /min.
The following installation instructions are valid for most gas flow regulator types:
1. Step aside and open the bottle valve (A) for a while to blow out possible impurities.
2. Turn the press regulation screw (B) of the regulator until no spring pressure can be felt.
3. Close the needle valve if there is one in the regulator.
4. Install the regulator onto bottle valve and tighten the connecting nut (C) with a wrench.
5. Install the hose spindle (D) and jacket nut (E) into the gas hose and tighten with a hose
clamp
6. Connect the hose with the regulator and the other end with the wire feed unit. Tighten jacket
nut.
7. Open the bottle valve slowly. The gas bottle pressure meter (F) shows bottle pressure.
Note! Do not use the whole contents of the bottle. The bottle pressure should be filled when
bottle pressure is 2 bar.
8. Open the needle valve if there is one in the regulator.
9. Turn the regulation screw (B) until the hose pressure meter (G) displays the required flow
(or pressure). When regulating the flow amount, the power source should be switched on
and the ”GAS PURGE” -switch pressed simultanously.
Close the bottle valve after welding is finished. If the machine will not be in use for a long time,
unscrew the pressure regulation screw.
Always fasten the gas cylinder securely in an upright position on a wall rack intended
for the purpose or on a cylinder cart. Always close the cylinder valve after you have
finished welding.
A
Gas bottle valve
B
Press regulation screw
C
Connecting nut
D
Hose spindle
E
Jacket nut
F
Gas bottle pressure meter
G
Gas hose pressure meter
E
B
D
C
A
F
G
A